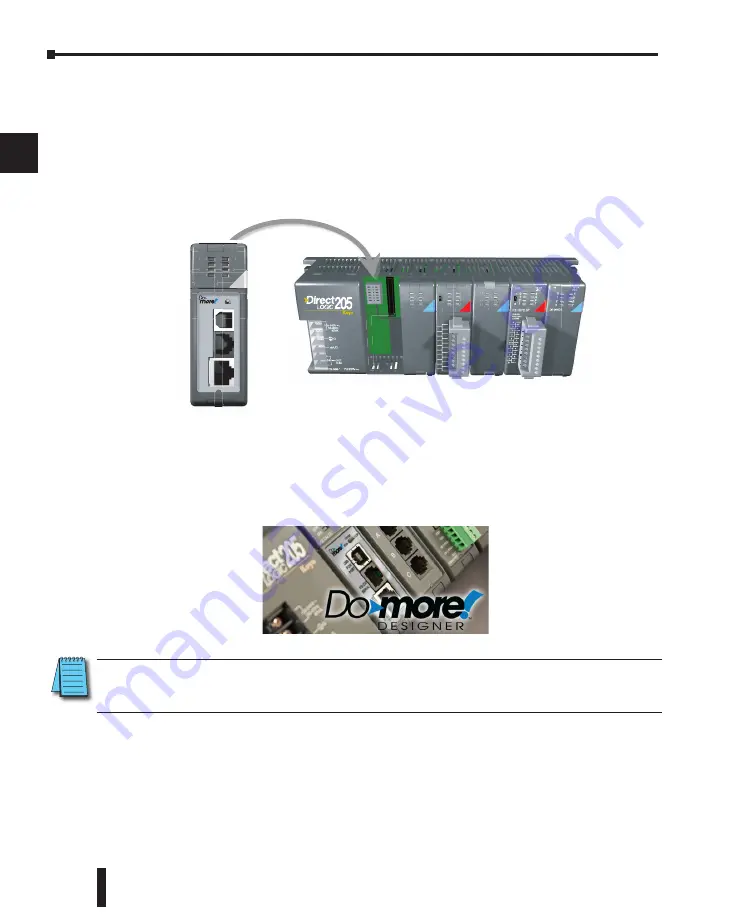
Do-more H2 Series PLC User Manual, 1st Edition, Rev. F - H2-DM-M
2–2
Chapter 2: Do-more PLC Hardware Overview
1
2
3
4
5
6
7
8
9
10
11
12
13
14
A
B
C
D
Do-more H2 Series PLC Overview
The Do-more H2 Series PLC is the first PLC series that we introduce to you as a part of the
Do-more PLC family. The Do-more H2 Series PLC utilizes most of the modules that we have
been selling as the DL205 PLC. You just need to install a Do-more H2 Series CPU module
into the DL205 base unit. However, the specifications of the Do-more H2 Series PLC are
very different from the DL205 PLC. This overview covers the key features of the Do-more
H2 Series PLC.
The Do-more H2 Series PLC is designed around a new control engine with a new, advanced
Do-more Instruction Set for ladder programs. The new Do-more Designer software, with
advanced programming and monitoring features, will be used to create your new programs.
NOTE:
Because the Do-more PLC supports a new instruction set and new memory addressing for ladder
programming, the user project made for the DL205 PLC CANNOT be used in the Do-more PLC. The
DL205 user project needs to be recreated from scratch for the Do-more PLC.
D2-08ND3
IN
12-24
VDC
0
1
2
3
4
5
6
7
D2-08ND3
IN
12-24
VDC
0
1
2
3
4
5
6
7
OUT
A
B
F2-16TD1P
12-24
VDC
10.2-26.4
VDC 0.25A
CLASS2
A
0
1
2
3
24V
0
1
2
3
B
0V
4
5
6
7
0V
4
5
6
7
0
1
2
3
4
5
6
7
D2-08ND
IN
0
1
2
3
P
12-24
VDC
4
5
6
7
Do-more H2 CPU Module
DL205 PLC base unit and I/O modules
H2-DM1E
PWR
RUN
ROM
ERR
ETH
USB
TX
RX
RS-232
SERIAL
USB
PGM
PORT
RUN
TERM
STOP
1
0
/
1
0
0
E
T
H
E
R
N
E
T
H2
H2
ER
ER
ER
ER
ER
R
ER
RR
ER
ER
ER
E
ER
ER
TERM
2-DM1EE
PWR
RUN
ROM
ETH
USB
TX
ROM
TX
2 DM1E
ERR
RX
E