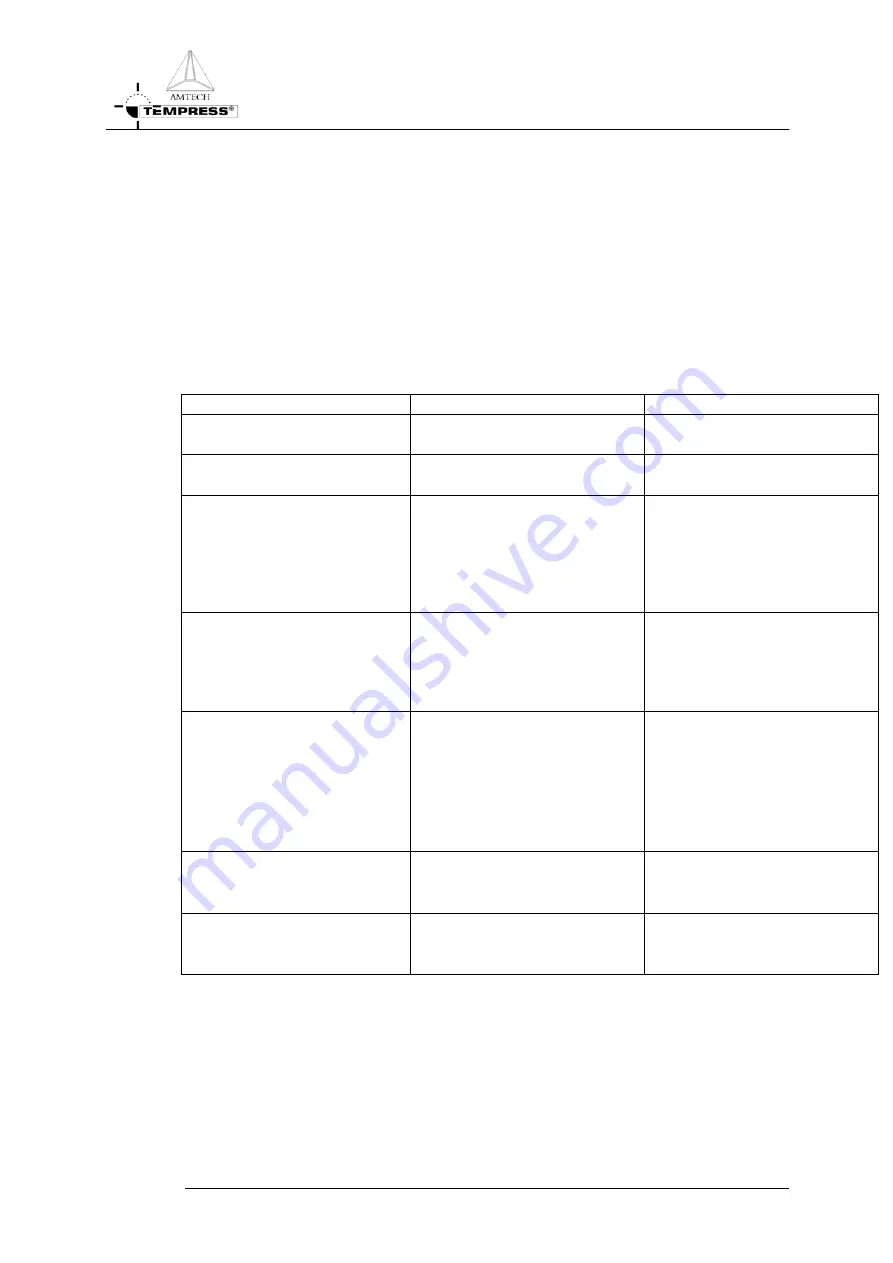
PROCESS DESCRIPTION
P
ROCESS
M
ANUAL
4.2-8
118
19 BACKFILL 2
119
Message BACKFILL [14]. Sonalert alarm No
120
Time: 000:10:00 (hr:min:sec) Variable Command: No
121
Gas N2 [1] at 100.0 [slm] Variable Command: No
122
Digital out N2 PURGE[9] = ON,N2PROCES[10] = ON,PROCESS[11] =
ON,EVACSIL1[12] = OFF,EVACSIL2[13] = OFF,EVACSIL3[14] =
OFF,SOFTSTRT[15] = OFF,MAINVAC[16] = OFF Variable Command: No
123
END
4.2.8
Troubleshooting a flat poly process
Problem: Cause:
Solution:
Wafers are thick at door side and
thin at pump side.
•
Gas distribution is incorrect
•
Increase gasload from the
pump side
Wafers are thick at the pump side
and thin at the door side.
•
Gas distribution is incorrect
•
Increase gasload from the
doorside
Wafers are thick at the top and
thin at the bottom.
•
The paddle is situated too
high in the tube.
•
The paddle is colder then the
wafers and the tube.
•
Adjust height of the paddle at
the cantilever system.
•
Insert temperature
stabilization step in the recipe
after ‘evacuate’ and/or ‘heat
up’ step.
Wafers are thick at the edges and
thin at the center.
•
Temperature is not
homogeneous within wafer.
•
Pressure is too high.
•
Insert temperature
stabilization step in the recipe
after ‘boat in’ and/or ‘heat up’
step.
•
Decrease pressure.
No consistency in uniformity.
•
Dirty quartz ware or wafers.
•
No constant pressure control.
•
Draft along the furnace.
•
Clean tube, quartz ware and
paddle.
•
Use clean wafers.
•
Check pressure control.
•
Decrease draft by reducing
overpressure cleanroom or
close possible draft holes.
Layer is too thin cross load.
•
Deposition time is too short.
•
Pressure is too low.
•
Increase deposition time in
recipe.
•
Increase pressure.
Layer is too thick cross load
•
Deposition time is too long.
•
Pressure is too high.
•
Decrease deposition time in
recipe.
•
Decrease pressure.