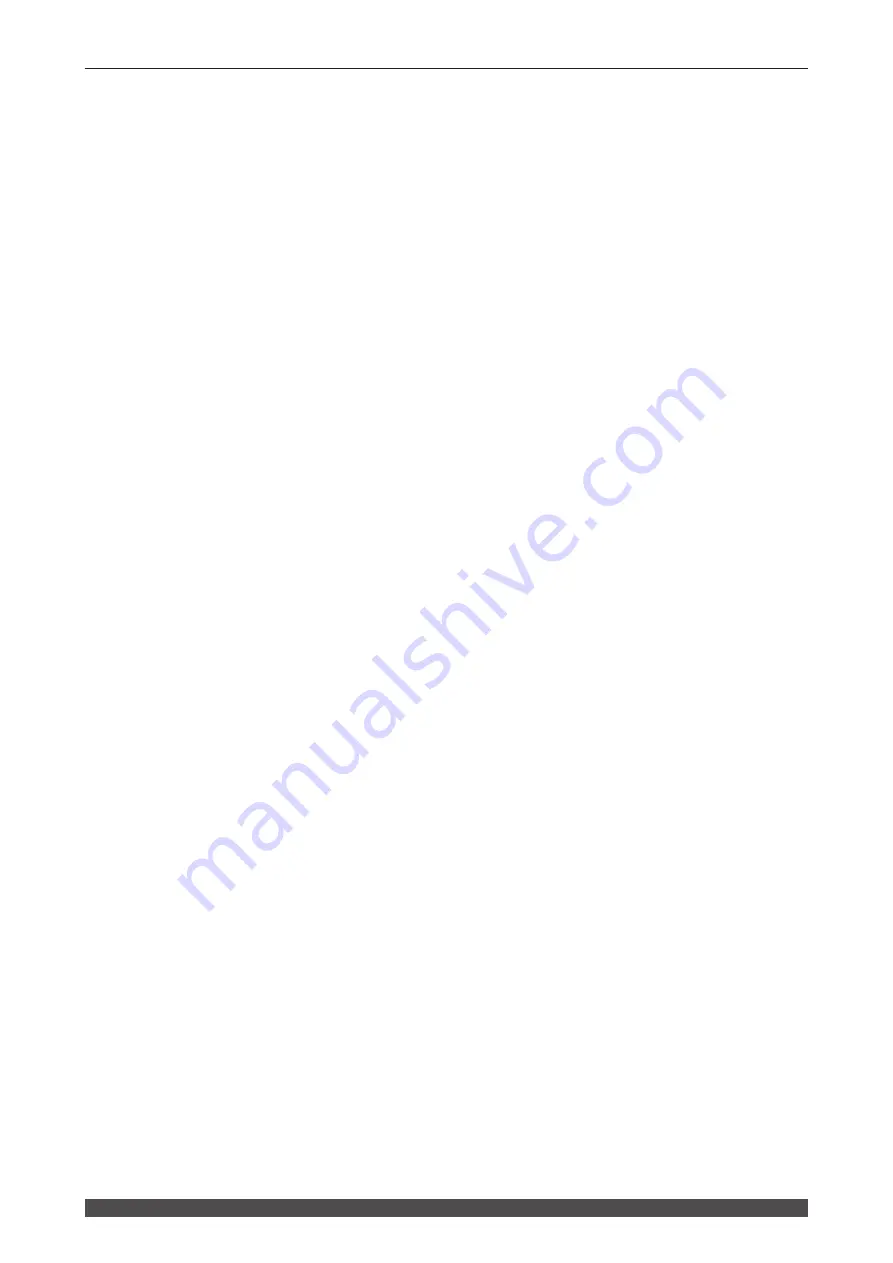
228
ML-2550A/2551A
Index
output value 79
peak value of laser output 65
POINT 66
up-sloping 66
Laser light (monitor)
appropriate number of laser light outputs 69, 88
average power 69
Lamp Input Power 92
lower limit value 69
measured value 69
total number of laser light outputs 69, 88
upper limit value 69
LASER POWER MONITOR 120
Laser Safety Supervisor 10
LASER START/STOP button 33, 118
Lithium Battery 195
LOW 69
M
MAIN SHUT 63
MAIN SWITCH Switch 29
MAIN UNIT 68
MEMORY SWITCH Screen 75, 98, 101, 112
MONITOR Screen 69, 91
N
O
Optical Fiber
fiber breakage detecting function 115
fiber mount checking function 115
Incident Beam Adjustment 193
LED ON checking function 115
Maximum Incident Laser Energy 51
Minimum bending radius 10, 50
Optical Fiber Inlets 32
Options 27
Output Unit 53
Output Unit with Fiber Sensor 114
P
Package for accessories 24
PANEL CONTROL 59, 86
password 94
PASSWORD Screen 71, 94
PEAK POWER 65, 121
PLC 127
POINT 66
POSITION AUTO-OFF 73
Power input terminals 47
POWER Lamp 33
Power Monitor Unit 35
powersharing 22, 104
Power Supply Terminals 30
PRESET COUNT 68
Primary Cooling Water 179
Printer 28
PRINTOUT SCHEDULE 72
PRINTOUT Screen 72
PROGRAM UNIT 68
Pulse width
PUMP 63
R
READY Lamp 33
REFERENCE SETTING 69
REFERENCE VALUE 66
REF TEMP 73
REMOTE INTERLOCK Connector 31, 136
REPEAT 67, 79
RESET COUNT 68
Resonator Mirror Holder 35
Resonator Shutter 35
RS-232C/RS-485 conversion adapter 56
RS-485 CONTROL 60, 87
Code Table 151
Communication Schedules 147
Control Codes 151
RS-232C/RS-485 conversion adapter 28
RS-485 (1) Connector 30
RS-485 (2) Connector 30
Set Value/Monitor Value Table 155
Table of Error Contents 167
S
SCHEDULE 63
SCHEDULE screen 65, 78
Schedule Signal Acceptance Time 111
Secondary Cooling Water 181
Sharing
Controlling Branch Shutters Independently
DIP switch 107
Summary of Contents for ML-2550A
Page 1: ...AA06M0642E 37 OPERATION MANUAL YAG LASER WELDER ML 2550A 2551A...
Page 19: ...Introduction Part...
Page 20: ......
Page 37: ...Installation and Preparation Part...
Page 38: ......
Page 46: ......
Page 57: ...Operating Part...
Page 58: ......
Page 116: ......
Page 144: ......
Page 168: ......
Page 173: ...Maintenance Part...
Page 174: ......
Page 203: ...Appendixes...
Page 204: ......