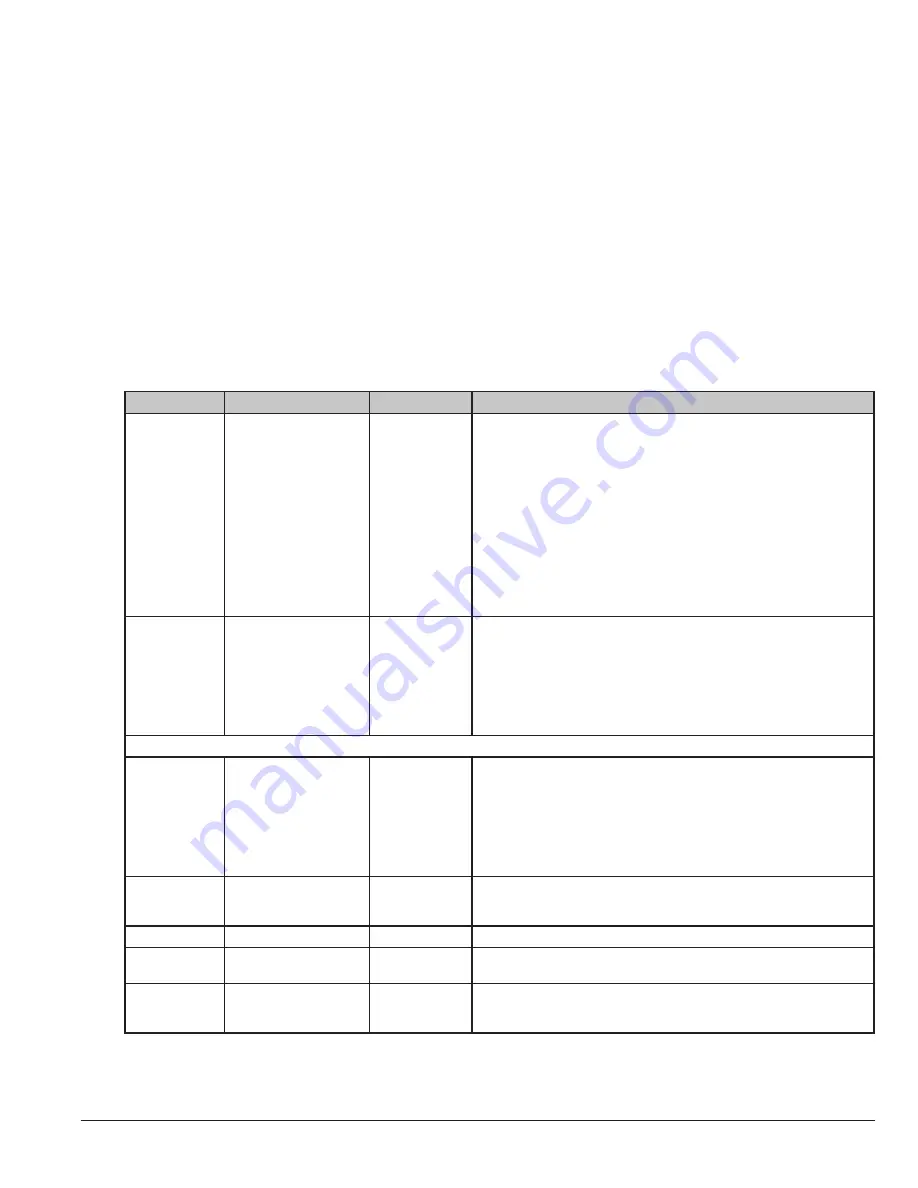
Standalone Motor and ABB Drive Setup 11-5
MN448
11.6 Start Mode Selection with FASR Motors
Automatic start
With the ACH580 and EC Titanium Motor, it’s recommended to set 21.01 (Vector start mode) = 2 automatic and Parameter
21.03 (Stop mode) = 0 for coast stop. Parameter 21.13 (Autophase mode) should be changed to Turning.
The start of PM motors consists of two parts:
1. Flying start detection: If the motor is rotating, flying start is performed
2. Autophasing detection: If the motor is not rotating, Autophasing is executed after Flying start detection.
After these start routines, the motor is controlled normally with Vector control.
NOTE
: Autophasing in this product range is done with DC current injection. The shaft of motor may rotate slightly forward/
backwards during the autophasing, depending on the true orientation of the axis. If axis movement need to be
avoided, then Ramp stop & Post-magnetization may help. In this case drive starts the rotation from same phase from
where the motor was stopped.
Parameter
Name
Value
Description
21.01
Vector start mode
2
Selects the motor start function for the vector motor control
mode, ie. when 99.04 Motor control mode is set to Vector.
Automatic:
With permanent magnet motors, start mode
Automatic is recommended. Under Automatic the drive motor
control program identifies the flux as well as the mechanical
state of the motor and starts the motor instantly under all
conditions.
Automatic start guarantees optimal motor start in most cases. It
includes the flying start function (starting to control the rotating
motor and accelerating it to the reference speed) and the
automatic restart function (restarting the drive automatically after
a short – max. 10 seconds – power supply failure).
21.03
Stop mode
0
Selects the way the motor is stopped when a stop command is
received.
Coast stop
Stop by switching off the output semiconductors of the drive.
The motor coasts to a stop. It is recommended to use Coast
stop if possible when using the ACH580 with the EC Titanium
motor for best start performance.
When start performance is critical or shaft movement in start need to be minimized apply the following additional settings.
21.03
Stop mode
1
Selects the way the motor is stopped when a stop command is
received.
Ramp stop
Stop along the active deceleration ramp. See parameter
group 23 Speed reference ramp. This mode may be selected
if the application requires a faster stopping time then the
recommended coast to rest mode.
21.08
DC current control
Bit 0 = 1
Bit 1 = 1
Bit 0 = 1 Enable DC hold
Bit 1 = 1 Enable post-magnetization
21.09
DC hold speed
~30 rpm
Depends on the application and motor, but 30rpm is typically ok
21.10
DC current
reference
~50%
Depends on the application and motor, but 50% is typically ok.
21.11
Post -
magnetization
time
~2s
Depends on the application and motor, but 2 s is typically ok.
Summary of Contents for EC Titanium ECS100A1H1DF4
Page 1: ... MN448_May 2020 May 2020 EC Titanium Manual User s guide ...
Page 10: ...1 4 Introduction MN448 ...
Page 20: ...3 4 Mechanical Information and Mounting MN448 ...
Page 26: ...4 6 Electrical Installation and Planning MN448 ...
Page 32: ...5 6 Control Pad Wiring and Keypad Interface MN448 ...
Page 36: ...6 4 Keypad Programming and Basic Operation MN448 ...
Page 44: ...8 4 Parameter Navigation and Groups MN448 ...
Page 51: ...9 7 Control Modes MN448 ...
Page 77: ...11 8 Standalone Motor and ABB Drive Setup MN448 ...
Page 99: ...A 12 Modbus RTU Example Connection MN448 ...
Page 102: ......