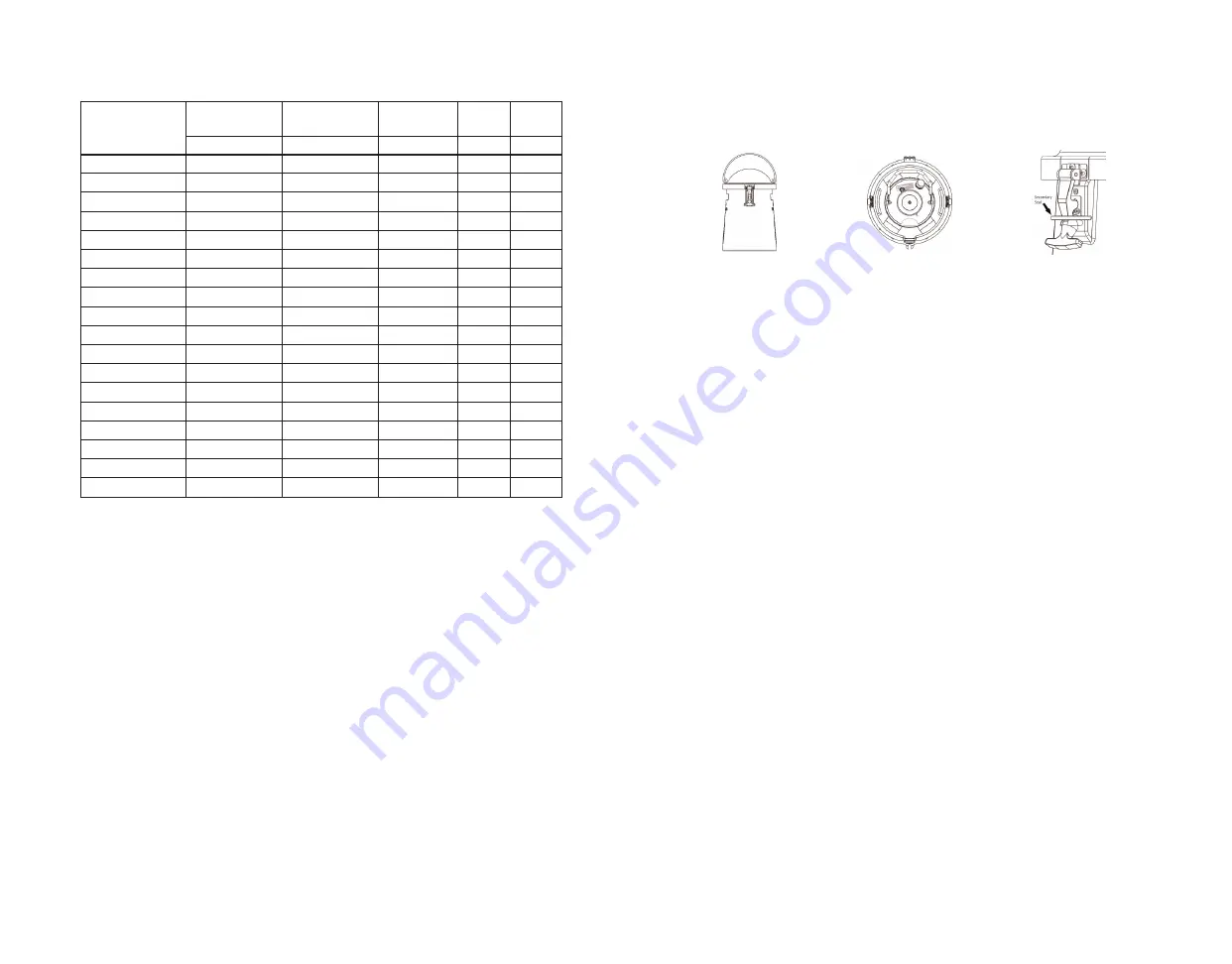
15
your asset from being tampered during shipment. Before putting PPSC into service, inspect it for any
damage that may jeopardize its functionality. Replace any aged/worn-out impact absorption foam
cushion inside the PPSC or any defective hardware. Remove badly damaged PPSCs from service.
Contact Customer or Technical Service for assistance in selecting the proper service parts.
Select the appropriate shipping method based on the value of contents. Common carriers handle
packages very roughly with the most stable side of the packaging down, and should be used for
low-value product shipment only. Contact carriers for shipment methods for their recommendation
on transporting valuable and/or irreplaceable contents.
MVE Vapor Shippers were primarily designed as vapor shipping containers, however, they can also
be used for immersion of samples. It is imperative that all liquid nitrogen be removed so the unit
remains classified as a Vapor Shipper for transport. If liquid nitrogen is visible in the bottom of the
inner, it then becomes a liquid shipper and the exception status is void. The liquid inside is now
classified as hazardous material.
GENERAL CLEANING
Do not use any petroleum based cleaning solution.
Inside of the vessel:
Any cleaning solution that does not react with aluminum, stainless steel, or G10 composite can be used
in the sanitation process of a MVE Vapor Shipper. In most cases, any household detergent or mild soap
solution is suitable. Other cleaners and disinfectants that can be used safely include hydrogen peroxide,
chlorine/water mixture, and denatured alcohol. The generally accepted practice of using 10% chlorine
bleach with 90% water solution holds as the best method for decontamination. It is recommended that
the unit is filled to its full capacity with the cleaning solution mixture, agitated, and then thoroughly
rinsed. It is important that all surfaces being sanitized are thoroughly rinsed and that all cleaner solution
residues are removed after cleaning. Allow the unit to dry completely before putting into service. It is
suggested that the unit is inverted to drain and dry completely.
Outside of the vessel:
Use light dampened cloth of mild soap solution.
PREVENTIVE MAINTENANCE
The owner may follow two methods of maintenance, Continuous and/or Annual.
For Continuous Maintenance (Recommended before each shipment):
If the tank is warm follow steps 1 - 3 under OPERATION section above but allow the unit with full
liquid to stand undisturbed for 2 hours. Verify no major frost or condensation on outside of unit.
Frost or condensation on the outside of unit would indicate either a weak or no vacuum. Inspect the
cork and cover for signs of damage that may affect NER and Hold Time. Inspect the outside of the
tank for signs of shipping damage, such as large dents, especially around the neck tube area.
Remove badly damaged tanks from service.
14
SHIPPING INSTRUCTIONS
MVE/Chart recommends the plastic protective shipping containers (PPSC) be used to help keep the
Vapor Shipper in the upright position and reduce the risk of damage to your valuable asset.
DO NOT
SHIP UNIT ON ITS SIDE OR UPSIDE DOWN. SHIPPING THE UNIT IN ANY POSITION OTHER THAN
UPRIGHT COULD REDUCE THE HOLD TIME TO LESS THAN 10% OF STATIC HOLD TIME, AND CAUSE
PERMANENT DAMAGE TO THE UNIT AND LOSS OF INVENTORY.
This could also void warranty.
WARNING:
If you ship the Vapor Shipper in a cardboard box, it will ship on its side, as common
carriers instruct their employees in sorting facilities to place boxes on conveyors with the most
stable side down.
Charge the unit by following all steps listed in OPERATION section before inserting into the PPSC. To
avoid damage to either the Vapor Shipper or PPSC never fill or dump the unit when inside the PPSC.
Fasten all locking latches tightly before shipping. You can also utilize cable tie, tamper proof security
seal, or any other appropriate secondary locking mechanism around existing locking latches to avoid
Empty
Charged
Static
Weight
Weight
Hold Time
lbs (kg)
lbs (kg)
Days
L/Day
certified
SC 2/1V
6 (2.7)
8.3 (3.7)
8
0.19
N
SC 4/2V
10.3 (4.6)
16.7 (7.5)
13
0.26
Y
SC 4/3V
11.5 (5.2)
18.5 (8.3)
21
0.20
Y
SC 20/12V
25.3
(11.4)
40.2
(18.2)
60
0.09
N
XC 30/12V
44
(20)
76
(34)
82
0.22
N
Cryoshipper
25.7
(11.6)
38.2
(17.3)
10
0.85
Y
Cryoshipper XC/IATA
32.3
(14.6)
48.9
(22.1)
14
0.70
Y
Cryoshipper 2000
65
(29.5)
95
(43.1)
15
0.79
N
Cryomoover
31
(14)
40.4 (18.3)
12
0.35
N
Cryoshipper MINI*
*
*
*
*
*
0.84
N
Mini-Moover
8.5
(3.8)
13.4 (6.0)
14
0.20
N
XC 20/3V
25.1 (11.3)
36 (16.3)
16
0.35
N
Doble 11
14.3
(6.4)
19.5
(8.8)
17
0.17
N
Doble 22**
23.8
(10.7)
35
(15.8)
18
0.35
N
Doble 20
23
(10.4)
30.3
(13.7)
21
0.10
N
Doble 28
32.2
(14.6)
46.8
(21.2)
21
0.35
N
Doble 34
34.5
(15.8)
47.9
(21.7)
21
0.20
N
Doble 47
41
(18.5)
54.6
(24.7)
21
0.40
N
NER
Model
Table 1 Reference Unit Performance by Model
Note: The use of a datalogger adds approximately 0.12L/day NER
* Pending on actual configuration
** Center canister required
*** 5% variance in actual weight is typical
Typical PPSC shown. The
shape of the PPSC helps
keep the product upright
during shipment.
Shock absorbing foam in the
PPSC helps prevent damage to
the dewar. Illustration shows top
view of the tank in the PPSC.
The rubber latch design allows
the use of a zip tie, vet seal,
safety seal, etc. to ensure
integrity of product shipped.
ISTA-3A