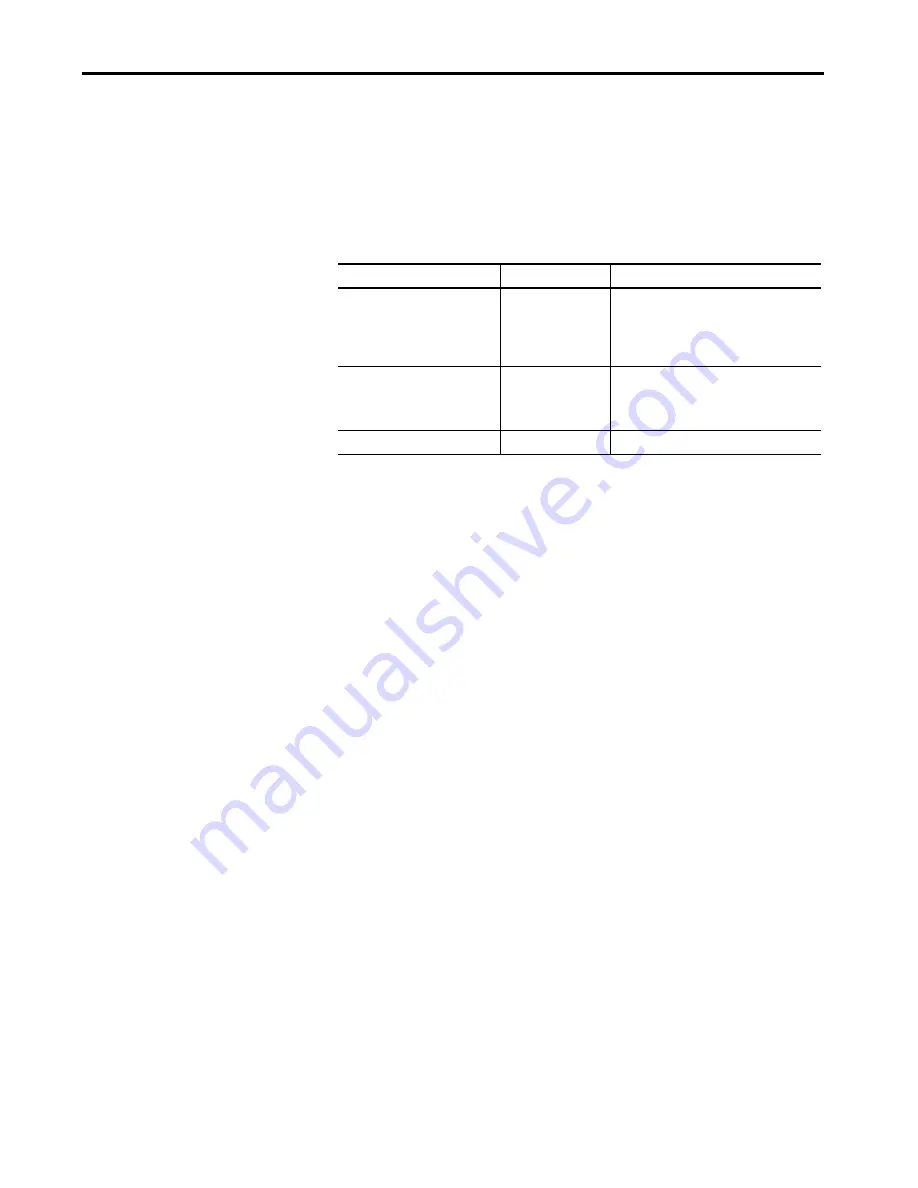
Rockwell Automation Publication 1444-UM001D-EN-P - June 2018
221
Configure Alarms
Chapter 8
In this example (shown) the multipliers are set based on Speed(0). The table, as
entered, results in the following:
• From 0…400 RPM, the alarm limits are multiplied by 1.5
• From 400…1200 RPM, the alarm limits are multiplied by 3.0
• Above 1200 RPM, the alarm limits are not multiplied (x1.0)
Adaptive Limits page parameters are:
Output Tag Limits
A third alternative to how limits are defined is to use output tag limits. Output
tag limits are enabled in Module Definition on the select data to be added to
the output tag page. In the controller output assembly,16 values (REALs) are
included for use as alarm limits. When ‘output tag limits’ is selected as the
alarm limits source, the high/low, danger/alert limits are mapped to selected
output tag locations.
When in this mode, the module applies the alarm limits as read from the
controller output tag. This mode then enables programmatic control of the
limits from the Logix controller, which provides a far more powerful alarm
management capability.
When output tag limits are applied, the limits read from the output assembly
are used directly and never multiplied.
Parameter
Values
Help
Control Parameter
Select from list of
measured values
While the complete list of measured values is
presented, in almost all cases the multipliers are
based on one of the four possible speed
selections: Speed(0), Factored Speed(0),
Speed(1), Factored Speed(1),
Control Parameter High Range Limit
0.00 … 50000.00
The respective multiplier is applied when the
control parameter is greater than the previous
entry high limit (or 0) and is less than or equal to
this value.
Alarm Limit Multiplier
0.01 … 100.00
The value that the alarm limits are multiplied by.