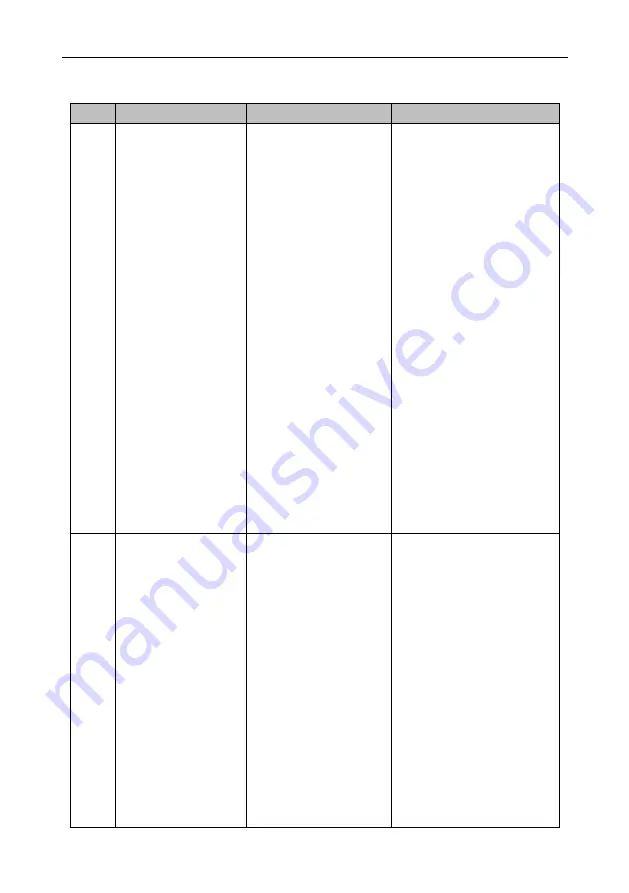
AS64 series AC servo drive Fault handling
-267-
9.1 Servo drive faults and workarounds
Code
Name
Possible cause
Workaround
Er01-0
IGBT fault
The drive actual output
current
exceeds
the
specified value.
1. Drive fault (such as drive
circuit or IGBT fault).
2. Drive cables U, V, and W
are short connected, or drive
cables are grounded or
contacted improperly.
3. The motor breaks down.
4. Drive cables U, V, and W
are connected in reverse
phases.
5.
Improper
parameter
settings
cause
system
divergence.
6. The ACC/DEC time in the
start or stop process is too
short.
7. Instantaneous load is too
heavy.
1. Remove the motor cables and
then enable the drive. If the fault
persists, replace the drive.
2. Ensure the motor cables and
wiring are in good conditions.
3. Reduce the settings of P0.10
and P0.11 to reduce the
maximum output torque.
4.
Commission
the
loop
parameters for system stabilizing
and reduce the setting of P0.12.
5. Increase the ACC/DEC time.
6. Replace the drive with a new
one with greater power.
7. Replace the motor.
Er01-5
IPM fault
The drive actual output
current
exceeds
the
specified value.
1. Drive fault (such as drive
circuit or IGBT fault).
2. Drive cables U, V, and W
are short connected, or drive
cables are grounded or
contacted improperly.
3. The motor breaks down.
4. Drive cables U, V, and W
are connected in reverse
phases.
1. Remove the motor cables and
then enable the drive. If the fault
persists, replace the drive.
2. Ensure the motor cables and
wiring are in good conditions.
3. Reduce the settings of P0.10
and P0.11 to reduce the
maximum output torque.
4.
Commission
the
loop
parameters for system stabilizing
and reduce the setting of P0.12.
5. Increase the ACC/DEC time.
6. Replace the drive with a new
one with greater power.
7. Replace the motor.