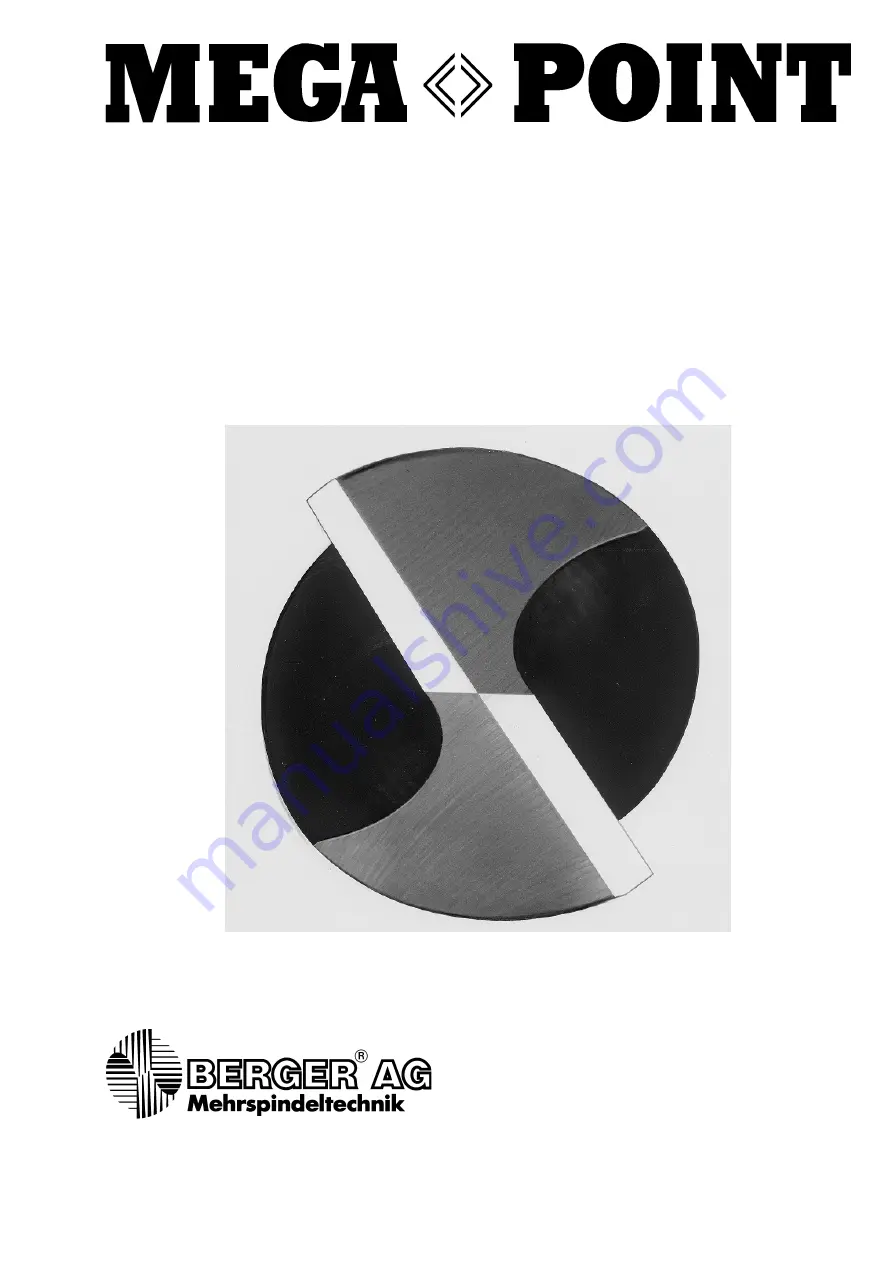
BERGER AG • Dept. Bohrerschleiftechnik
C.F.L. Lohnerstrasse 28E • CH-3645 Gwatt/Thun
T41 (0) 33 336 15 66 • T41 (0) 33 336 16 66
www.megapoint.ch • [email protected]
UNIVERSAL OPTICAL DRILL GRINDING MACHINE
O P E R AT I N G I N S T R U C T I O N S