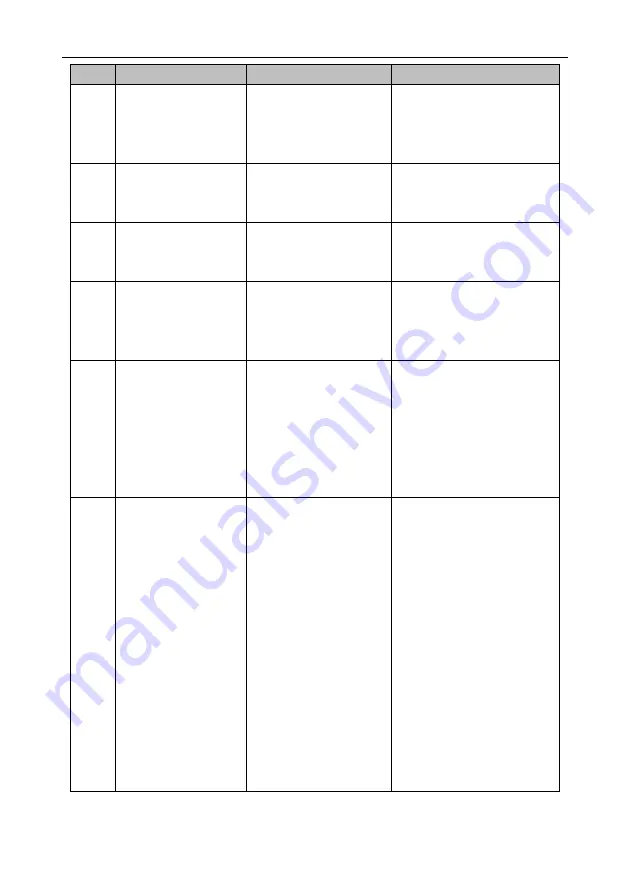
AS64 series AC servo drive Fault handling
-276-
Code
Name
Possible cause
Workaround
3. The setting of P4.32 is
less than that of P4.31.
4. The encoder feedback
signal is interfered.
5. Replace the motor with a new
one with a higher speed.
Er19-1
Speed fault–CCW
overspeed
The
speed
feedback
exceeds the setting of P4.40
by more than 20ms.
1. Ensure the encoder is normal.
2. Set P4.40 properly.
Er19-2
Speed fault–CW
overspeed
The
speed
feedback
exceeds the setting of P4.41
by more than 20ms.
1. Ensure the encoder is normal.
2. Set P4.41 properly.
Er19-3
Speed fault–Overspeed
parameter set incorrectly
The setting of P4.40 is less
than 0 or that of P4.41 is
greater than 0.
1. Ensure the encoder is
connected properly.
2. P4.40 or P4.41 is set
incorrectly.
Er19-4
Speed fault–Out-of-
control fault
The motor is out of control
due to the incorrect motor
power cable connection or
wrong motor code setting.
1. Ensure the encoder is
connected reliably.
2. Ensure the phase sequence of
the power cable is correct.
3. Ensure the motor code is
correct.
4. Set P4.35 to 0.
Er20-0
Speed deviation fault
In non-torque mode, the
deviation between the motor
speed and speed command
exceeds the setting of
P4.39.
1. The motor phases U, V,
and W are in reverse
sequence or motor cables
are not connected.
2. The motor load is too
heavy, which causes motor
stalling.
3. The drive force is
insufficient, which causes
motor installing.
1. Ensure the motor cable
phases are in correct sequence
and motor cables are connected
properly.
2. Check whether the conveyer
belt or chain is too tight or the
workbench
reaches
the
boundary
or
encounters
obstacles. If yes, resolve the
problem.
3. Ensure the speed loop control
parameters are set properly, the
drive is not damaged, and the
servo system model is correct.
4. Increase the setting of P4.39.