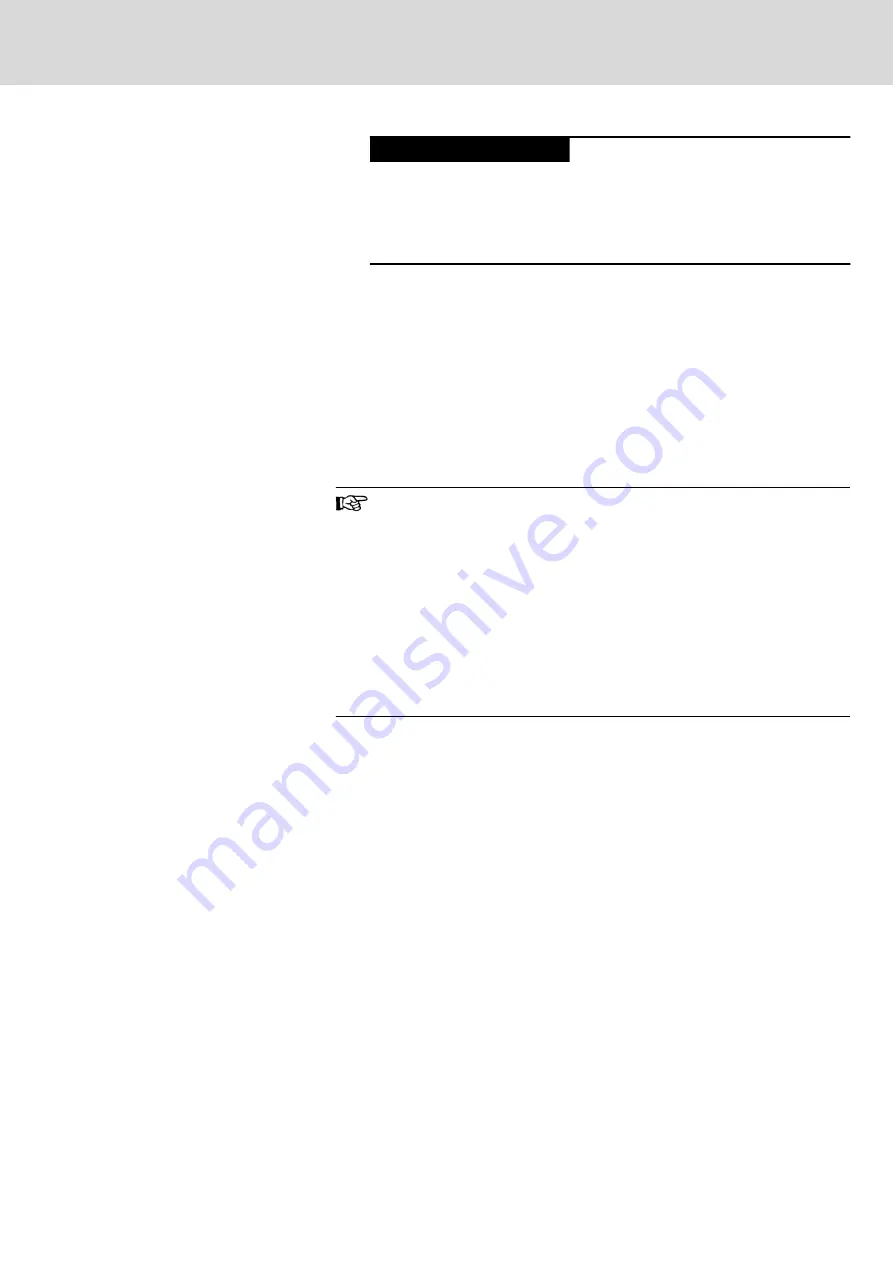
If seals are inserted incorrectly or not at
all, the degree of protection of the motor
will be lost!
NOTICE
Before attaching the terminal box cover to the terminal box, check the
glued-in seal at the terminal box cover to verify that it is in a proper state
and at the correct position.
8.4
Sensors
8.4.1
Temperature sensors
By default, MST stators are equipped with an integrated SNM.150.DK tem‐
perature sensors for motor protection. All stators are fitted with an additional
temperature sensor KTY84-130 for external temperature measurement.
To ensure safe motor protection against thermal overload, the temperature
sensor SNM.150.DK has to be connected to the drive controller. Comply with
the respective connection diagram for the selected connection type (device
connector or terminal box) when connecting the temperature sensors.
●
To ensure safe motor protection against thermal overload,
temperature sensor SNM.150.DK has to be connected to the
drive controller.
●
Ensure correct polarity when connecting the temperature
sensor KTY84-130 for external temperature measurement
(see
fig. 8-3 "Wire identification at MST stators with connec‐
●
KTY84-130 is an ESD sensitive device! For this reason, the
stranded wires of the sensor are protected by a protective
foil at the connection cable. Before connecting the sensor,
take appropriate measures for ESD protection ( ESD = elec‐
trostatic discharge).
Also note the information on motor temperature monitoring in
8.4.2
Encoder
Encoder and encoder connection components are not included in the scope
of delivery of the motor. Select the components according to the machine re‐
quirements.
Setting the encoder polarity depends on the direction of rotation of the rotor
and have to be parameterized upon controller startup. Refer to the instruc‐
tions in the functional description of the controller and the definitions in
ter 13.6 "Determining the polarity of the encoder system" on page 389
.
For information on encoder manufacturers, please refer to
Please note:
The connection cable for connecting the motor encoder and the controller to
an encoder-compatible plug. When using components of different manufac‐
turers, ensure continuous compatibility of the connection technique.
MBT High Synchronous Torque Motors
257/409
Connection technique
R911298798_Edition 08 Bosch Rexroth AG
Summary of Contents for rexroth MBT
Page 1: ...MBT High Synchronous Torque Motors Project Planning Manual R911298798 Edition 08 ...
Page 18: ...6 409 MBT High Synchronous Torque Motors Bosch Rexroth AG R911298798_Edition 08 ...
Page 32: ...20 409 MBT High Synchronous Torque Motors Bosch Rexroth AG R911298798_Edition 08 ...
Page 240: ...228 409 MBT High Synchronous Torque Motors Bosch Rexroth AG R911298798_Edition 08 ...
Page 298: ...286 409 MBT High Synchronous Torque Motors Bosch Rexroth AG R911298798_Edition 08 ...
Page 416: ...404 409 MBT High Synchronous Torque Motors Bosch Rexroth AG R911298798_Edition 08 ...
Page 421: ...Notes MBT High Synchronous Torque Motors 409 409 ...