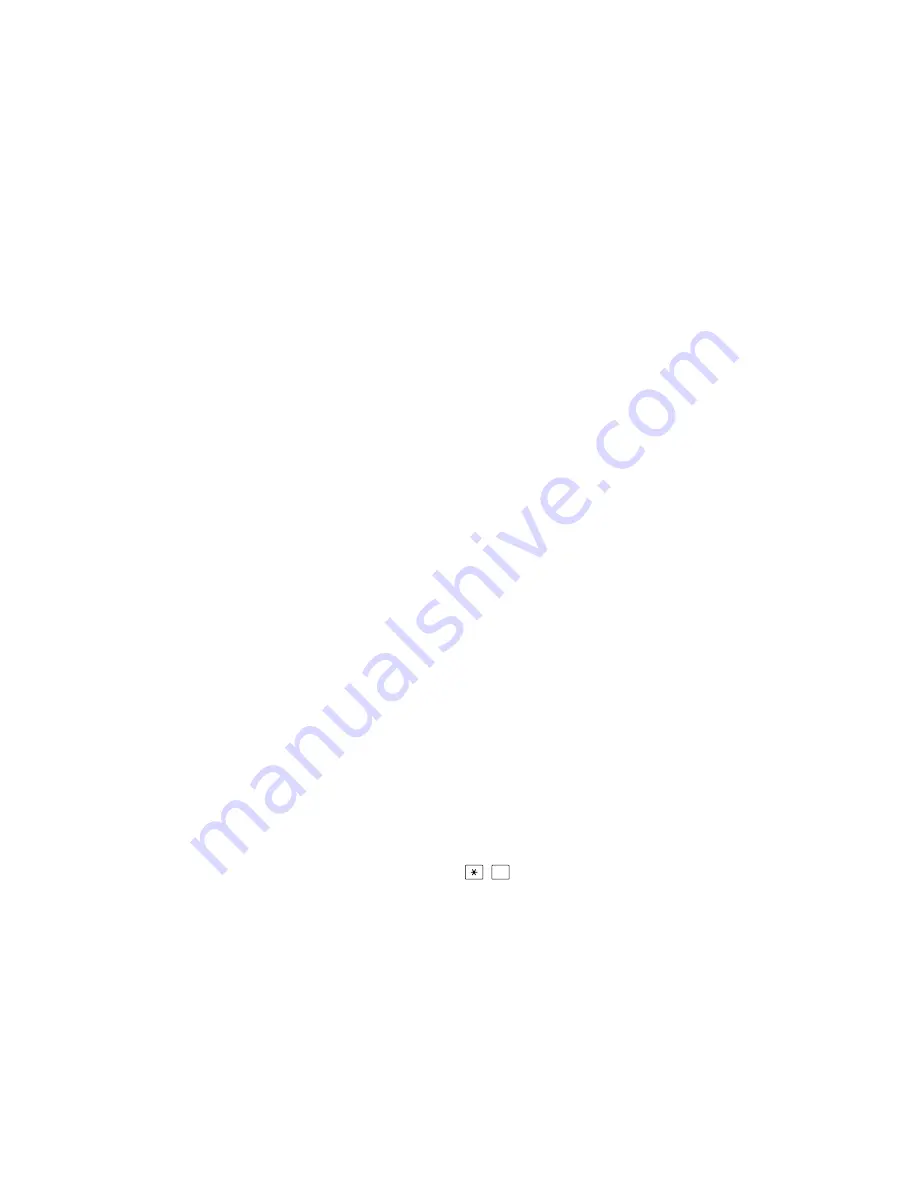
SECTION 7. MEASUREMENT PROGRAMMING EXAMPLES
7-8
It is desired to control the temperature bath at
50
o
C with as little variation as possible. High
resolution is desired so the control algorithm will
be able to respond to minute changes in
temperature. The highest resolution is obtained
when the temperature range results in an output
voltage (V
s
) range which fills the measurement
range selected in Instruction 6. The full bridge
configuration allows the bridge to be balanced
(V
s
= 0V) at or near the control temperature.
Thus, the output voltage can go both positive
and negative as the bath temperature changes,
allowing the full use of the measurement range.
The resistance of the PRT is approximately
119.7 ohms at 50
o
C. The 120 ohm fixed
resistor balances the bridge at approximately
51
o
C. The output voltage is:
V
s
= V
x
[R
s
/(R
s
+R
1
) - R3/(R
2
+R
3
)]
= V
x
[R
s
/(R
s
+5000) - 0.023438]
The temperature range to be covered is 50
±
10
o
C. At 40
o
C R
s
is approximately 115.8
ohms, or:
V
s
= -802.24x10
-6
V
x
even with an excitation voltage (V
x
) equal to
5000mV, V
s
can be measured on the
±
10mV
scale (40
o
C = 115.8
Ω
= -4.01mV, 60
o
C = 123.6
Ω
= 3.428mV). There is a change of
approximately 4mV from the output at 40
o
C to
the output at 51
o
C, or 364
µ
V/
o
C. With a
resolution of 0.33
µ
V on the
±
10mV range, this
means that the temperature resolution is
0.0009
o
C.
The
±
5 ppm per
o
C temperature coefficient of
the fixed resistors was chosen so that their
±
0.01% accuracy tolerance would hold over the
desired temperature range.
The relationship between temperature and PRT
resistance is a slightly nonlinear one. Instruction
16 computes this relationship for a DIN standard
PRT where the nominal temperature coefficient
is 0.00385/
o
C. The change in nonlinearity of a
PRT with the temperature coefficient of
0.00392/
o
C is minute compared with the slope
change. Entering a slope correction factor of
0.00385/0.00392 = 0.98214 as the multiplier in
Instruction 16 results in a calculated
temperature which is well within the accuracy
specifications of the PRT.
PROGRAM
1: Full Bridge (P6)
1:
1
Reps
2:
21
10 mV, 60 Hz Reject, Slow
Range
3:
3
DIFF Channel
4:
1
Excite all reps w/Exchan 1
5:
5000
mV Excitation
6:
1
Loc [ Rs_Ro ]
7:
.001
Mult
8:
.02344 Offset
2: BR Transform Rf[X/(1-X)] (P59)
1:
1
Reps
2:
1
Loc [ Rs_Ro ]
3:
50
Multiplier (Rf)
3: Temperature RTD (P16)
1:
1
Reps
2:
1
R/R0 Loc [ Rs_Ro ]
3:
2
Loc [ TEMP_degC ]
4:
.98214 Mult
5:
0.0
Offset
7.11 PRESSURE TRANSDUCER - 4
WIRE FULL BRIDGE
This example describes a measurement made
with a Druck PDCR 10/D depth measurement
pressure transducer. The pressure transducer
was ordered with passive temperature
compensation for use with positive or negative
excitation and has a range of 5 psi or about 3.5
meters of water. The transducer is used to
measure the depth of water in a stilling well.
Instruction 6, 4 Wire Full Bridge, is used to
measure the pressure transducer. The high
output of the semiconductor strain gauge
necessitates the use of the
±
50mV input range.
The sensor is calibrated by connecting it to the
CR23X and using Instruction 6 with a multiplier
of 1 and an offset of 0, noting the readings
(
6
Mode) with 10 cm of water above the
sensor and with 334.6 cm of water above the
sensor. The output of Instruction 6 is 1000 V
s
/V
x
or millivolts per volt excitation. At 10 cm the
reading is 0.19963mV/V and at 334.6 cm the
reading is 6.6485mV/V. The multiplier to yield
output in cm is:
(334.6 - 10)/(6.6485-.19963) = 50.334 cm/mV/V
Summary of Contents for CR23X
Page 8: ...CR23X TABLE OF CONTENTS vi This is a blank page ...
Page 12: ...CR23X MICROLOGGER OVERVIEW OV 2 1 2 3 A 4 5 6 B 7 8 9 C 0 D FIGURE OV1 1 CR23X Micrologger ...
Page 34: ...CR23X MICROLOGGER OVERVIEW OV 24 This is a blank page ...
Page 50: ...SECTION 1 FUNCTIONAL MODES 1 16 This is a blank page ...
Page 72: ...SECTION 4 EXTERNAL STORAGE PERIPHERALS 4 8 This is a blank page ...
Page 88: ...SECTION 6 9 PIN SERIAL INPUT OUTPUT 6 10 This is a blank page ...
Page 110: ...SECTION 7 MEASUREMENT PROGRAMMING EXAMPLES 7 22 This is a blank page ...
Page 134: ...SECTION 8 PROCESSING AND PROGRAM CONTROL EXAMPLES 8 24 This is a blank page ...
Page 164: ...SECTION 9 INPUT OUTPUT INSTRUCTIONS 9 30 This is a blankpage ...
Page 188: ...SECTION 11 OUTPUT PROCESSING INSTRUCTIONS 11 8 This is a blankp age ...
Page 221: ...SECTION 13 CR23X MEASUREMENTS 13 21 FIGURE 13 5 1 Circuits Used with Instructions 4 9 ...
Page 229: ...14 3 1 2 3 A 4 5 6 B 7 8 9 C 0 D FIGURE 14 3 1 CR23X Battery Pack and Panel ...
Page 240: ...SECTION 14 INSTALLATION AND MAINTENANCE 14 14 This is a blank page ...
Page 244: ...APPENDIX A GLOSSARY A 4 This is a blank page ...
Page 268: ...APPENDIX B CONTROL PORT SERIAL I O INSTRUCTION 15 B 24 This is a blank page ...
Page 276: ...APPENDIX C BINARY TELECOMMUNICATIONS C 8 This is a blank page ...
Page 278: ...This is a blank page ...
Page 282: ...APPENDIX F DYNAGAGE SAP FLOW P67 F 4 This is a blank page ...
Page 299: ...APPENDIX I TD OPERATING SYSTEM ADDENDUM FOR CR510 CR10X AND CR23X MANUALS ...
Page 300: ...This is a blank page ...
Page 302: ...This is a blank page ...
Page 308: ...TABLE DATA ADDENDUM AD 6 This is a blank page ...
Page 324: ...TD ADDENDUM SECTION 1 FUNCTIONAL MODES AD 1 8 This is a blank page ...
Page 340: ...TD ADDENDUM SECTION 8 PROCESSING AND PROGRAM CONTROL EXAMPLES AD 8 10 This is a blank page ...
Page 342: ...This is a blank page ...
Page 373: ...This is a blank page ...