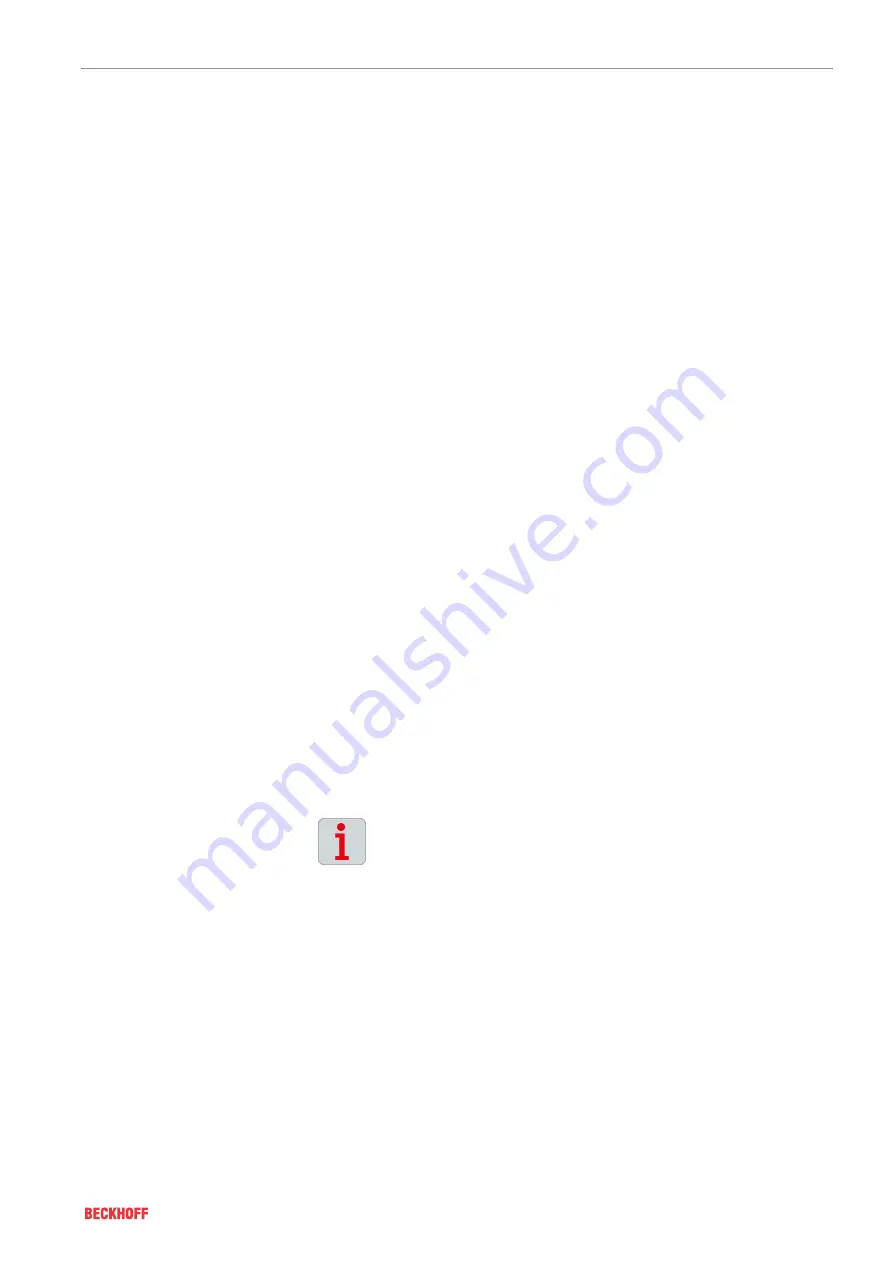
Product overview
Version: 1.1
───
31
AMP8000 and AMP8500
3.6
Product characteristics
No modification of the machine design
The AMP8000 can be mounted instead of a standard servomotor of
the AM8000 and AM8500 series without modifying the machine de-
sign, since only the overall length has been changed. All other di-
mensions remain unchanged.
Coupling module
Coupling modules are available for the AX8000 EtherCAT-based
servo drive system for connecting the distributed servo drives to the
PC-based control technology. With the 1-channel and 2-channel
coupling modules as the only component in the control cabinet, you
can establish the connection of the DC link, the 24 V
DC
supply and
the EtherCAT communication.
Reduced cable lengths and wiring work
Due to the high IP65 protection rating, you can integrate the distribu-
tion module directly into the machine layout. Only one cable must be
routed from the control cabinet or power supply module to the distri-
bution module.
Minimal floor space and cabling effort
You can connect the power supply module directly to the supply net-
work. Mains filter, rectifier and charging circuit for the integrated DC
link capacitors are provided in the power supply module.
EtherCAT P
Via the EtherCAT P M8 outputs at the power supply module and dis-
tribution module you can either supply EtherCAT P modules or con-
nect further power supply modules for system extension.
Holding brake [+]
The motors can be equipped as an option with permanent magnet
holding brakes. These operate according to the quiescent current
principle and open at a voltage of 24 V
DC
+6/-10 % with
> 10,000,000 switching cycles.
The installed holding brake is not suitable for service braking, since
there is no monitoring for wear and functionality by the servo drive
and the configuration. This applies in particular to vertical axes.
Safety measures for vertical axes must be applied
When operating vertical axes, appropriate additional measures
must be taken; for example, including but not only:
• additional redundant brake units
• mechanical safeguards or interlocks
• attachment of a balancing weight
Permanent magnet holding brakes alone are not approved for the
protection of persons. Taking ISO 13849-1 and 13849-2 into ac-
count, additional precautions must be taken for personal protection.
In the event of voltage interruptions due to emergency stop or power
failure, the holding brake is permissible as a service brake to a lim-
ited extent. You can perform a maximum of 2000 emergency stops
from a maximum of 3000 rpm with a maximum of three times the in-
trinsic inertia of the motor. These maximum values may vary due to
increased load inertia.
The function check of the holding brake can be performed with a
torque wrench or with TwinCAT Scope.
Summary of Contents for AMP8000
Page 1: ...Operating instructions EN AMP8000 and AMP8500 Distributed servo drives 11 15 2022 Version 1 1 ...
Page 2: ......
Page 43: ...Technical data Version 1 1 43 AMP8000 and AMP8500 4 3 1 2AMP8620 2005 0100 4 3 1 2 ...
Page 44: ...Technical data 44 Version 1 1 AMP8000 and AMP8500 4 3 1 3AMP8620 2005 0200 4 3 1 3 ...
Page 47: ...Technical data Version 1 1 47 AMP8000 and AMP8500 4 5 1 2AX8832 0000 0000 4 5 1 2 ...
Page 108: ......