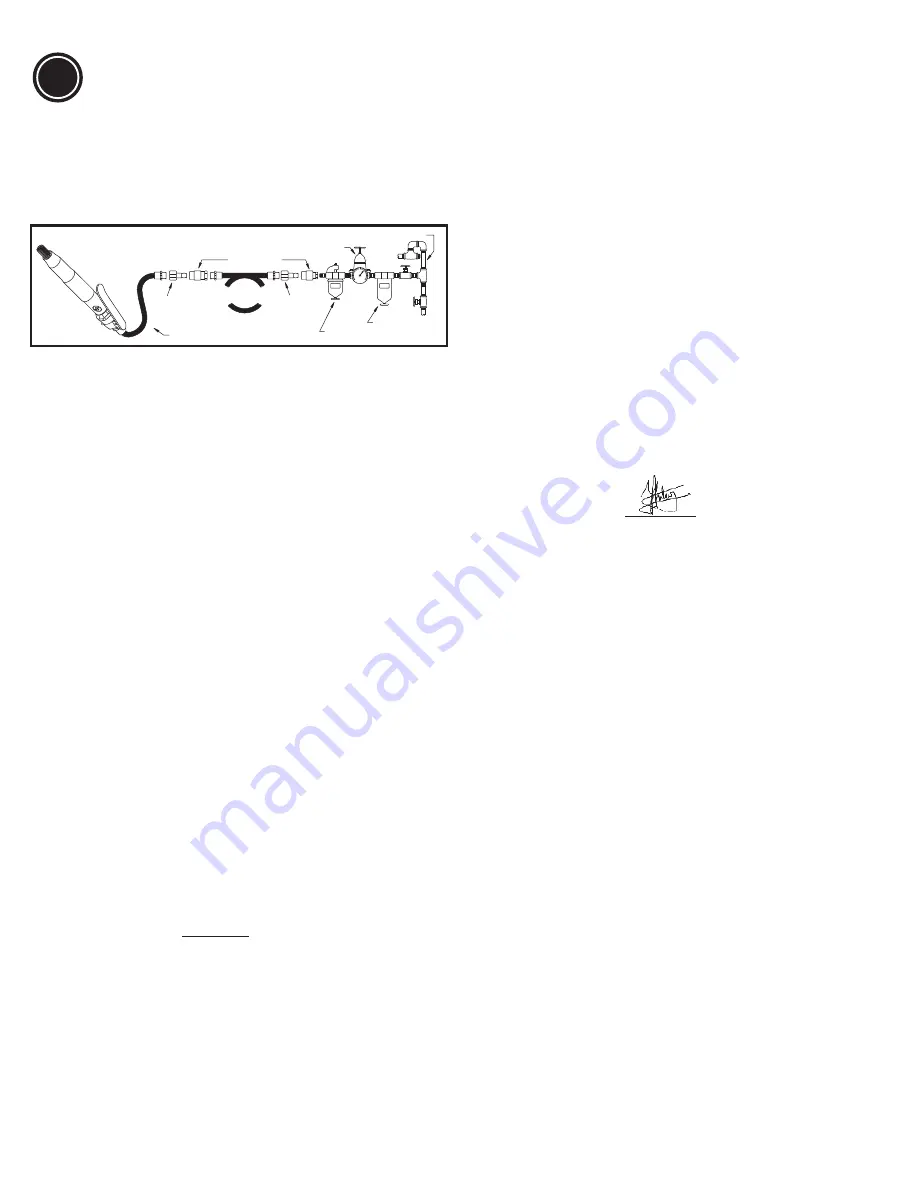
Copyright 2004, Chicago Pneumatic Tool Company
All rights reserved. Any unauthorized use or copying of the contents or part thereof is prohibited. This applies in particular to trademarks,
model denominations, part numbers and drawings. Use only authorized parts. Any damage or malfunction caused by the use of
unauthorized parts is not covered by Warranty or Product Liability.
CP7120
Needle Scaler
INSTRUCTION MANUAL
Air Supply Requirements
1. Supply tool with 90 psig (6.2 bar) of clean, dry air. Higher
pressure drastically reduces tool life.
2. Connect tool to air line using pipe, hose, and fitting sizes
shown in the diagram.
Lubrication
1. Use an air line lubricator with SAE #10 oil, adjusted to two (2)
drops per minute. If an air line lubricator cannot be used, add
air motor oil to the inlet once a day.
2. The use of synthetic oils for air line lubrication is not
recommended because of possible damage to seals, o-rings,
hose, rotor blades and polycarbonate oiler/filter bowls.
Operation
For Needle Scaler
1. Push in the front assembly and twist to the open slot, then
pull needle assembly out of housing.
2. Remove worn needles from holder and replace with new
needles, making sure the needle heads fit into the
countersunk holes in needle holder.
3. Slide needles through spring and front nosepiece. Check that
driver is not damaged and placed inside housing correctly.
4. Lubricate entire needle assembly with a light coating of oil.
Reassemble by sliding assembly into the housing, line up
slot, then push in and twist to lock in place.
For Chisel Scaler
1. To insert chisel, press loop on retainer aside, push chisel into
cylinder and release loop.
2
.
Place cutting edge of chisel against workpiece, depress
trigger.
c
Caution: Do not operate tool without chisel in cylinder,
or allow the chisel to be driven out of cylinder. Internal
damage will result if piston is allowed to strike cylinder
wall.
Maintenance
1. Disassemble and inspect air motor every three months if the
tool is used every day. Replace damaged or worn parts.
2. High wear parts are underlined in the parts list.
3. Dirt or gum deposits cut tool power. To correct this, flush out
the tool with gum solvent oil or an equal mixture of SAE #10
oil and kerosene. If outside conditions are in order,
disassemble tool, replace worn or damaged parts, clean,
reassemble and relubricate.
English
EN
EC DECLARATION OF CONFORMITY
We, Chicago Pneumatic Tool Company, 1800 Overview
Drive, Rock Hill, SC 29730 USA, declare under our sole
responsibility that the product to which this declaration
relates, is in conformity with the requirements of the Council
Directive of June 1998 on the approximation of the laws of
the Member States relating to machinery (98/37/EC).
Machine Name
CP7120 Needel Scaler
Machine
Type
Power tool with 1/2” sq. shank for use
with chisel and various 1/2” sq. shank accessories,
Needles - No other use is permitted.
Serial
No.
Tools with No. 04200P or higher
Technical
Data
1/2” sq. shank
Air pressure 90 psi (6.2 bar)
Harmonized
Standards
Applied
EN292
National
Standards
Applied
ISO 8662-14,
Name
And
Position
Of
Issuer
Yves Antier, General
Manager, Chicago Pneumatic Tool Company
Signature
Of
Issuer
Place
And
Date
Of
Issue
Rock Hill, SC 29730 USA,
October 31, 2004
Noise & Vibration Declaration*
Sound pressure level 99 dB(A),uncertainty 3 dB(A), in
accordance with ISO 15744-2002. For sound power, add
11 dB(A).
For Needle Scaler
2
Vibration value 9.7 m/s , re. ISO 8662-14.
For Chisel Scaler
2
Vibration value 15.6 m/s , re. ISO 8662-14.
*These declared values were obtained by laboratory
type testing in compliance with the stated standards and
are not adequate for use in risk assessments. Values
measured in individual work places may be higher than
the declared values. The actual exposure values and risk
of harm experienced by an individual user are unique
and depend upon the way the user works, the workpiece
and the workstation design, as well as upon the
exposure time and the physical condition of the user.
We, Chicago Pneumatic, cannot be held liable for the
consequences of using the declared values, instead of
values reflecting the actual exposure, in an individual risk
assessment in a work place situation over which we have
no control.
ISO15744-
2002
1/2" (12 mm)
3/8" (10mm)
3/8" (10mm)
3/8" (10mm)
CA048361 (1/2")
CA048362 (1/2")
CA048360 (1/2")
3/8" (10mm)
3/8" (10mm)