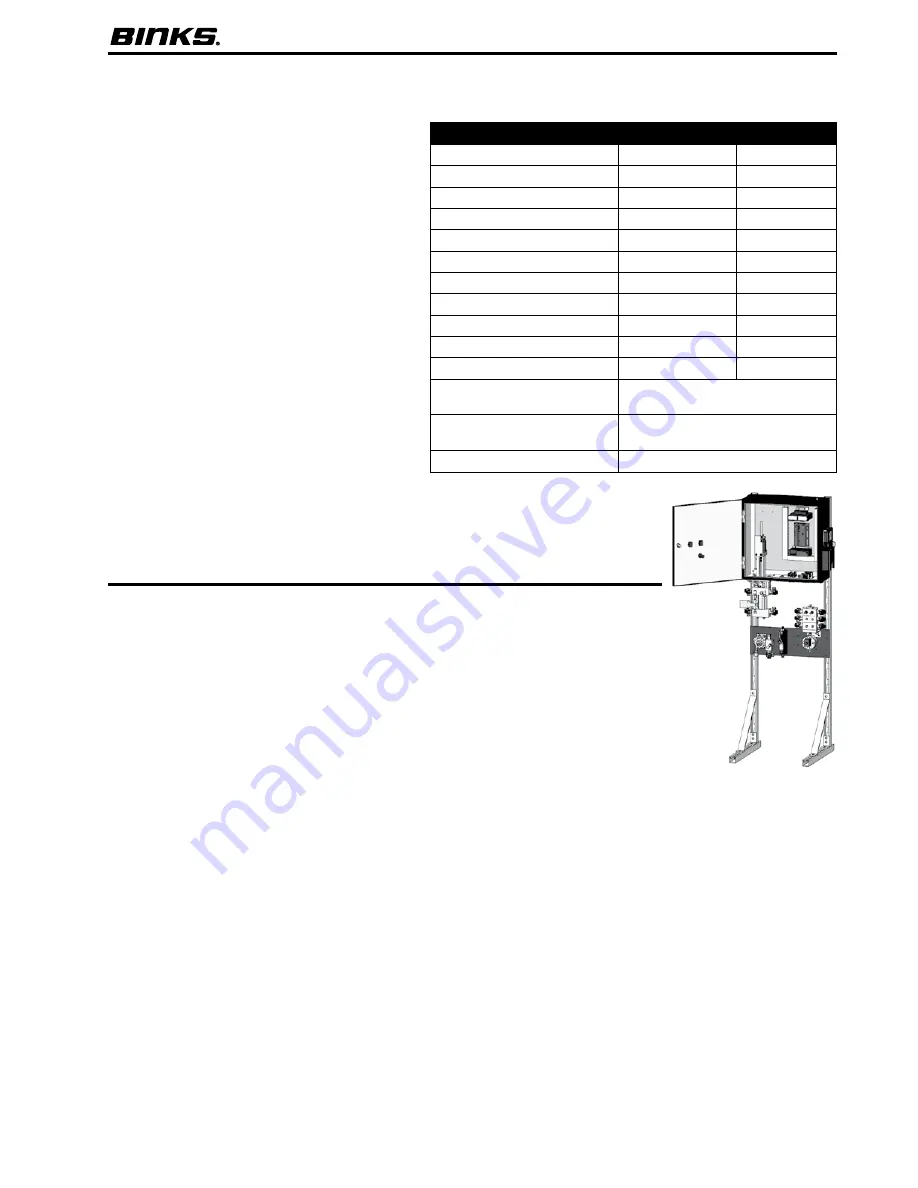
5
BINKS EMS | OPERATION MANUAL
2.1
Technical Specifications
ELECTRONIC MIX SOLUTIONS
The Binks EMS system is designed to accurately
mix most two component paints. It will supply any
low- pressure manual or automatic spray gun and
can easily handle very low flow rates or high ratio
materials (greater than 20:1). The system uses real
time metering to accurately dispense and mix the
resin and hardener on-ratio regardless of varying flow
rate as seen in real world paint applications such as
feathering or rapid triggering with manual guns.
Binks EMS units are configurable with many
popular options such as use with up to 6 colors,
programmable flushing, a Dispense Pump flow
sensor, in-booth fluid panel capability, and gun flush
boxes. The system can provide accurate resin and
hardener dispensing from 1:1 to 100:1 ratios. The
high flow capability mated with the control hardware
and software allows use with two spray guns
simultaneously.
The system is easily set up and operated with front
panel switches and a 24-key control pendant with a 3.8 inch
monochrome screen. Manipulation of system parameters is
restricted via password protection.
TECHNICAL SPECIFICATIONS
Max Working Air Pressure
130 psi
9 bar
Optimal Working Air Pressure
75–100 psi
5.2–6.9 bar
Max Inlet Fluid Pressure
250 psi
17.2 bar
Max Dispense Pump Flow Rate
6.8 or 13.6 oz/min
200 or 400 cc/m
Min Dispense Pump Flow Rate
0.7 or 1 oz/min
2 or 30 cc/min
“A” Side Flowmeter Range
2.4–67.6 oz/min
70–2000 cc/min
Operating Temperature Range
41–122 Fahrenheit
5–50 Celsius
Weight of the Unit
100–150 lbs.
45–68 Kg
Viscosity Range of Fluid
20–3000 cPs
Mixing Ratio Range
1:1–100:1
Ratio Tolerance Range
Up to +/- 1%
Wetted Parts
300 series stainless steel, PTFE,
perfluoroelastomer, FEP
External Power Requirements
95-132 VAC, 50–60Hz. 8 Amp,
14 AWG power supply wire gauge
Environmental
Indoor use, pollution degree (2)
THE BINKS EMS HAS UNIQUE FEATURES
THAT YIELD SUPERIOR MIXING PERFORMANCE:
Continuous Flow
—The mix manifold is designed to
optimize mix quality and minimize internal volume by
receiving Resin (Component A) and Hardener (Component
B) continuously—not in alternating “doses”.
Accurate Dispensing
—Control and positioning of the
metering Dispense Pump is precise. An electronically
controlled stepper motor with internal worm gear and shaft
allow for adjustable dispense speeds while maintaining
accuracy.
Ease of Use
—The control Pendant is simple to learn, and
efficient to use. It allows easy control of the unit, along with
real time data feedback and in-depth troubleshooting when
alarms occur.
Versatile Configurations
— The machine has the ability
to accept up to six different resins, and can be configured
with manual or programmable flushing. It also allows the use
of up to two Gun Flush Boxes.
Intrinsically Safe Option
— An intrinsically safe option
enables the fluid panel to be mounted in a spray booth. This
minimizes the waste produced by color changes.
Programmable Flushing
—
Set unique flushing options
specific to material needs.
Mounting Options
—
The control enclosure can be mounted to a pedestal floor
stand for mobility, or it can be ordered with a wall mount to
be plumbed into an existing workspace.
Low Flow Capability
—The design of the Dispense
Pump allows for low hardener flow rates. Very high mix
ratios at low flow rates can be achieved. The standard 200cc
Dispense Pump can accurately dispense hardener as low as
2cc per minute.
Alarm Warnings
—The built in alarm system warns the
user of system errors and suggests possible solutions. Help
screens provide troubleshooting information to remedy
system alarms.
Modular Design
—All fluid panel sub-assemblies are easily
and quickly removed for maintenance and repair.
2.2 Features
System shown:
E20-141102