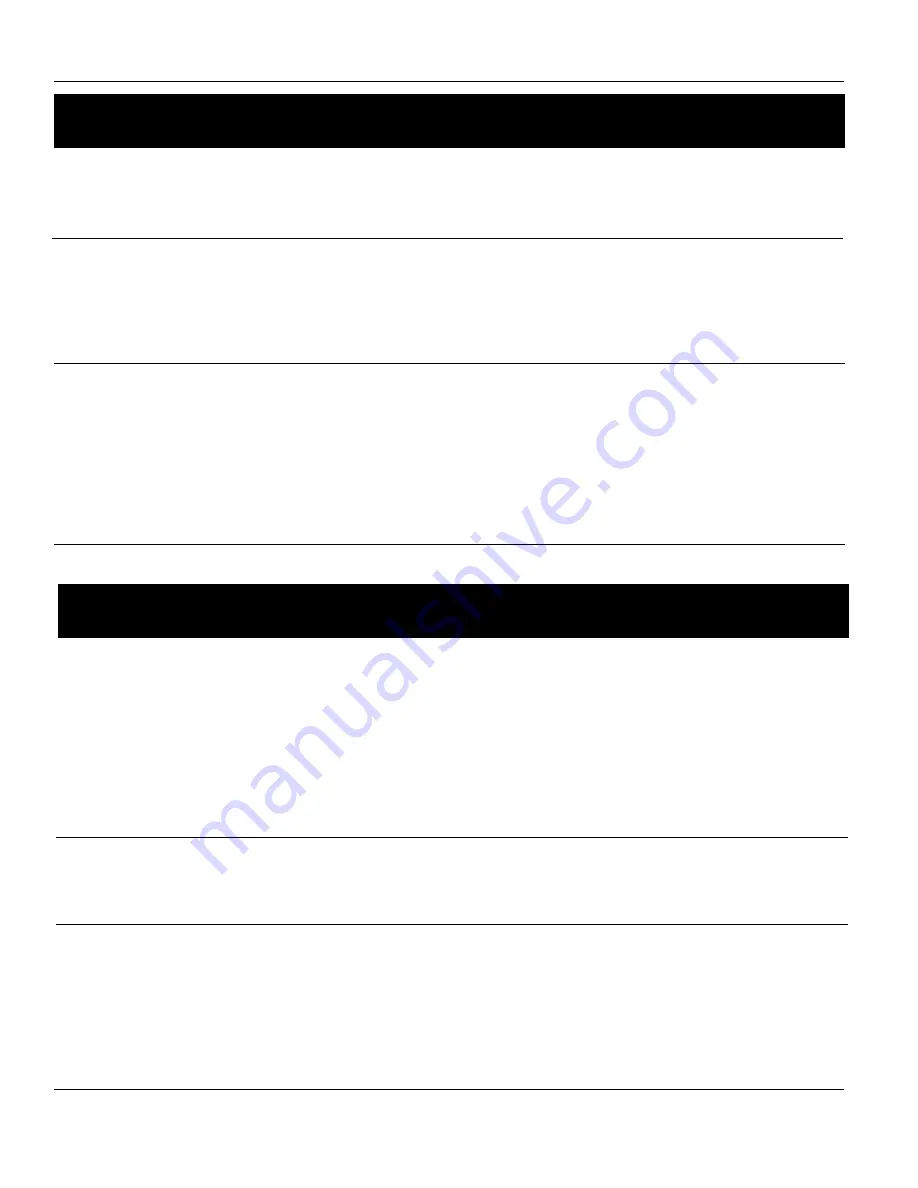
10
Operating Instructions
✽
These diagnostic and repair procedures should be performed by an authorized service center.
Troubleshooting Chart - Generator (Continued)
Symptom
Possible Cause(s)
Corrective Action
Low output voltage
under load
Erratic output voltage
Noisy operation
1. Open diode
2. Engine speed too slow at full load
3. Excessive load applied
4. Voltage setting on front panel incorrect
1. Unbalanced engine
2. Dirty, corroded, or loose wiring
connection
3. Unstable load applied
1. Loose welder/generator or engine bolt
2. Short circuit in welder/generator field or
load
3. Faulty bearing
1. Test diodes, replace if necessary
✽
2. Adjust engine speed
✽
3. Reduce the applied load
4. Adjust setting on front panel
1. Refer to engine manual
2. Referring to the wiring diagram, clean and
reconnect all wiring
✽
3. Remove all loads, then apply each one
individually to determine which one is
causing erratic function
1. Tighten all mountings
2. Test winding resistance, replace field
winding if necessary
✽
Test load devices for shorts. Replace
defective load device.
3. Replace bearing
1. Check work clamp, cable and connection to work
piece. Check electrode cable and clamp
2. Check all welder external connections
3. Set front panel switch to weld
4. Referring to the wiring diagram, clean and
reconnect all wiring
✽
5. Replace capacitor
✽
6. Test winding resistance, replace field winding if
necessary
✽
7. Test diodes, replace if necessary
✽
1.Avoid contact with work piece
2. Make sure clothing and work area are dry
1. Verify that electrode is for alternating current (AC)
2. Use smaller diameter electrode
3. Verify proper grounding. (No paint, varnish or
corrosion)
4. Adjust engine speed
Troubleshooting Chart - Welder
Symptom
Possible Cause(s)
Corrective Action
1. Inadequate current at electrode
2. Poor connections at welder
3. Front panel switch set incorrectly
4. Open, shorted, or incorrect wiring
5. Faulty capacitor
6. Open or shorted field windings
7. Open diodes
1. Accidental contact with work
piece
2. Current leakage caused by moist
clothing or work area
1. Wrong type of electrode.
2. Electrode diameter too large
3. Work piece not properly
grounded
4. Engine speed is too slow
Welder runs but does not
weld
Welder gives trickle
shocks
Arc difficult to strike
✽
These diagnostic and repair procedures should be performed by an authorized service center.
www.chpower.com