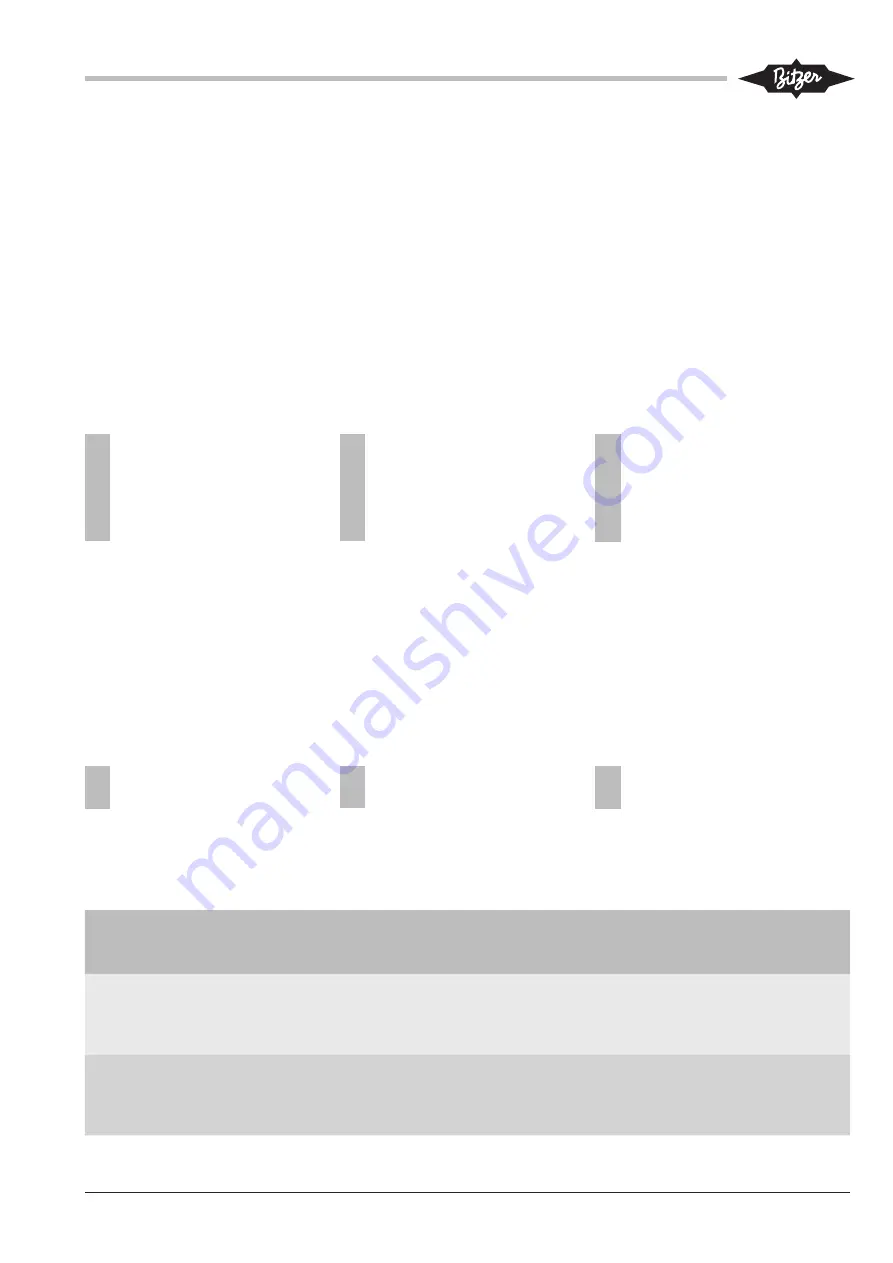
23
SB-110-2 RUS
Ölkontrolle
Unmittelbar nach Inbetriebnahme
folgende Kontrollen durchführen:
• Maximaler und empfehlenswerter
Ölstand während Betrieb innerhalb
Schauglasbereich des Ölabschei-
ders (minimaler Ölstand wird durch
Ölniveauwächter abgesichert).
• In der Anlaufphase kann sich Öl-
schaum bilden, der sich aber nach
2 bis 3 Minuten abschwächen
sollte. Sonst besteht der Verdacht
auf hohen Flüssigkeitsanteil im
Sauggas.
!
!
Achtung!
Gefahr von Nassbetrieb!
Druckgas-Temperatur min-
destens 20 K (R134a, R404A,
R507A, R407C) oder mindestens
30 K (R22) über Verfl üssigungs-
temperatur halten.
Wenn in der Anlaufphase das Öl-
Überwachungssystem (F7) oder nach
Ablauf der Verzögerungszeit (120 s)
der Ölniveauwächter anspricht, deutet
dies auf akuten Schmierungsman-
gel hin. Mögliche Ursachen sind zu
geringe Druckdifferenz oder zu hoher
Kältemittelanteil im Öl. Sauggasüber-
hitzung kontrollieren.
Wenn größere Ölmengen nachgefüllt
werden müssen:
!
!
Achtung!
Gefahr von Flüssigkeitsschlägen!
Ölrückführung überprüfen.
Ölkühler-Temperaturregelung
einstellen
Oil check
Immediately after commissioning do
the following checks:
• Maximum and recommended
oil level during operation within
the sight glass range of the oil
separator (minimum oil level is
monitored by an oil level switch).
• Oil foam can be generated during
the starting phase, but should
reduce after 2 to 3 minutes. If it
does not reduce this can indicate
excessive liquid in the suction gas.
!
!
Attention!
Danger of wet operation!
Keep the discharge temperature
at least 20 K (R134a, R404A,
R507A, R407C) or at least
30 K (R22) above condensing
temperature.
If the oil monioring system (F7) cuts
out during the starting phase or the
oil level switch after the delay time
(120 s) this indicates a severe lack of
lubrication. Possible reasons are too
small pressure difference or excessive
refrigerant in the oil. Check suction
gas superheat.
If larger quantities of oil must be
added:
!
!
Attention!
Danger of liquid slugging!
Check the oil return.
Setting the oil cooler temperature
control
Контроль масла
Сразу после пуска в эксплуатацию
выполните следующие проверки:
• Максимальный и рекомендуемый
уровень масла во время работы
компрессора в пределах смотро-
вогостекла в маслоотделителе
(минимальный уровень масла
контролируется реле уровня масла).
• Масляная пена может образовываться
во время пуска, но она должна
уменьшиться через 2 – 3 минуты. Если
она не уменьшается, то это может
указывать на избыточное содержание
жидкого хладагента во всасываемом
газе.
!
!
Внимание!
Опасность влажного хода!
Температура нагнетания должна
быть как минимум на 20 K (R134a,
R404A, R507A, R407C) или на
30 K (R22) выше температуры
конденсации.
Если система контроля масла (F7)
срабатывает во время пуска компрессора
или если срабатывает реле уровня
масла после периода временной
задержки (120 сек.), то это указывает
на значительную нехватку смазки.
Возможными причинами могут быть
слишком малый перепад давления или
избыток хладагента в масле. Проверьте
перегрев всасываемого газа.
Если необходима дозаправка масла:
!
!
Внимание!
Опасность гидравлического удара!
Проверьте возврат масла.
Настройка регулятора температуры
маслоохладителя
R134a, R404A, R507A, R407C, R22
Fühlerposition
Sensor position
Расположение датчика
Einstelltemperatur
Temperature setting
Настройка температуры
nominal
nominal
номинальная
maximal
maximum
макс.
Bypass-Misch-Ventil oder Wasserregler
By-pass mixing valve or water regulator
Перепускной смесительный клапан или
водорегулятор
Druckgasleitung
Discharge gas line
Линия нагнетаемого газа
20 K > t
c
max.
70°C (85°C*)
Temperatur-Regler des Ölkühler-Lüfters
(luftgekühlt)
Temp. regulator of air-cooled oil cooler fan
Регулятор температуры вентилятора
воздушного маслоохладителя
Druckgasleitung
Discharge gas line
Линия нагнетаемого газа
30 K > t
c
max.
80°C (95°C*)
* R134a t
c
: > 55°C