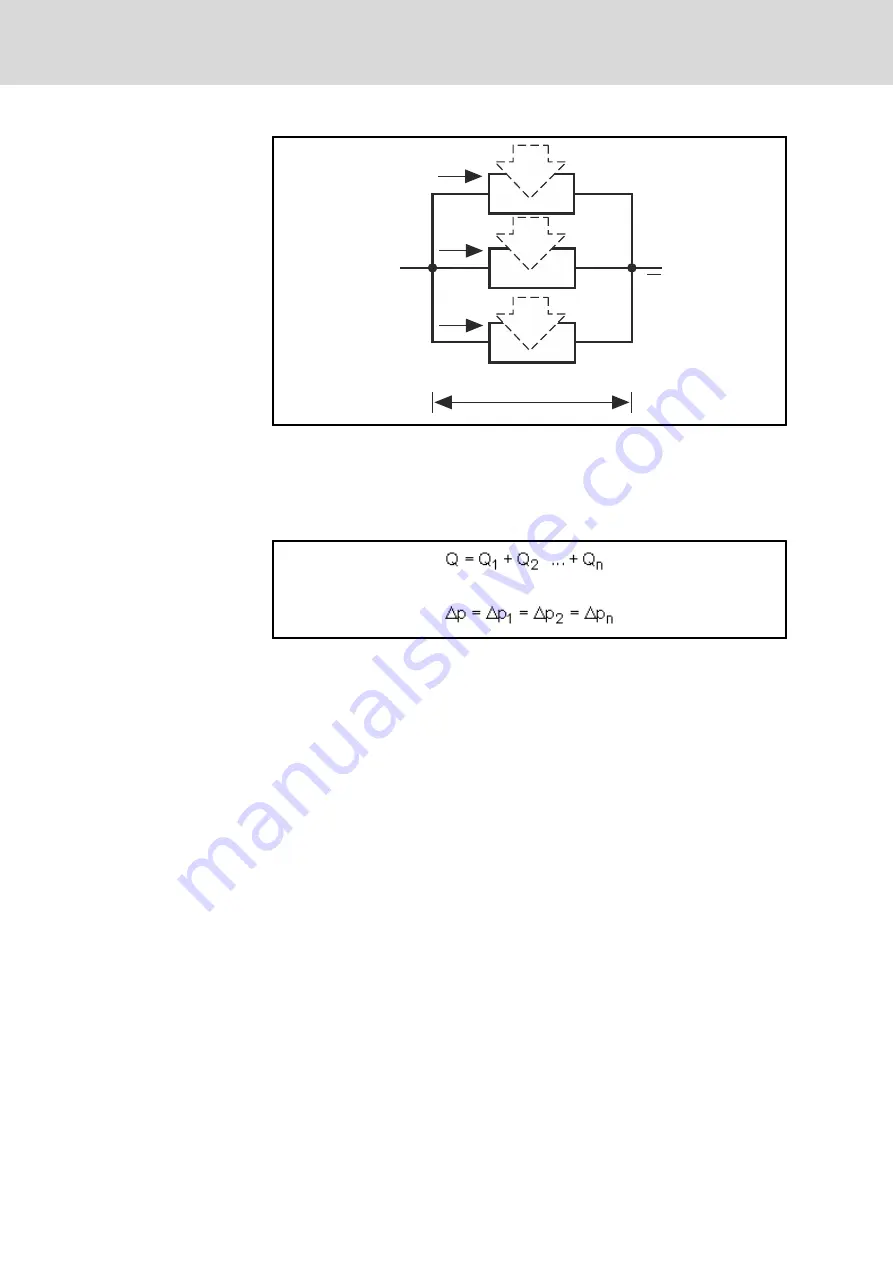
Parallel connection
J
1
Q
1
S
J
1
J
2
Q
2
S
J
J
3
Q
3
D
P
V1
P
V2
P
V3
Fig. 9-11:
Parallel connection of liquid-cooled drive components
The parallel connection is characterized by nodes in the hydraulic system.
The sum of the coolant streams flowing into a node is equal to the sum of the
coolant streams flowing out of this node. Between two nodes, the pressure
difference (pressure drop) is the same for all intermediate cooling system
branches.
Δp
Pressure drop
Q
Flow quantity
Fig. 9-12:
Pressure drop and flow rate in the parallel connection of hydraulic
components
When several working components are cooled, a parallel connection is ad‐
vantageous for the following reasons:
●
The individual components that are to be cooled can be cooled using
the individual required flow rate. This means a high thermal operational
reliability.
●
Same temperature level at the coolant entry of all components (uniform
machine heating)
●
Same pressure difference between coolant entry and outlet of all com‐
ponents (no high overall pressure required)
274/409
Application notes
MBT High Synchronous Torque Motors
Bosch Rexroth AG R911298798_Edition 08
Summary of Contents for rexroth MBT
Page 1: ...MBT High Synchronous Torque Motors Project Planning Manual R911298798 Edition 08 ...
Page 18: ...6 409 MBT High Synchronous Torque Motors Bosch Rexroth AG R911298798_Edition 08 ...
Page 32: ...20 409 MBT High Synchronous Torque Motors Bosch Rexroth AG R911298798_Edition 08 ...
Page 240: ...228 409 MBT High Synchronous Torque Motors Bosch Rexroth AG R911298798_Edition 08 ...
Page 298: ...286 409 MBT High Synchronous Torque Motors Bosch Rexroth AG R911298798_Edition 08 ...
Page 416: ...404 409 MBT High Synchronous Torque Motors Bosch Rexroth AG R911298798_Edition 08 ...
Page 421: ...Notes MBT High Synchronous Torque Motors 409 409 ...