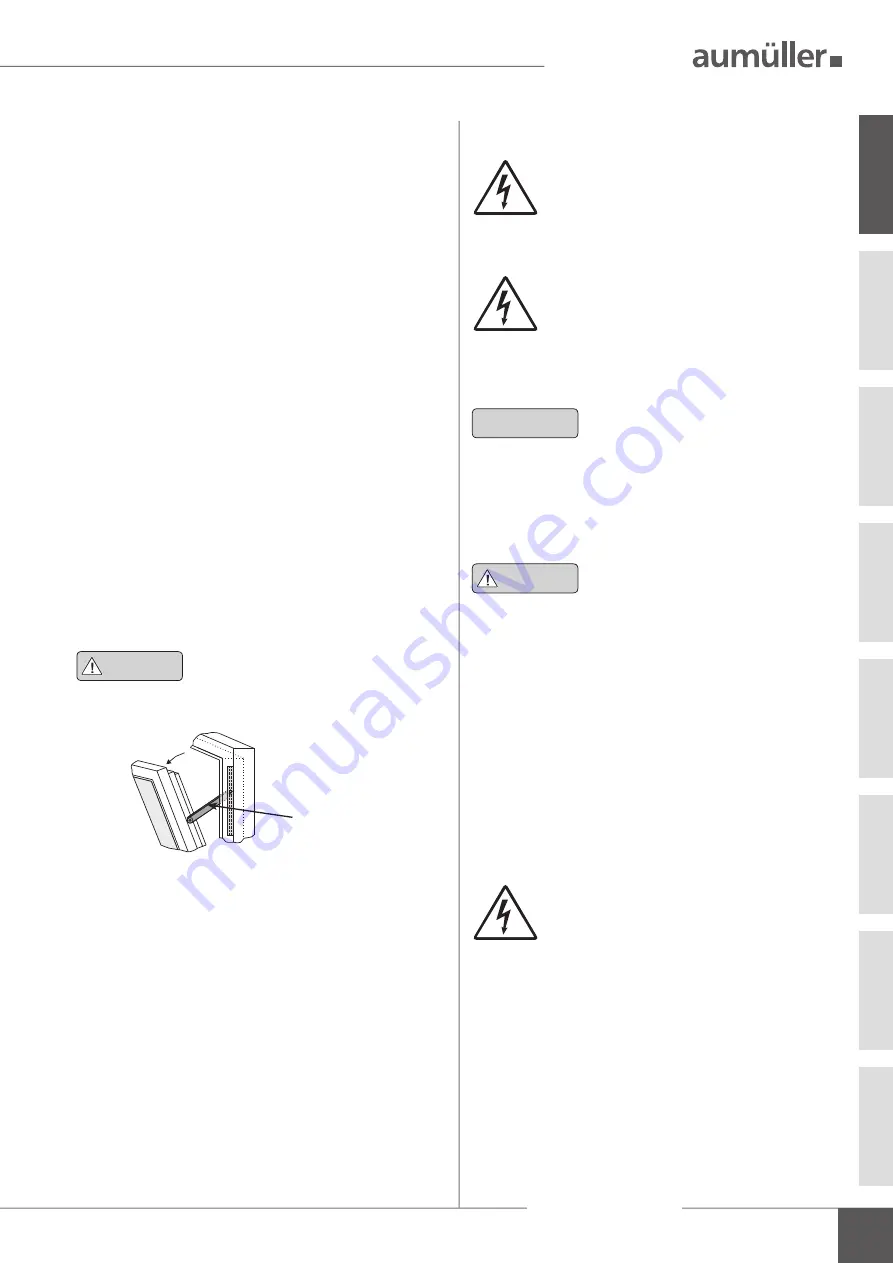
7
Assembly Instruction
FV1 / FV3 / FV4
s
afety
instruCtions
01
w
arning
w
arning
Crush and shear points
To avoid injuries,
crushing and shear points
between
casement and frame must be secured
against entrapment
up to an installation height of 2,5 meters above the
fl oor
with appropriate measures. This can be achieved e.g.
by using contact-based or contactless protective devices
against entrapment, which stop the motion through con-
tact or through interruption by a person. At a force higher
than 150 N at the main closing edge the motion must stop
within 20 mm. A warning symbol at the opening element
must indicate this clearly.
Unintentional or independent opening or falling
Casements are to be hinged or secured such way that in
case one of the mounting elements fails it will not crash /
slam down or move in an uncontrolled manner by e.g. using
double suspensions, safety scissors, casement stays.
Tilting windows shall be equipped with safety scissors or
similar devices to avoid damages and risks of injury for
persons through improper installation and operation. The
safety scissors must be adjusted to the opening stroke of
the drive (see technical data) to avoid blocking. The opening
width of the safety scissors must be bigger than the drive
stroke.
Routing cables and electrical connection
Routing or installing of electrical cables and connections
may be performed only by specialist companies. Never
operate drives, control units, operating elements and
sensors at operating voltages and connections contrary
to the specifi cations of the manufacturer.
All relevant national instructions shall be observed for
the installation.
The types of cable, cable lengths and cross-sections shall
be selected in accordance with the manufacturer’s technical
data. If necessary, the cable types shall be coordinated with
the competent local authorities and energy supply com-
panies. Low-voltage lines (24 V DC) shall be routed
separate from the high-voltage lines. Flexible cables may
not be fl ush-mounted. Freely suspended cables shall be
equipped with strain reliefs.
Clamping points shall be checked for tightness of threa-
ded connections and cable ends. Access to junction boxes,
clamping points and external drive control boxes shall be
ensured for maintenance work.
Damaged mains supply lines of drives
with plug connectors may only be re-
placed by the manufacturer or qualifi ed
service / maintenance personnel!
Power cables which are fi xed to the drive
casing cannot be replaced. If the cable is
damaged the device must be scrapped!
The movable casement must be secured
against unintentional or independent
opening as well as falling down.
All-pole disconnecting devices shall be instal-
led in the permanent electrical installation or
external Control Unit for the drive.
The mains supply lines 230 V / 400 V AC shall
be protected separately!
24V DC drives may only be connected to
power supply sources that comply with SELV
specifi cations.
Cables must be laid such way that they can-
not be sheared off, twisted or bent during
operation. Drive cables laid inside window
profi les must be protected by insulating
tubes with a suffi cient temperature resistance.
Through holes shall be equipped with cable
sleeves!
safety scissors
In the case of tandem / multiple opera-
tion of drives connected in series, the
cross-section of the connection cable
must be checked autonomously, depen-
ding on the total current consumption of
the drive system.
n
ote
Summary of Contents for FV1
Page 34: ...34 Assembly Instruction FV1 FV3 FV4 08...
Page 36: ...9000018401_V2 0_KW21 22...