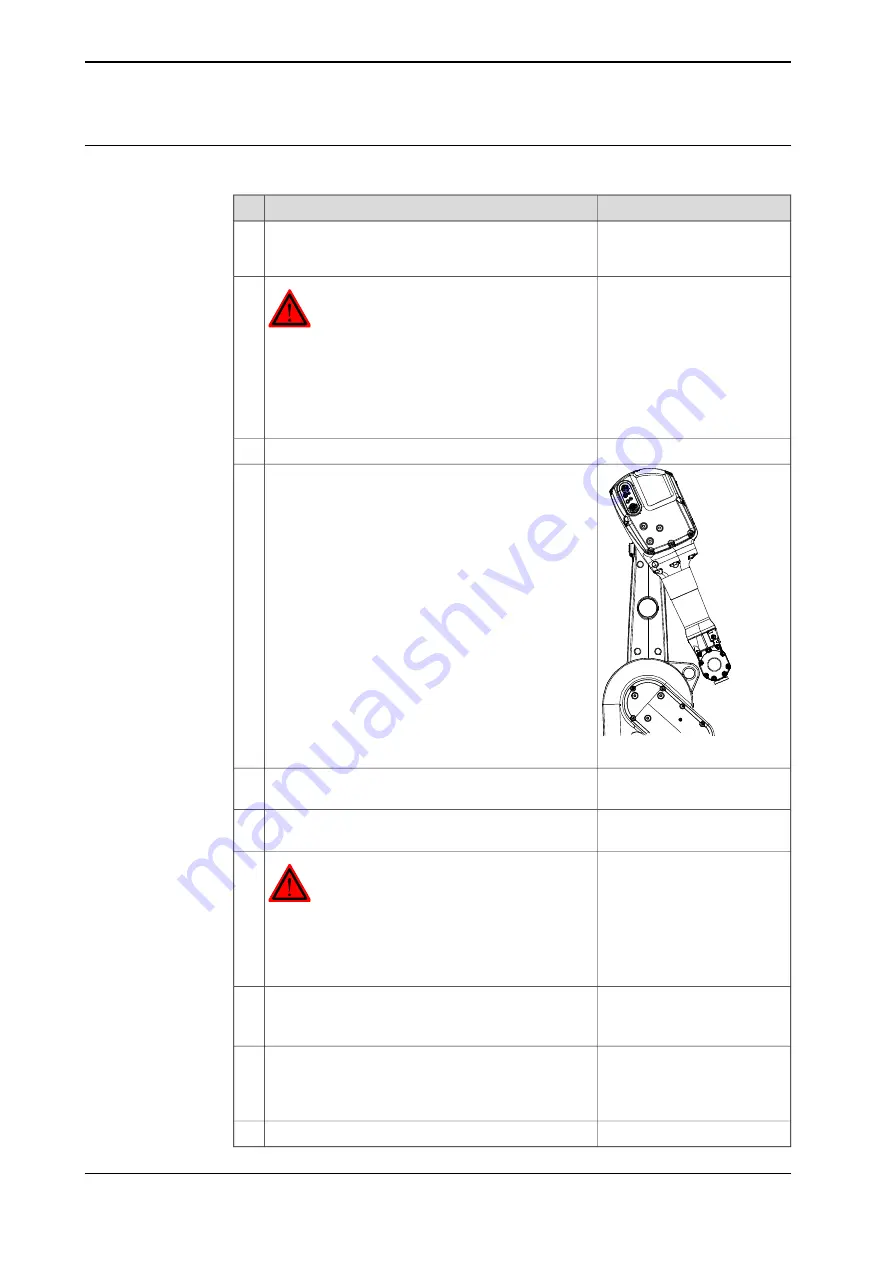
Removal, motor axis 3
The procedure below details how to remove the axis 3 motor.
Note
Action
Decide which calibration routine to use, and take ac-
tions accordingly prior to beginning the repair proced-
ure.
1
DANGER
Turn off all:
•
electric power supply
•
hydraulic pressure supply
•
air pressure supply
to the robot, before entering the robot working area.
2
Remove any additional mechanical stops from axis 3.
3
xx0500001447
Move:
•
axis 2 to calibration position
•
upper arm backwards against the mechanical
stop.
This position enables removal of the motor without
draining of the gearbox, axis 3.
4
Shown in the figure
.
Remove the
upper arm housing cover
.
5
Shown in the figure
.
Disconnect the motor connectors R3.MP3 and R3.FB3.
6
DANGER
Secure the weight of the upper arm properly before
releasing the brakes of motor, axis 3.
When releasing the holding brakes of the motor, the
upper arm will be movable and may fall down!
7
Connect to connector R3.MP3:
•
+: pin 7
•
-: pin 8
In order to release the brakes, connect the 24 VDC
power supply to the motor.
8
Remove the motor, axis 3, by unscrewing its attach-
ment screws and washers.
9
Lift the motor gently straight out, making sure the
motor pinion is not damaged.
Disconnect the brake release voltage.
10
Continues on next page
270
Product manual - IRB 1600/1660
3HAC026660-001 Revision: W
© Copyright 2006-2018 ABB. All rights reserved.
4 Repair
4.6.3 Replacement of motor, axis 3, IRB 1600
Continued
Summary of Contents for IRB 1660
Page 1: ...ROBOTICS Product manual IRB 1600 1660 ...
Page 8: ...This page is intentionally left blank ...
Page 18: ...This page is intentionally left blank ...
Page 48: ...This page is intentionally left blank ...
Page 152: ...This page is intentionally left blank ...
Page 336: ...This page is intentionally left blank ...
Page 372: ...This page is intentionally left blank ...
Page 388: ...This page is intentionally left blank ...
Page 396: ......
Page 397: ......