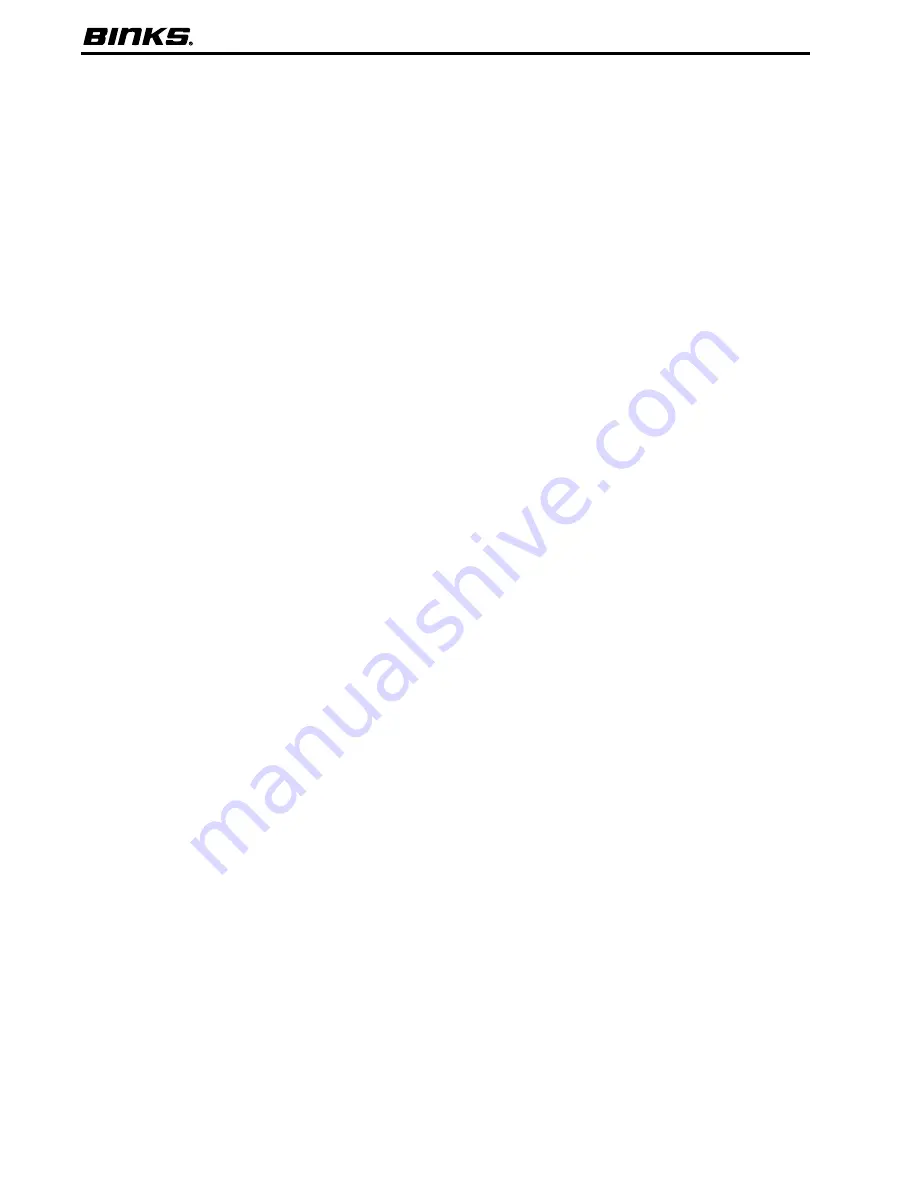
46
BINKS EMS | OPERATION MANUAL
11.1 Glossary of Terms
ACME Lubricant
—Lubricant used on the ACME screw
threads on the stepper motor rod. The lubricant reduces
friction and prevents damage to the threads. Follow callouts
where labeled.
Active Ratio
—The current resin-to-hardener ratio the
system has loaded and ready to spray. Visible on the Home
screen of the pendant.
Air Cut Off Valve
—A pneumatically (pilot) operated
valve that stops the flow of atomizing air to the spray gun
during a flush or color change. Only used with gun flush
boxes.
Air Flow Switch
—A device used to send a pneumatic
signal to the EMS control when the spray gun atomizing air
is triggered. The switch is located on the EMS fluid back
panel. Optionally, it may be located in the spray booth.
Alarm
—The red light and buzzer on the front of the EMS
Enclosure. Alarms sound when certain monitored values fall
out of the operating range, such as the pot life or mixture
ratio. Also referred to as a fault.
Atomizing Air
—The air supplied to the spray gun that
is used to atomize the mixed material. This air is routed
through the Air Flow Switch(es), where recommended
supply pressure is between 20 and 75 psi.
Air Flush Valve
—The ball valve on a single color unit
with the manual flush option. It controls the air used to flush
the fluid lines. When open, it allows air to travel into the fluid
lines. Located on the bottom of the Mix Manifold.
Ball Valve
—A hand operated valve that opens or closes a
passageway with the turn of a knob or handle.
Blow Back
—The term used to describe the backward flow
of material through the system. In the Binks EMS system this
condition is prevented by the use of check valves to limit the
direction that fluid pressure can take. Always ensure proper
function of the check valves to prevent Blow Back and the
corresponding damage that could occur to the Dispense
Pump or other components. Also known as “crossover”.
Blow Off Time
—The amount of time allotted for the
triggering of atomizing air with no fluid supply. This is a
parameter set in the EMS system to allow a painter to use the
gun atomizing air for a short time to clean a part immediately
prior to spraying.
Calibration
—The process of setting a device to measure
accurately. The Flow Meter is the only Binks EMS
components that requires calibration. See
9.3 Flow Meter
Calibration Procedure
to verify the proper performance of
the flow meter.
Catalyst
—A coating component that initiates a chemical
reaction in the coating to accelerate the hardening process.
Catalysts are typically identified by high mix ratios such
as 10:1 or 50:1. Sometimes the catalyst-to-resin ratio is
expressed as a percentage such as 10% or 2%.
Check Valve
—Valves used to limit the flow of fluid
or air to one direction. The valve is typically held in
the closed position by a spring. Check valves should be
cleaned or replaced frequently as they are more likely than
other components to become clogged with hardened paint
particles.
Chop
—The term used to describe short bursts of air or
solvent in the fluid lines, typically in sequence at varying
specified intervals. Lengths of time set in the Setup screens
of the Pendant.
Circulation System
—A circulation system is fluid
plumbing with the ability to circulate paint material in a
continuous loop so particles remain in suspension. These
systems can be used with the Binks EMS unit and routed
through the Color Stack.
Color Stack
—The component of the Binks EMS that
augments the unit to accept up to 6 colors, allow plumbing
for circulation systems, controls flush procedures, and
mounts the flow meter for active metering. The component
will accommodate 2-6 resin colors.
Component A
—The term used to describe the resin
material that is sent through the color stack and flow meter.
Component B
—The term used to describe the hardener
material or catalyst that is metered by the Dispense Pump.
Hardeners as used in Urethane or Epoxy paints become part
of the final product, whereas catalysts are typically used to
initiate a reaction in the paint material.
Depressurized
—No residual fluid or air pressure.
Diaphragm
—A part of the Air Flow Switch that relays
differential pressure to the amplifier and results in a signal to
the PLC. If this part is damaged or contaminated it may not
function properly and should be replaced.
Dispense Pump
—Dispenses hardener to the Mix
Manifold at the flow rate requested by the PLC. The dispense
pump is available in two different sizes.
Dispense Pump Flow Sensor
—The optional low flow
sensor placed at the inlet of the Dispenser Pump. It sends
a signal to the PLC when it senses fluid flow. Adjustable to
accommodate the various flow rate ranges.
EMS
—Acronym for the Binks Electronic Mix Solutions
system.