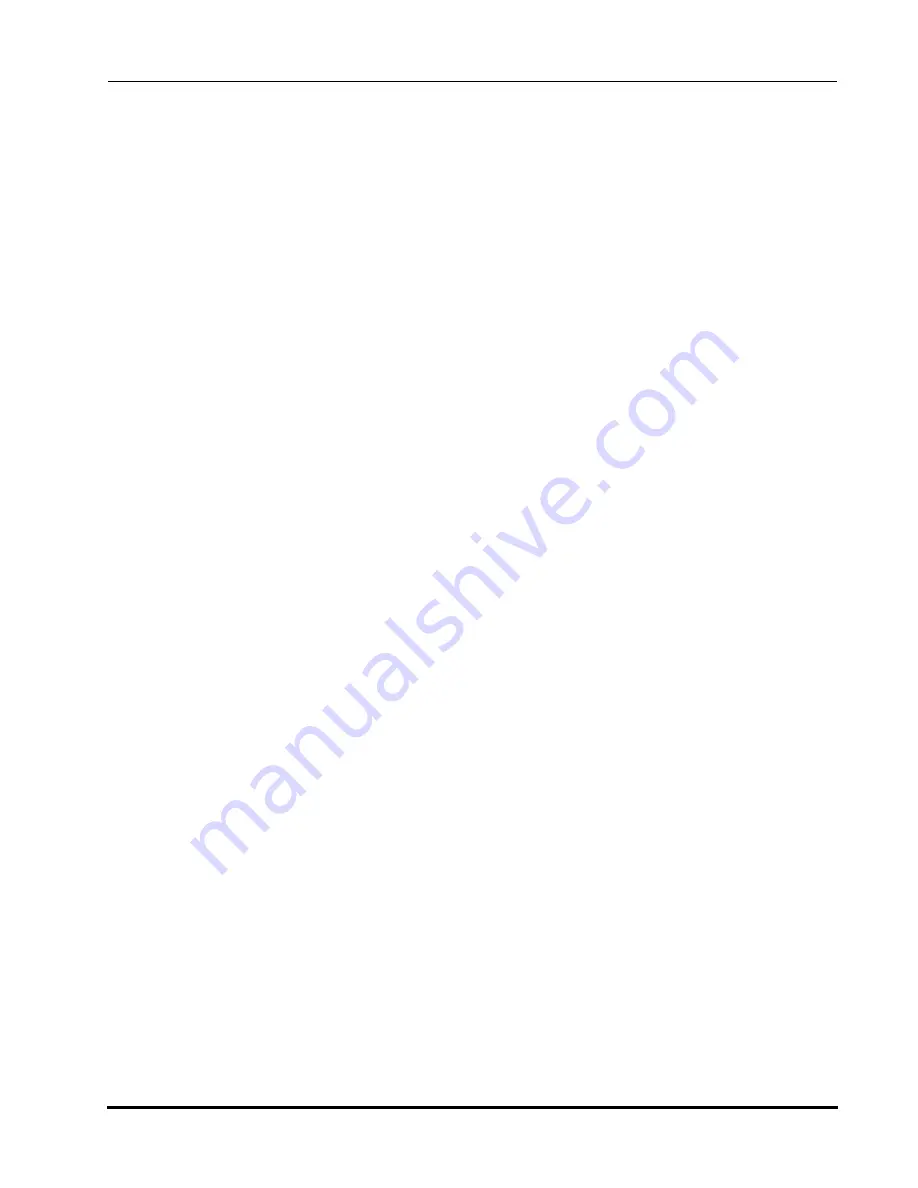
Atmospheric Single-Arm Robot
Maintenance
User’s Manual
Robot Leadscrew Lubrication Procedure
Brooks Automation
Revision 1
9-7
Determining which grease to use on your robot
For Kuroda “C” type grease (P/N 1007-0360)
You need to use Kuroda greas (P/N for ATM100, 1007-0062c). On the lead-
screw you should see:
•
The grease on the leadscrew is white or tan.
•
“Kuroda” is printed on the bottom part of the leadscrew bearing nut.
•
There is a black rubber plug on the purge port.
Procedure for lubricating with Kuroda grease:
1.
Remove the black plug by carefully pushing the plug through with a
small screwdriver.
2.
Insert the tip of the grease syringe into the grease port and push the
grease into the bearing nut until the grease purges out through the
nylon retainer on the bottom of the bearing nut.
3.
Re-insert the black plug into the grease port and clean off the excess
grease.
For LG2 grease (P/N 1007-0359
You need to use LG2 grease on the robot for the ATM100 (1001-0062A),
ATM200 (1001-0127), ATM300 and FPD (1001-0092), ATM400/ABM400 (1001-
0096) or the FPD500 (1001-0093). On the leadscrew you should see:
•
There is no visible markings on the leadscrew bearing nut.
•
The purge port is filled in with solder.
Procedure for lubricating with LG2 grease:
1.
Locate your 6mm 45 degree "zerk" fitting that is to be installed.
Artisan Technology Group - Quality Instrumentation ... Guaranteed | (888) 88-SOURCE | www.artisantg.com