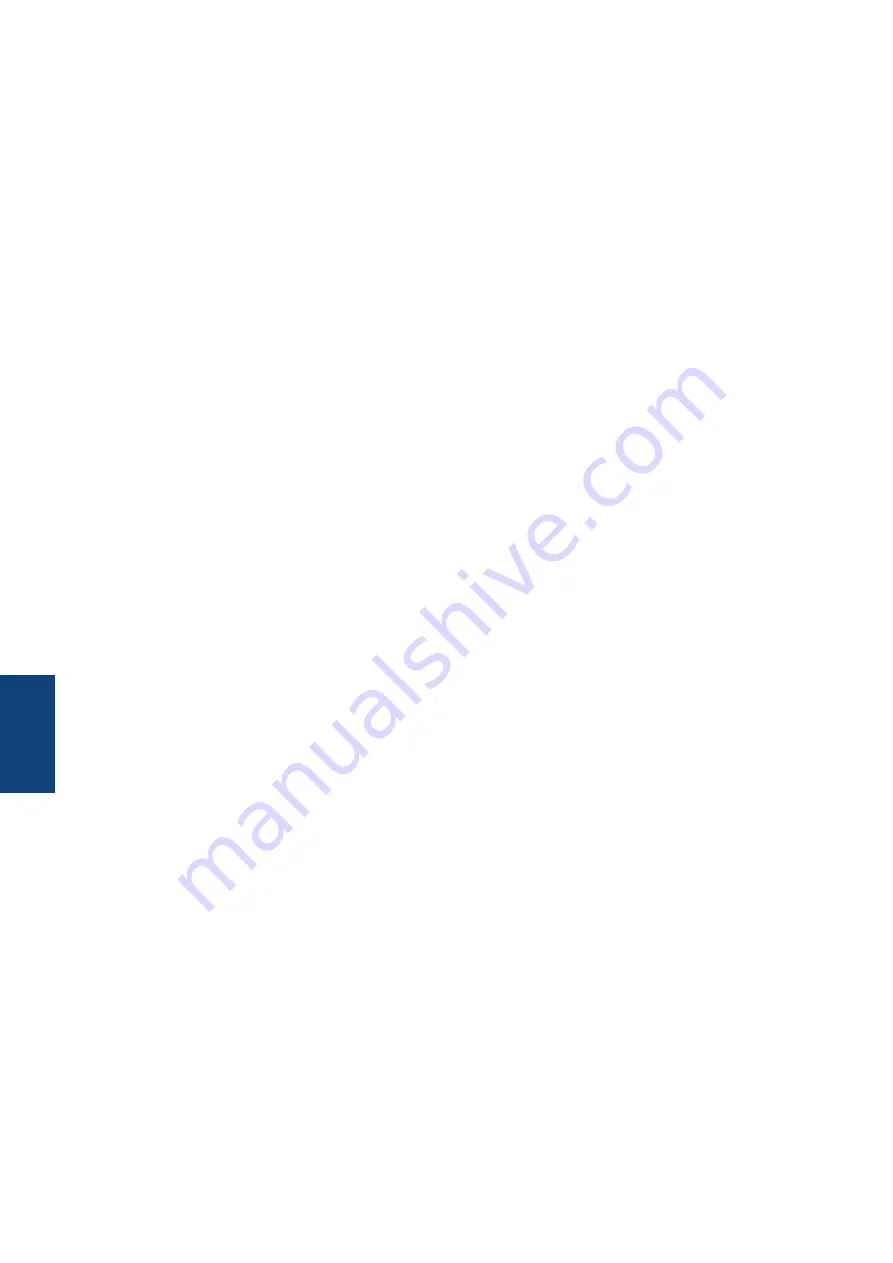
58
MAI
N
TE
N
AN
C
E
&
IN
SP
EC
TI
O
N
Frequency
Inspection
A thorough inspection should be carried out periodically (every 3 months) or as special
circumstances may require. Before starting an inspection disconnect hydraulic system and
remove all foreign materials (dirt, paint, grease, oil, scale, etc) from surface by a suitable
method. After a field inspection, it is advisable to record the extent of testing and testing
results. The periodic or critical load inspection may be conducted in the field. If cracks,
excessive wear etc are recognized, contact Blohm + Voss Oil Tools, LLC or an authorized
service company.
Hydraulic System Inspection
Check for leakage every day. If an internal or external leakage reaches an unacceptable
level, contact Blohm + Voss Oil Tools, LLC or an authorized service company.
Dismantling Inspection
Generally, when the equipment returns to base, warehouse, etc carry out the tool inspec-
tion, immediately. Furthermore, repair it if necessary prior to it being sent on the next
job. The tool should be dismantled and inspected in a suitably equipped facility for exces-
sive wear, cracks, flaws or deformations. Corrections should be made in accordance with
recommendations which can be obtained from Blohm + Voss Oil Tools, LLC.
Summary of Contents for FloorHand 9GF-1102
Page 6: ...6 DESCRIPTION DESCRIPTION...
Page 10: ...10 DESCRIPTION Figure 2 1 352 mm 53 2 in 1 488 mm 58 6 in 1 174 mm 46 2 in 2 581 mm 101 6 in...
Page 11: ...11 DESCRIPTION...
Page 12: ...12 COMMISSIONING COMMISSIONING...
Page 17: ...17 INSTALLATION INSTALLATION...
Page 24: ...24 OPERATIONS 24 OPERATIONS OPERATIONS...
Page 49: ...49 MAINTENANCE INSPECTION MAINTENANCE INSPECTION...
Page 52: ...52 MAINTENANCE INSPECTION Figure 50...
Page 57: ...57 MAINTENANCE INSPECTION Figure 54...
Page 63: ...63 SPARE PARTS SPARE PARTS...
Page 65: ...DRAWINGS 65 DRAWINGS...
Page 66: ...DRAWINGS 66 Figure 55 CANTILEVER STYLE FLOORHAND WITH 9FM 2050 HYDRAULIC CYLINDER...
Page 71: ...DRAWINGS 71 FLOORHAND COMBINATION MANIFOLD 9FH 01539 Figure 60...
Page 72: ...DRAWINGS 72 FLOORHAND RETURN MANIFOLD 9FH 01540 Figure 61...
Page 92: ...INDEX 92 INDEX...
Page 104: ...INDEX 104 W WINCH 87 WINCH ASSY HOSE FITTING KIT 87 WINCH MOUNTING PLATE 87 X Y Z...