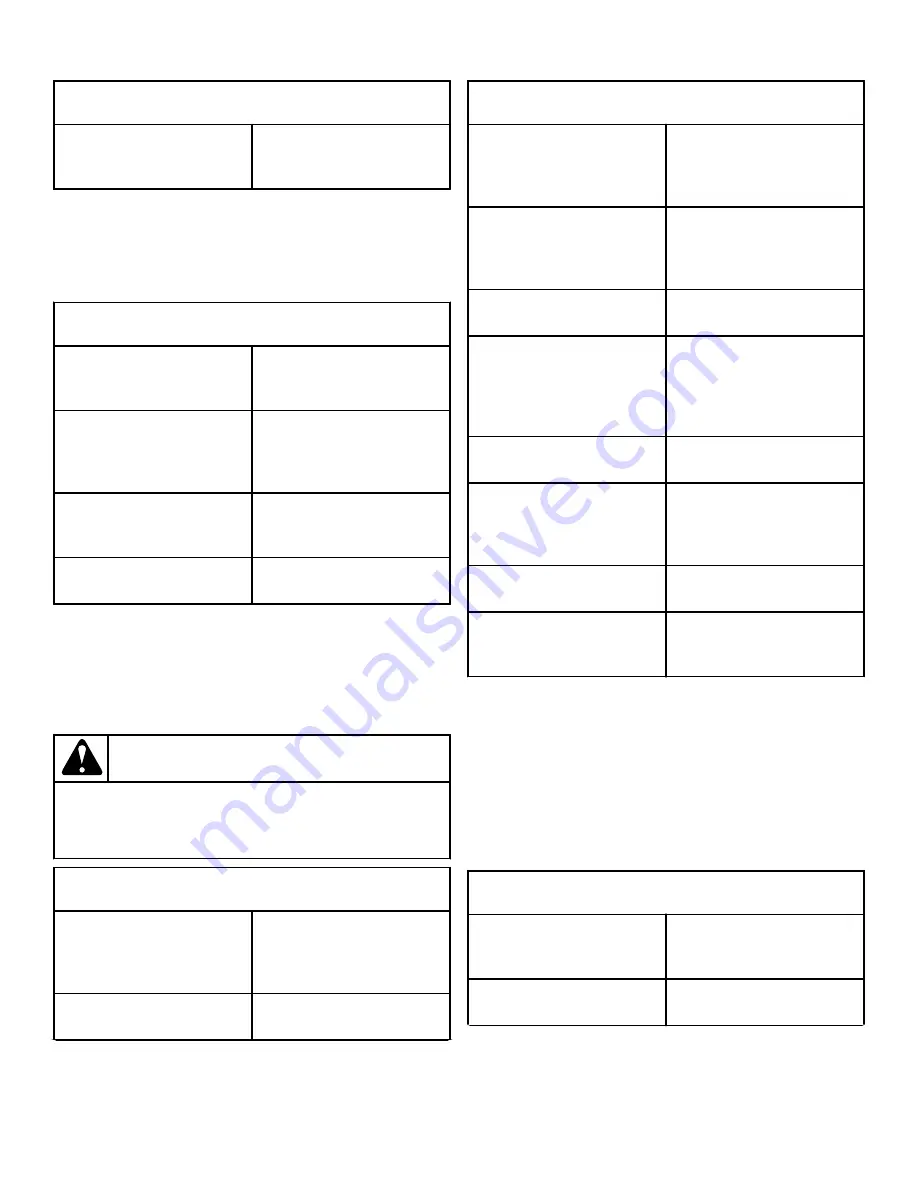
Diagnosing Failure 9
5. Check the output relay that
powers the door lock coil.
If the relay stays closed and
the relay is broken, replace the
wash computer.
Table 60
Failure 10: Target Temperature not Reached
If requested temperature is not reached during step then error 10
is generated.
Diagnosing Failure 10
1. Check if the heating contac-
tor is activated
If the heating contactor is not
activated: repair the wiring or
replace the contactor.
2. Check if the heating ele-
ments are heating.
If the heating elements are not
heating: Repair the wiring or
replace the defective heater el-
ements.
3. Check if the temperature
sensor is functioning.
If the temperature sensor is de-
fective: replace the tempera-
ture sensor.
4. Check the output relay that
powers the heating contactor.
If the relay is broken, replace
the wash computer.
Table 61
Failure 11: Fill Failure
Failure 11 occurs when the water level has not reached its target
level in x minutes. x = maximum fill time, a value that can be
programmed at the Initialization Menu.
WARNING
The rubber hose must be fixed with a flexible clamp
on the electronic water level sensor. .
C078
Diagnosing Failure 11
1. Check if the programmed
maximum fill time in the Initi-
alization menu is acceptable.
If the water flow is very slow,
increase the value for the max-
imum fill time. The default
value is 10 minutes.
2. Check if the external water
valves are open.
If the water valves are closed:
open the water inlet valves.
Table 62
continues...
Diagnosing Failure 11
3. Check if the water inlet
valves are not blocked by dirt.
If the water inlet valves are
blocked by dirt: clean the wa-
ter inlet valves or replace the
water inlet valves.
4. Check the coil of the water
inlet valves.
If the coil of the water inlet
valve is electric open: replace
the coil or the complete water
inlet valve.
5. Check the drain valve.
If the drain valve is defective:
replace the drain valve.
6. Check if the rubber hose
(for measuring the water level)
is well mounted on the elec-
tronic level sensor and on the
drain valve.
If the hose is not well mount-
ed: install the rubber hose
properly.
7. Check if the hose on the
electronic sensor is air tight.
If the air hose is not air tight:
replace the air tube.
8. Check if the hose doesn’t
contain water. (siphon)
If the air tube contains water:
remove the water and fix the
hose so that it doesn’t work as
a siphon.
9. Check the continuity of the
wiring.
If the wiring is not continuous:
repair the wiring.
10. Check the output relay that
powers inlet valves and the
drain valve.
If the relay receives a com-
mand signal but is not closed,
replace the wash computer.
Table 62
Failure 12: Overfill Failure
If the target water level is X units above the target level then fail-
ure message 12 will be displayed.
The fault message will not be generated when the user is advanc-
ing from a sequence with a high water level to a sequence with a
low water level. X= "Maximum level Overfill", a value that can
be programmed at the Initialization menu.
Diagnosing Failure 12
1. Check if the water inlet
valves are broken.
If the water inlet valves are
broken: clean or replace the
water inlet valve diaphragms.
2. Check if the water pressure
is too high.
Lower the water pressure.
Table 63
continues...
Troubleshooting
©
Copyright, Alliance Laundry Systems LLC -
DO NOT COPY or TRANSMIT
91
Part No. D1631ENR7
Summary of Contents for IYG065J
Page 2: ......