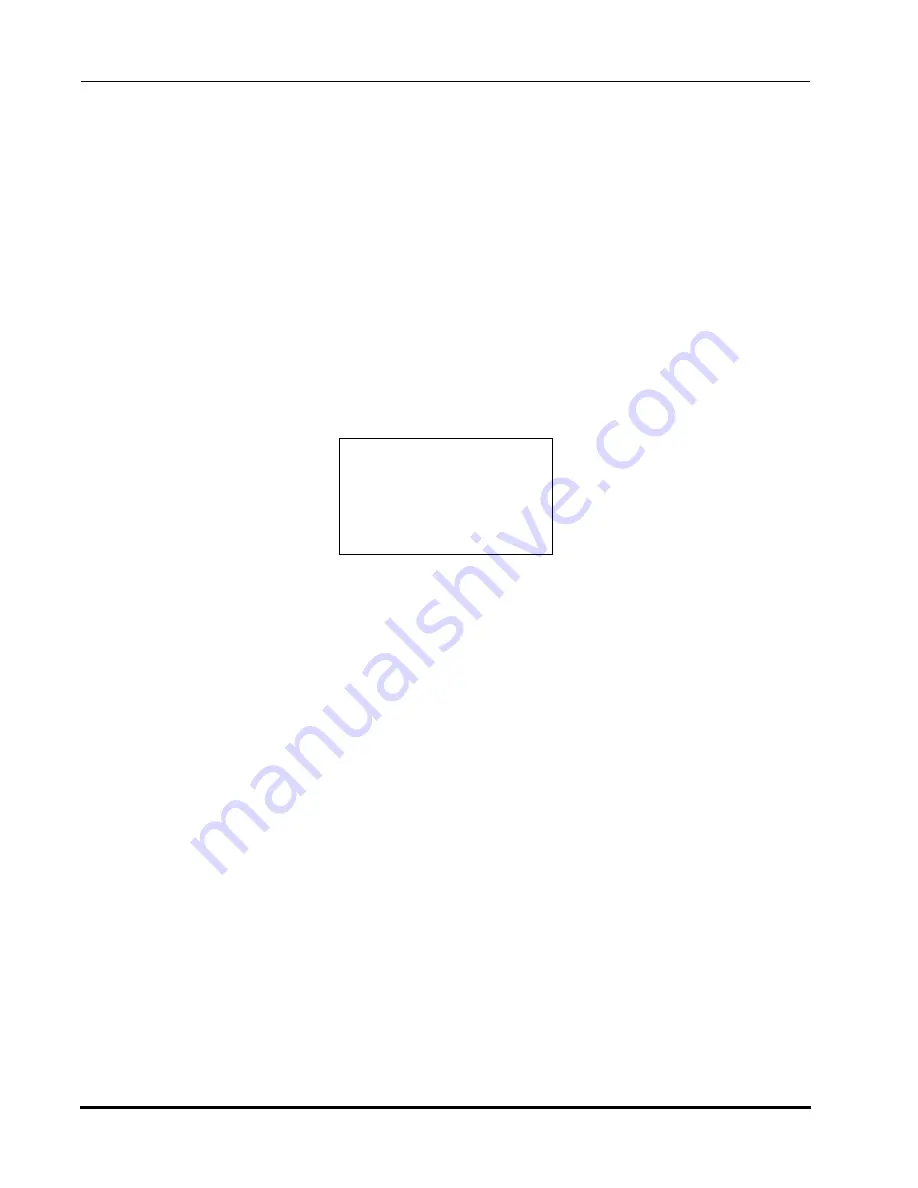
Maintenance
Atmospheric Single-Arm Robot
Using the Teach Pendant to Run Diagnostics
User’s Manual
Brooks Automation
9-36
Revision 1
STEP #5 (AMP. BOARD SETUP)
Do not perform Step 5. Press the >>> key to advance to the next step.
STEP #6 (AMP. MODULE SETUP)
Do not perform Step 6. Press the >>> key to advance to the next step.
STEP #7 (SERVO TEST)
Run the Servo Test only after you pass the Encoder Read Test. Before you move an
axis, make sure the robot signal cable is securely connected.
In the display, XXXX TL is the torque limit being sent to the corresponding motor,
and YYYY is the current torque limit setting.
To test the continuous action of the amplifier modules:
1.
Set the torque limit (TL) to 3333 by pressing the > and < buttons as needed.
2.
Manually move one axis at a time. You should feel the motor apply a
counter-directional force smoothly and continuously without jerking.
Repeat Step 2 for another axis. At higher torque settings, be careful to not apply too
much force because the belts might slip.
STEP #8 (HOME TEST & SET)
Each robot motor is factory set such that the distance between the home switch and
the encoder index is always between 1/3 and 2/3 of a motor revolution away. This is
critical for maintaining repeatability of the home position of each axis at a given
mechanical calibration.
In the following graphic, the robot Z axis is homed. The homing procedure moves an
axis to its home switch and then moves in the opposite direction to find the encoder
index. (The encoder index is up to one encoder revolution mark.)
T: XXXX
R: XXXX TL
Z: XXXX YYYY
Move Axes
Artisan Technology Group - Quality Instrumentation ... Guaranteed | (888) 88-SOURCE | www.artisantg.com