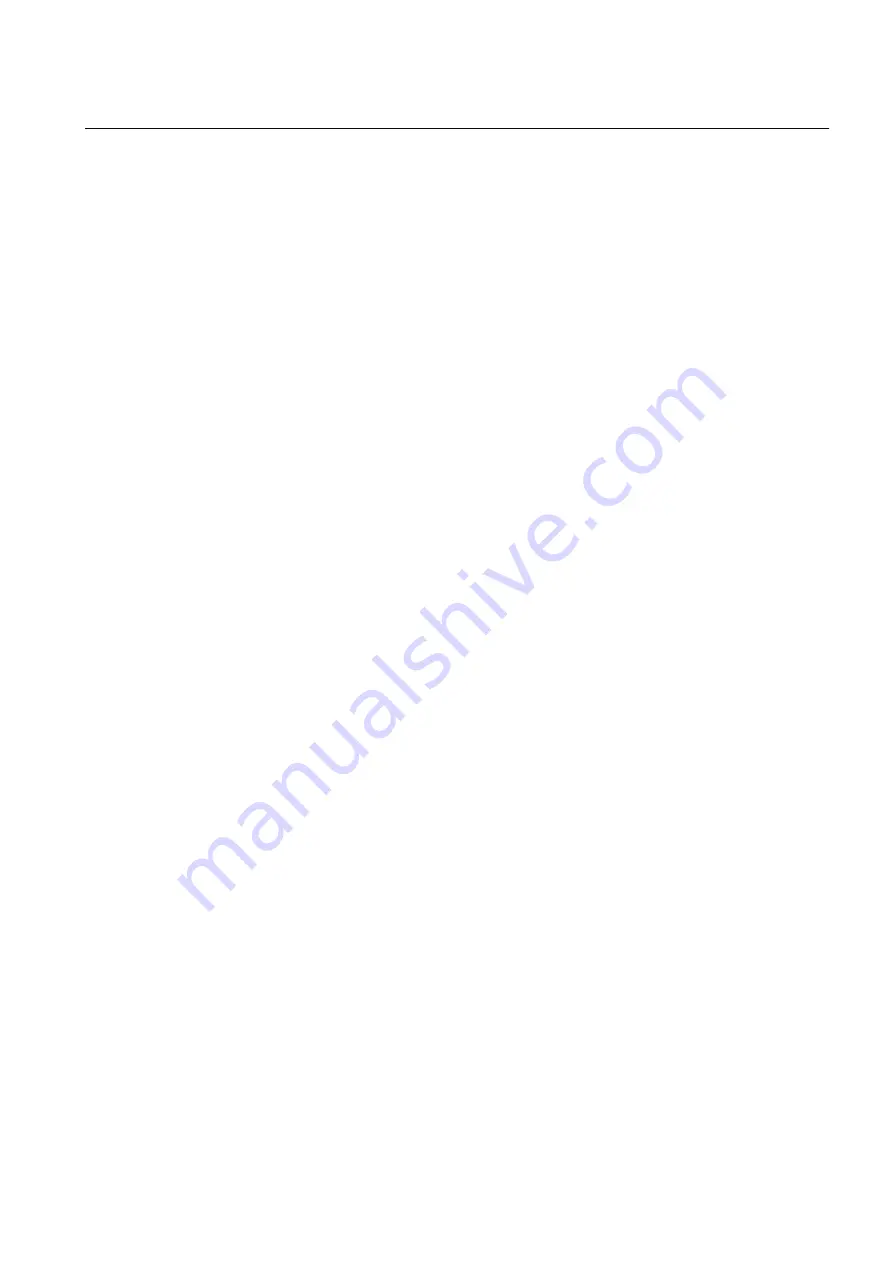
Energizing the IED............................................................................77
Design..............................................................................................78
Checking the self supervision signals...............................................80
Determine the cause of an internal failure..............................80
Self supervision HMI data............................................................81
Section 8 Set up the PCM600 communication link per IED...........83
Setting up communication between PCM600 and the IED...............83
Section 9 Establishing connection and verifying the SPA/IEC-
communication ..............................................................89
Entering settings...............................................................................89
Entering SPA settings..................................................................89
Entering IEC settings...................................................................90
Verifying the communication............................................................90
Verifying SPA communication.....................................................90
Verifying IEC communication......................................................91
Fibre optic loop.................................................................................91
Optical budget calculation for serial communication with SPA/
Section 10 Establishing connection and verifying the LON
communication ..............................................................93
Communication via the rear ports ....................................................93
LON communication....................................................................93
The LON Protocol........................................................................94
Hardware and software modules.................................................95
Optical budget calculation for serial communication with LON ........97
Section 11 Establishing connection and verifying the IEC 61850
communication...............................................................99
Overview...........................................................................................99
Setting the station communication....................................................99
Verifying the communication..........................................................100
Section 12 Configuring the IED and changing settings..................101
Overview.........................................................................................101
Entering settings through the local HMI..........................................102
Configuring analog CT inputs.........................................................102
Downloading settings and configuration from a PC........................103
Writing an application configuration to the IED..........................103
Section 13 Verifying settings by secondary injection ....................105
Table of contents
3
Installation and commissioning manual
Summary of Contents for RELION RET670
Page 1: ...Relion 670 series Transformer protection RET670 Installation and commissioning manual...
Page 2: ......
Page 16: ...10...
Page 24: ...18...
Page 26: ...20...
Page 28: ...22...
Page 82: ...76...
Page 88: ...82...
Page 94: ...88...
Page 104: ...98...
Page 110: ...104...
Page 210: ...204...
Page 230: ...224...
Page 239: ...233...