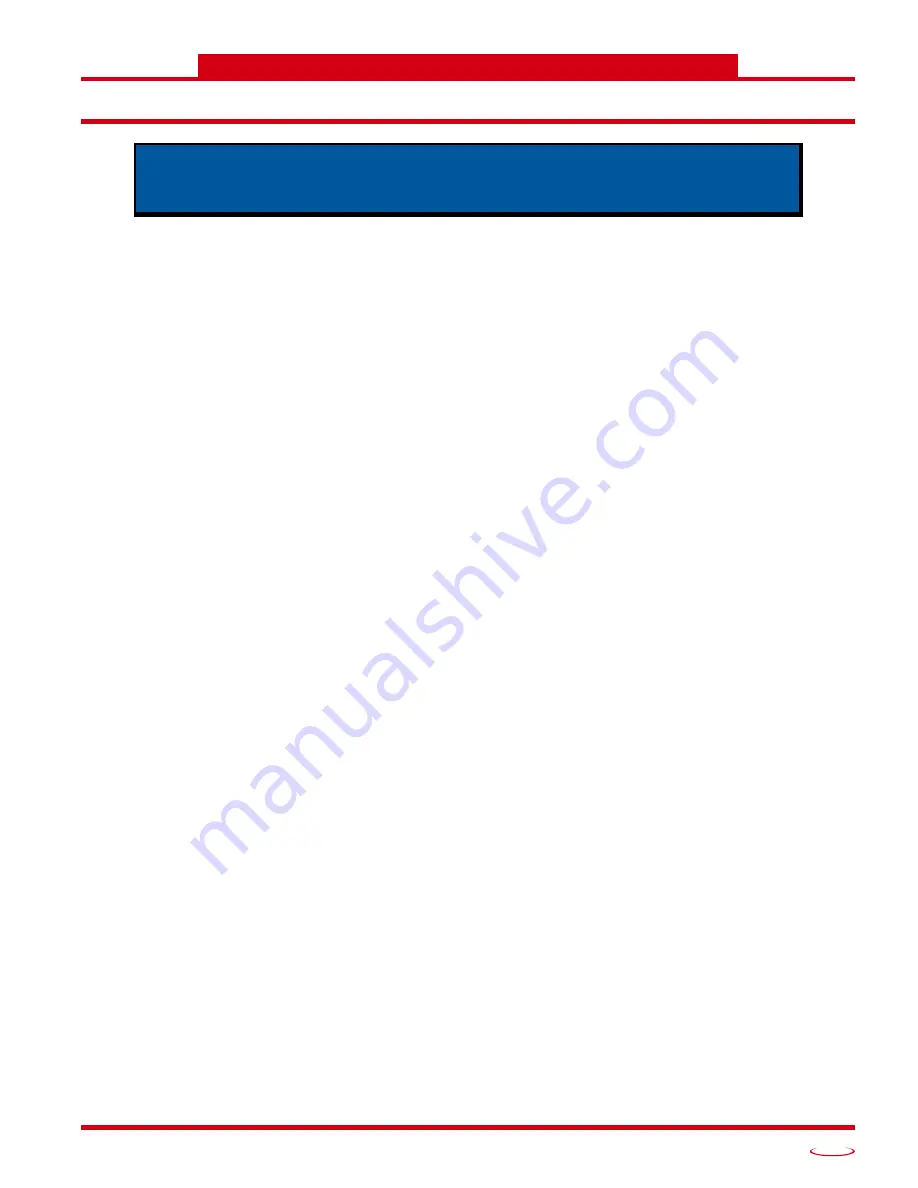
20 Gear Drive, Plymouth Ind. Park, Terryville, CT 06786
Tel: (860) 585-1254 Fax: (860) 584-1973 http://www.amci.com
21
REFERENCE 3
M
OTION
C
ONTROL
Definitions
Units of Measure
Distance:
Every distance is measured in steps. When you configure the unit, you will specify the number of
steps you want to complete one rotation of the motor shaft. It is up to you to determine how many steps are
required to travel the appropriate distance in your application.
Speed:
All speeds are measured in steps/second. Since the number of steps needed to complete one shaft
rotation is determined by your programming, it is up to you to determine how many steps per second is
required to rotate the motor shaft at your desired speed.
Acceleration:
The typical unit of measure for acceleration and deceleration is steps/second/second, or steps/
second
2
. However, when programming a Networked Driver, all acceleration and deceleration values must be
programmed in the unit of measure of steps/second/millisecond.
To convert from steps/second
2
to steps/second/millisecond, divide the value by 1000. This must be done
when converting from a value used in the equations to a value programmed into a Networked Driver.
To convert from steps/second/millisecond to steps/second
2
, multiply the value by 1000. This must be
done when converting from the value programmed into a Networked Driver to the value used in the
equations.
Motor Position
Motor Position is defined in counts. The range is -2,147,483,648 to +2,147,483,647.
Home Position
The Home Position is any position on your machine that you can sense and stop at. There are two ways to
defining the Home Position. The first is using the Preset Position command to set the Motor Position register
to a known value. The second method is using one of the
Find Home
commands. If you use the unit’s
Find
Home
commands, the motor position and encoder position registers will automatically be set to zero once the
home position is reached. Defining a Home Position is completely optional. Some applications, such as those
that use the Networked Driver for speed control, don’t require position data at all.
Count Direction
Clockwise moves will always increase the motor position register reported back to the host. Some of the
moves, such as the Jog Move, have a positive and negative command. A positive command, such as the +Jog
Move command, will result in a clockwise rotation of the shaft.
Starting Speed
The Starting Speed is the speed that most moves will begin and end at. This value is set while configuring the
unit and it has a valid range of 1 to 1,999,999 steps/second. This value is typically used to start the move
above the motor’s low frequency resonances and, in micro-stepping applications, to limit the amount of time
needed for acceleration and deceleration. AMCI does not specify a default value in this manual because it is
very dependent on motor size and attached load.
When a move command is sent to a Networked Driver, the unit calculates the
entire profile before starting the move or issuing an error message. This chapter
explains how the profiles are calculated and the different available moves.