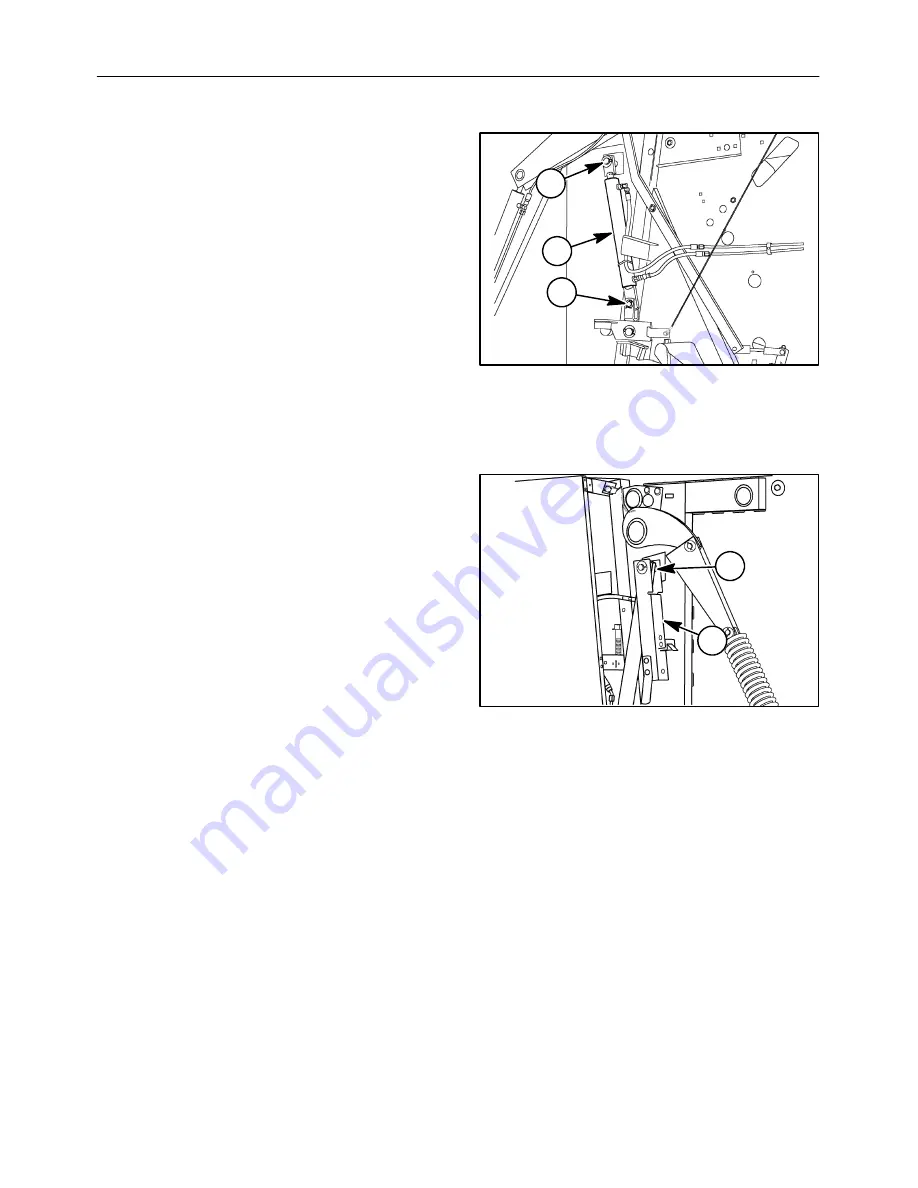
SECTION 35 - HYDRAULIC SYSTEM - CHAPTER 1
35-4
OVERHAUL
LIFT CYLINDER
Removal
1. Close the tailgate and remove all pressure from
the system by stopping the tractor engine. Then
move the tractor remote control lever several
times to both the open and close positions.
2. Clean the areas on and around the cylinder, 1,
near the fittings that attach the lines or hoses to
the cylinder.
3. Disconnect the lines from the fittings on the
cylinder. Loosen the lines slowly to allow the
release of any residual pressure. Plug the hoses
and fittings.
4. Remove the cotter pin closest to the baler from
the lower cylinder mounting pin, 2, in the tailgate
latch. Pull the pin out of the cylinder and latch.
2
3
19993371
1
2
5. Remove the cotter pin and washers from the
upper cylinder mount, 3, and remove the
cylinder. This will also require removal of the
tailgate lockout bracket, 4, and a spacer, 5,
between the rod and lockout.
6. If the cylinder is being replaced, remove the
fittings from the cylinder so they can be installed
on the replacement cylinder.
Installation
1. If the cylinder is being replaced, install either the
fittings removed from the old cylinder or new
fittings.
2. Install the cylinder on the upper mount, 3, and
install washers and a cotter pin to secure the
cylinder.
NOTE:
Be sure to reinstall the tailgate lockout
bracket, 4, with a spacer, 5, on the outside of the rod
when installing the cylinder. There should also be a
41.2 mm (1-5/8
″
) ID washer between the lockout and
the tailgate and a 35 mm (1-3/8
″
) ID washer between
the rod and tailgate pin.
3. Insert the cylinder in the tailgate latch and install
the pivot pin, 2, Figure 3, and secure with a 1/4
″
x 1-1/2
″
cotter pin.
Connect The Lines To The Fittings
Connect the baler to a tractor and open and close the
tailgate several times to purge air from the system.
Check for leaks at the fittings.
5
4
19993368
3
Summary of Contents for RBX443
Page 1: ...5 5RXQG DOHU 5HSDLU 0DQXDO...
Page 12: ......
Page 42: ...SECTION 00 GENERAL INFORMATION CHAPTER 1 00 30...
Page 60: ...SECTION 31 IMPLEMENT DRIVELINE CHAPTER 1 31 18...
Page 82: ...SECTION 31 IMPLEMENT DRIVELINE CHAPTER 2 31 22...
Page 90: ...SECTION 35 HYDRAULIC SYSTEM CHAPTER 1 35 8...
Page 100: ...SECTION 55 ELECTRICAL SYSTEMS CHAPTER 1 55 10...
Page 113: ...SECTION 55 ELECTRICAL SYSTEMS CHAPTER 3 55 9 BALER LIGHTS WIRING DIAGRAM 17...
Page 114: ...SECTION 55 ELECTRICAL SYSTEMS CHAPTER 3 55 10...
Page 124: ...SECTION 62 PRESSING CHAPTER 1 62 2 SECTIONAL VIEWS FLOOR ROLL 1...
Page 128: ...SECTION 62 PRESSING CHAPTER 1 62 6...
Page 130: ...SECTION 62 PRESSING CHAPTER 2 62 2 SECTIONAL VIEWS STARTER ROLL 1...
Page 134: ...SECTION 62 PRESSING CHAPTER 2 62 6...
Page 150: ...SECTION 62 PRESSING CHAPTER 3 62 16...
Page 164: ...SECTION 62 PRESSING CHAPTER 4 62 14...
Page 178: ...SECTION 62 PRESSING CHAPTER 5 62 14...
Page 196: ......