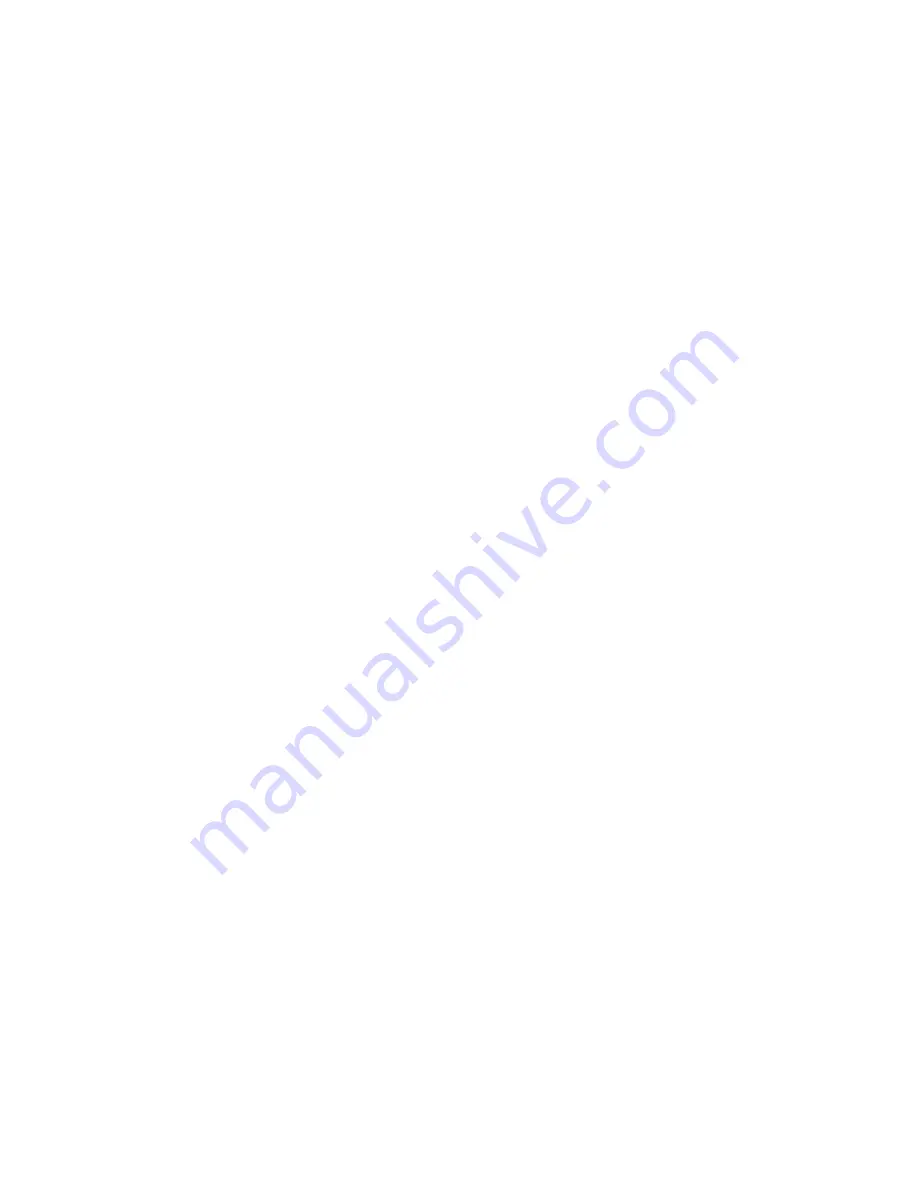
82
Fan Track Learn Enable (FT.CF)
For
BP.CF
= 5, this return/exhaust control configuration se-
lects whether the fan tracking algorithm will make corrections
over time and add a learned offset to
FT.ST
. If this configura-
tion is set to No, the unit will try to control the delta cfm value
between the supply and return VFDs only based on
FT.ST
.
Fan Track Initial DCFM (FT.ST)
For
BP.CF
= 5, this return/exhaust control configuration is the
start point upon which corrections (offset) are made over time
when
FT.CF
= Yes. It is the constant control point for delta
cfm control when
FT.CF
= No.
Fan Track Max Clamp (FT.MX)
For
BP.CF
= 5, this return/exhaust control configuration is the
maximum positive delta cfm control value allowed unless out-
door air cfm control is available and then the delta cfm control
value would be clamped to the outdoor air cfm value directly
(see the Economizer section on page 72 for a description of
outdoor air cfm configuration).
Fan Track Max Correction (FT.AD)
For
BP.CF
= 5, this return/exhaust control configuration is the
maximum correction allowed every time a correction is made
based on
FT.TM
. This configuration is only valid when
FT.CF
=
Yes.
Fan Track Internal EEPROM (FT.OF)
For
BP.CF
= 5, this return/exhaust control internal EEPROM
value is a learned correction that is stored in non-volatile RAM
and adds to the offset when
FT.CF
= Yes. This value is stored
once per day after the first correction. This configuration is
only valid when
FT.CF
= Yes.
Fan Track Internal Ram (FT.RM)
For
BP.CF
= 5, this return/exhaust control internal value is not
a configuration but a run time correction that adds to the offset
throughout the day when
FT.CF
= Yes. This value is only valid
when
FT.CF
= Yes.
Fan Track Reset Internal (FT.RS)
This option is a one time reset of the internal RAM and internal
EEPROM stored offsets. If the system is not set up correctly
and the offsets are incorrect, this learned value can be reset.
Supply Air cfm Config (SCF.C)
For
BP.CF
= 5, this configuration is set at the factory depending
on whether an air foil or forward curve supply air fan is being
used. This information is then used by the control to determine the
correct cfm tables to be used when measuring supply air cfm.
Building Pressure Run Rate (BP.TM)
For
BP.CF
= 2, 3, 4, and 5, this configuration is the PID run
time rate.
Building Pressure Proportional Gain (BP.P)
For
BP.CF
= 2, 3, 4, and 5, this configuration is the PID Pro-
portional Gain.
Building Pressure Integral Gain (BP.I)
For
BP.CF
= 2, 3, 4, and 5, this configuration is the PID Inte-
gral Gain.
Building Pressure Derivative Gain (BP.D)
For
BP.CF
= 2, 3, 4, and 5, this configuration is the PID Deriv-
ative Gain.
BUILDING PRESSURE CONTROL OPERATION
Configuration
BP
BP.CF = 1 (Constant Volume 2-Stage
Control)
Two exhaust fan relays will be turned on and off based on econo-
mizer position to maintain building pressure control. The two trip
set points are
Configuration
BP
BP.P1
and
Configuration
BP
BP.P2
. If the economizer position is greater than or equal to
BP.P1
, then power exhaust relay 1 is energized, turning on the first
stage. A 60-second timer is initialized. If the economizer falls 5%
below the
BP.P1
, then the power exhaust fan relay is turned off. If
the economizer position is less than
BP.P1
and the 60-second tim-
er has expired, the power exhaust fan relay is turned off. The same
logic applies to the second power exhaust fan relay, except the
BP.P2
trip point is monitored. If the economizer position is greater
than or equal to
BP.P2
, then power exhaust relay 2 is energized,
turning on the second stage. A 60-second timer is initialized. If the
economizer is 5% below the
BP.P2
, the second power exhaust fan
relay is turned off. If the economizer is less than
BP.P2
and the 60-
second timer has expired, the power exhaust fan relay is turned
off.
Configuration
BP
BP.CF = 2 (Modulating Power Exhaust)
Control is accomplished with two Belimo MP communicating
actuators in tandem and 2 exhaust fan relays. If building pressure
(
Pressures
AIR.P
BP
) rises above the building pressure set
point (
BP.SP
) and the supply fan is on, building pressure control
is initialized. Thereafter, if the supply fan relay goes off or if the
building pressure drops below the
BP.SP
minus the building
pressure set point offset (
BP.SO
) for 5 continuous minutes,
building pressure control will be stopped. Any time building
pressure control becomes active, the exhaust fan relay turns on,
starting the dual exhaust fan motors. After the exhaust fan relay
turns on, control is performed with a PID loop where:
Error =
BP
–
BP.SP
K = 1000 *
BP.TM
/ 60 (normalize the PID control for run
rate)
P = K *
BP.P
* (error)
I = K *
BP.I
* (error) + “I” calculated last time through the
PID
D = K *
BP.D
* (error – error computed last time through
the PID)
Power exhaust control signal (limited between
BP.MN
and
(
BP.1M
/
BP.2M
) %) = P + I + D
Configuration
BP
BP.CF = 3 (VFD Controlling Exhaust
Fan Motors)
The VFD controlling power exhaust consists of an exhaust fan
VFD (
Outputs
FANS
E.VFD
) enabled by one power ex-
haust relay (
Outputs
FANS
P.E.1
). If building pressure
(
Pressures
AIR.P
BP
) rises above the building pressure set
point (
BP.SP
) and the supply fan is on, then building pressure
control is initialized. Thereafter, if the supply fan relay goes off
or if the building pressure drops below the
BP.SP
minus the
building pressure set point offset (
BP.SO
) for 5 continuous min-
utes, building pressure control will be stopped. The 5-minute
timer will continue to re-initialize while the VFD is commanded
to a position > 0%. If the building pressure falls below the set
point, the VFD will slow down automatically. Any time building
pressure control becomes active, the exhaust fan relay turns on
which energizes the exhaust fan VFD. Control is performed with
a PID loop where:
Error =
BP
–
BP.SP
K = 1000 *
BP.TM
/60 (normalize the PID control for run
rate)
P = K *
BP.P
* (error)
I = K *
BP.I
* (error) + “I” calculated last time through the
PID
D = K *
BP.D
* (error – error computed last time through
the PID)
VFD control signal (clamped between
BP.MN
and
BP.MX
%) = P + I + D
NOTE: Do not change values of PID set point without approval
from Carrier.
BP.CF = 4 (High-Capacity Exhaust Control)
Control is accomplished with a VFD and two exhaust fan relays.
High-capacity power exhaust consists of an exhaust fan VFD
(
Outputs
FANS
E.VFD
) enabled by one power exhaust relay
Summary of Contents for Weathermaster 48P2030-100
Page 130: ...130 Fig 19 Typical Power Schematic Sizes 040 075 Shown ...
Page 131: ...131 Fig 20 Main Base Board Input Output Connections ...
Page 132: ...132 Fig 21 RXB EXB CEM SCB Input Output Connections ...
Page 133: ...133 Fig 22 Typical Gas Heat Unit Control Wiring 48P030 100 Units Shown ...
Page 134: ...134 Fig 23 Typical Electric Heat Wiring 50P030 100 Units Shown ...
Page 135: ...135 Fig 24 Typical Power Wiring 115 V ...
Page 136: ...136 Fig 25 Typical Gas Heat Section Size 030 050 Units Shown ...
Page 138: ...138 Fig 27 Component Arrangement Size 030 035 Units ...
Page 139: ...139 Fig 28 Component Arrangement Size 040 075 Units ...
Page 140: ...140 Fig 29 Component Arrangement Size 090 100 Units ...