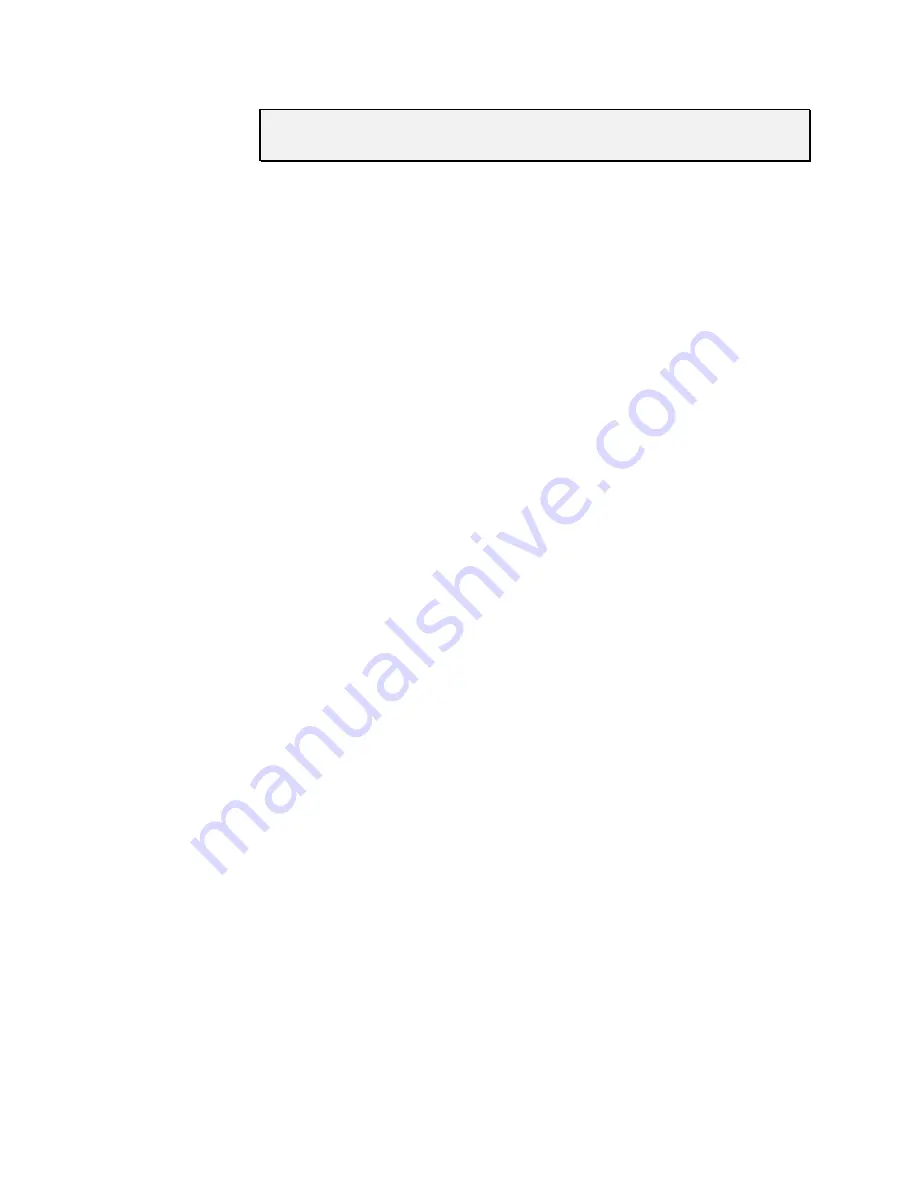
Software Communication
3-29
CAUTION!
Once the [W] command is issued to a pump with a valve mounted, the
valve will not move until the power is cycled to the pump.
z Set Counter Position (3-Port Distribution Valve Only)
The [z] command sets the pump’s position counter to the value contained in the current
encoder position. This command is used after a plunger overload error to resynchronize
the pump’s actual position with its internally recorded position without having to go
through the entire initialization sequence.
Plunger Movement Commands
A <n> A
BSOLUTE
P
OSITION
The [A] command moves the plunger to the absolute position <n>, where <n> = 0..3000.
For example:
[A300] moves the syringe plunger to position 300.
[A600] moves the syringe plunger to position 600.
a
<n> A
BSOLUTE
P
OSITION
(N
OT
B
USY
)
This is the same as the [A] command, except that the status bit within the reply string
indicates that the pump is not busy. This is useful for on-the-fly speed changes.
P <n> R
ELATIVE
P
ICKUP
The [P] command moves the plunger down the number of steps commanded. The new
absolute position is the previous po <n>, where <n> = 0..3000.
For example:
The syringe plunger is at position 0. [P300] moves the plunger down 300 steps.
[P600] moves the plunger down an additional 600 steps to an absolute position of
900. The [P] command will return error 3 (invalid operand) if the final plunger
position would be greater than 3000.
Summary of Contents for XP 3000
Page 21: ...Hardware Setup 2 5 RS 232 CABLING Figure 2 3 RS 232 Multi Pump Cabling nc ...
Page 22: ...Hardware Setup 2 6 RS 485 CABLING Figure 2 4 RS 485 Multi Pump Cabling RS 485 A RS 485 B ...
Page 23: ...Hardware Setup 2 7 CAN CABLING Figure 2 5 CAN Multi Pump Cabling ...
Page 36: ...Hardware Setup 2 20 Figure 2 12 XP 3000 Threaded Mount Holes ...
Page 134: ......