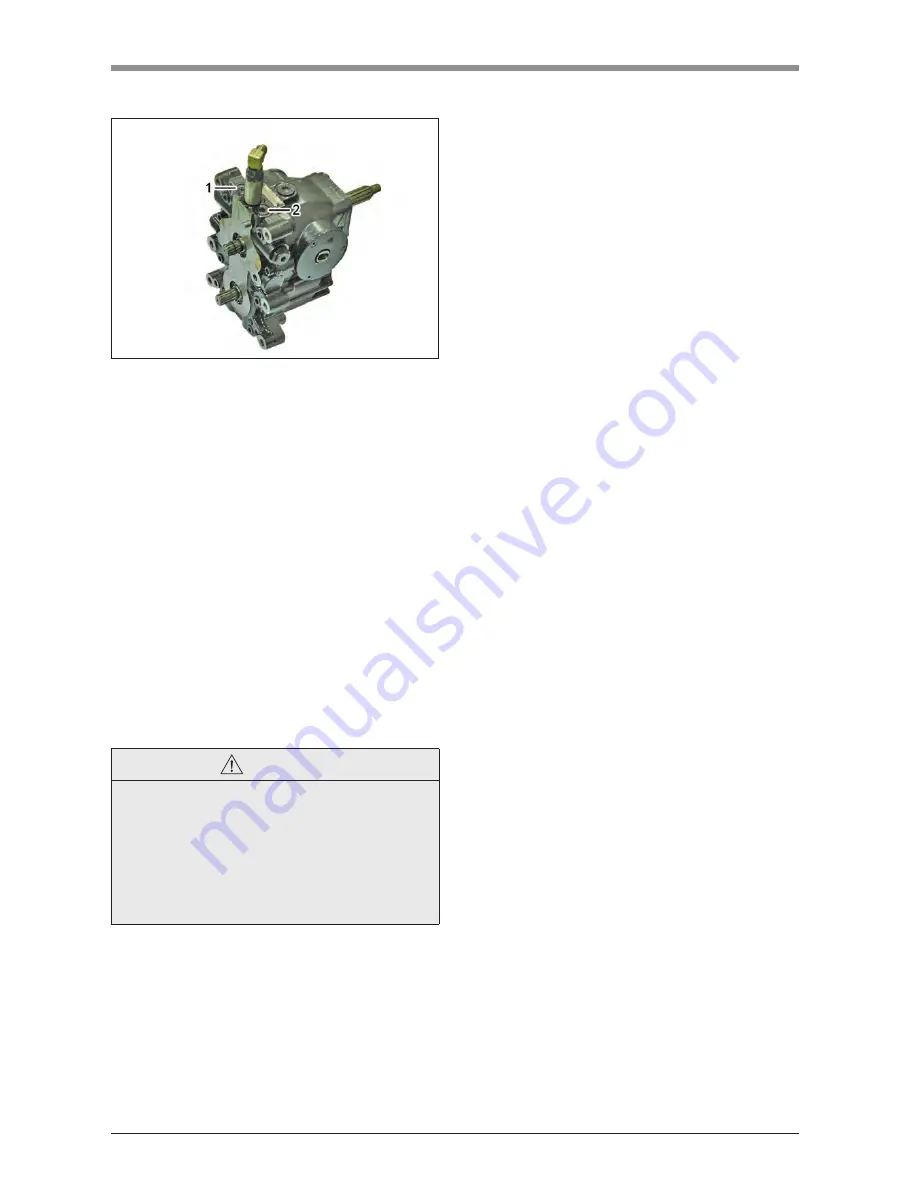
6
-
100
42hw-201601
Chapter 6 hydrauliC system
3015r(h)/3515r(h)/4015r(h)/F36r(h)/F42r(h) traCtOr
8.5 hst maiN relieF valve pressure test
a42W644a
1. Remove the plug (1) from the pressure measuring
port of the HST high pressure relief valve and set
the pressure gauge (500 kgf/cm
2
or higher).
2. Start the engine and place the range shift lever
in the 3rd gear shift position. Then, depress the
brake pedal fully and depress the shuttle shift
pedal repeatedly to increase the oil temperature.
3. Set the engine speed to 2,600 RPM and depressing
the forward pedal fully. Then, measure the pressure
of the high pressure relief valve (for forward driving).
4. If the measurement is out of the standard (380
kgf/cm
2
), check the high-pressure relief valve
and HST body.
5. Perform the same measurement for the reverse
driving side.
(1) Pressure measuring port of high
pressure relief valve (forward driving) (PT 3/8)
(2) Pressure measuring port of high
pressure relief valve (reverse driving) (PT 3/8)
warNiNG
if the tractor moves with the brake pedal de-
pressed, it can cause an accident. stop the test
immediately and resume the test after the service.
Never let anyone other than the driver get near
the front and rear side of the tractor. any ob-
server can be hit by a tractor during the test and
he/she can seriously get injured.
•
•
Summary of Contents for 3015h
Page 6: ......
Page 162: ... BranSOn tractors Co Ltd MEMO ...
Page 172: ... BraNSON tractors Co ltd MEMO ...
Page 278: ... BranSon tractors Co ltd MEMO ...
Page 380: ......
Page 382: ......
Page 384: ......
Page 432: ......
Page 438: ......
Page 447: ...Chapter 8 INDEX ...
Page 454: ... BraNSON tractors Co Ltd MEMO ...