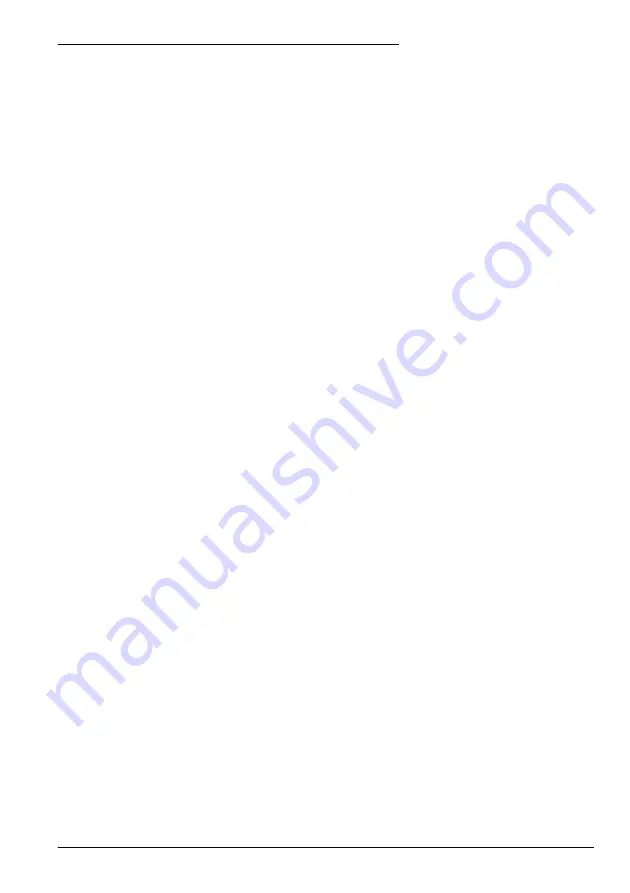
www.baldormotion.com
Troubleshooting 7-1
MN1901
7.1 Introduction
This section explains common problems that may be encountered, together with possible
solutions.
7.1.1 Problem diagnosis
If you have followed all the instructions in this manual in sequence, you should have few
problems installing the MintDrive
II
. If you do have a problem, read this section first.
In Mint WorkBench, use the Error Log tool to view recent errors and then check the help file.
If you cannot solve the problem or the problem persists, the SupportMe feature can be used.
7.1.2 SupportMe feature
The SupportMe feature (on the Help menu) can be used to e-mail information to the Baldor
representative from whom you purchased the equipment. If required, you can choose to add
your program files as attachments. Mint WorkBench will automatically start up your e-mail
program and begin a new message, with comprehensive system information and selected
attachments already in place. You can add any additional message of your own and then send
the e-mail. The PC must have email facilities to use the SupportMe feature. If you prefer to
contact Baldor technical support by telephone or fax, contact details are provided at the front
of this manual. Please have the following information ready:
H
The serial number of your MintDrive
II
.
H
Use the Help, SupportMe menu item in Mint WorkBench to view details about your
system.
H
The catalog and specification numbers of the motor that you are using.
H
Give a clear description of what you are trying to do, for example trying to establish
communications with Mint WorkBench or trying to perform fine-tuning.
H
Give a clear description of the symptoms that you can observe, for example the Status
display, error messages displayed in Mint WorkBench, or the current value of any of the
Mint error keywords
AXISERROR
,
AXISSTATUS
,
INITERROR
,
MISCERROR
and
DRIVEERROR
.
H
The type of motion generated in the motor shaft.
H
Give a list of any parameters that you have setup, for example the motor data you
entered/selected in the Commissioning Wizard, the gain settings generated during the
tuning process and any gain settings you have entered yourself.
7.1.3 Power-cycling the MintDrive
II
The term “Power-cycle the MintDrive
II
” is used in the Troubleshooting sections. On models
with a customer supplied 24V supply, remove the 24V supply, wait for the MintDrive
II
to power
down completely (all Status LED segments will turn off), then re-apply the 24V supply.
On models with an internally generated 24V supply, remove the AC power supply, wait for the
MintDrive
II
to power down completely (all Status LED segments will turn off), then re-apply AC
power.
7
Troubleshooting
7
Artisan Technology Group - Quality Instrumentation ... Guaranteed | (888) 88-SOURCE | www.artisantg.com