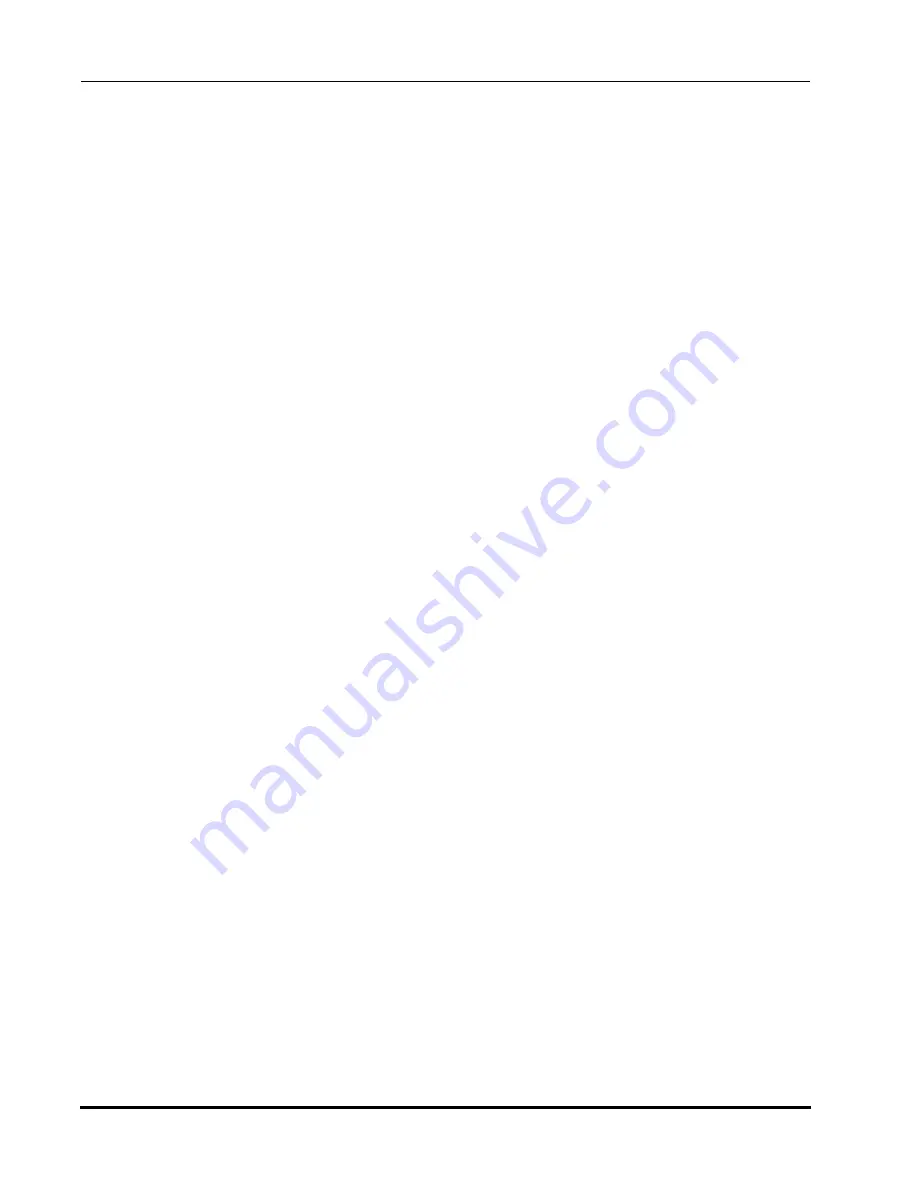
Operational Interfaces
Atmospheric Single-Arm Robot
Interface Overview
User’s Manual
Brooks Automation
5-2
Revision 1
Interface Overview
The robot and controller comprise the basic wafer handling system.Three cables con-
nect the robot and the controller:
•
Two 50-pin, D-sub signal cables. The robot and controller send and receive sig-
nals over the signal cables.
•
One 8-pin, high-power, D-sub power cable that carries the current to the ampli-
fiers. The output power that drives the T, R, and Z-axis motors to the correct
position is sent from the controller to the robot.
The controller has up to three communication ports that can provide various commu-
nication connections:
•
The optional Teach Pendant uses a 6-pin modular connection to an RJ12 jack
for connection to COM1.
•
The host computer 25-pin D-sub can connect to an RS-232 cable for host com-
puter to controller communication. The signal cable is connected to a DB25-pin
male connector RS-232 serial port.
•
An optional third communication port can be used for connection to other
equipment, such as an elevator or indexer.
For more information about communication connections, refer to the
Smart Controller
Hardware and Software User’s Manual
.
The controller has additional external connections:
•
The controller I/O board(s) provides optically isolated external inputs and out-
puts. The input lines read signals from components such as cassette sensors.
The output lines control external devices such as a relay of up to 50 V
DC
at 200
mA.
•
The two power supplies are switching and linear. The switching power supply
provides power to the PC bus and the linear power supply provides power to
the amplifier modules.
Figure 5-1
shows the typical connections for a typical system using the Atmospheric
Single-Arm Robot.
Artisan Technology Group - Quality Instrumentation ... Guaranteed | (888) 88-SOURCE | www.artisantg.com