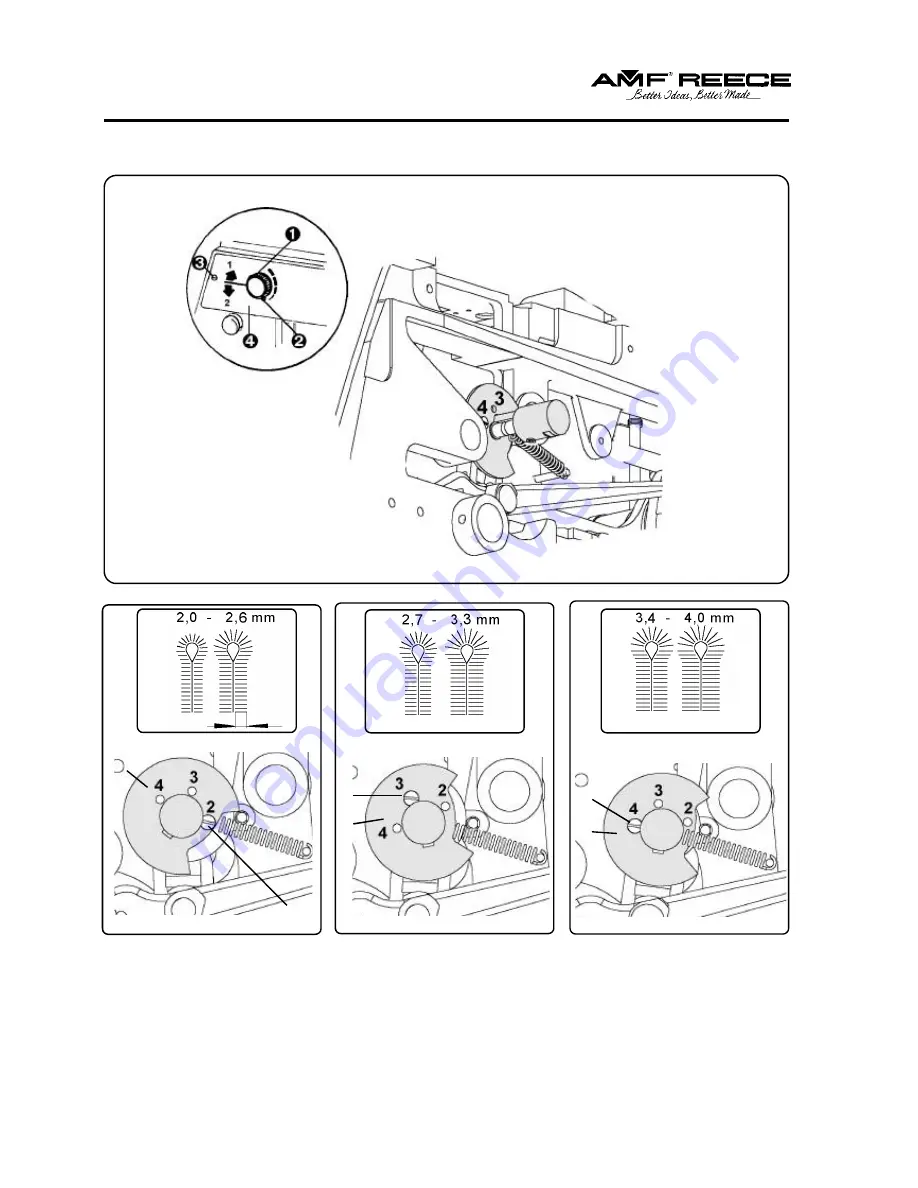
1-26
S100
Revised 10/2005
e-mail: [email protected] ; [email protected]; website: www.amfreece.com
Phones: +420 582 309 146 (Service), +420 582 309 286 (Spare Parts); Fax: +420 582 360 606
D -MACHINE ADJUSTMENT
4
3
Ï
Ï
Ï
Î
Î
Î
2
1-26
S100
Revised 10/2005
e-mail: [email protected] ; [email protected]; website: www.amfreece.com
Phones: +420 582 309 146 (Service), +420 582 309 286 (Spare Parts); Fax: +420 582 360 606
D -MACHINE ADJUSTMENT
4
3
Ï
Ï
Ï
Î
Î
Î
2