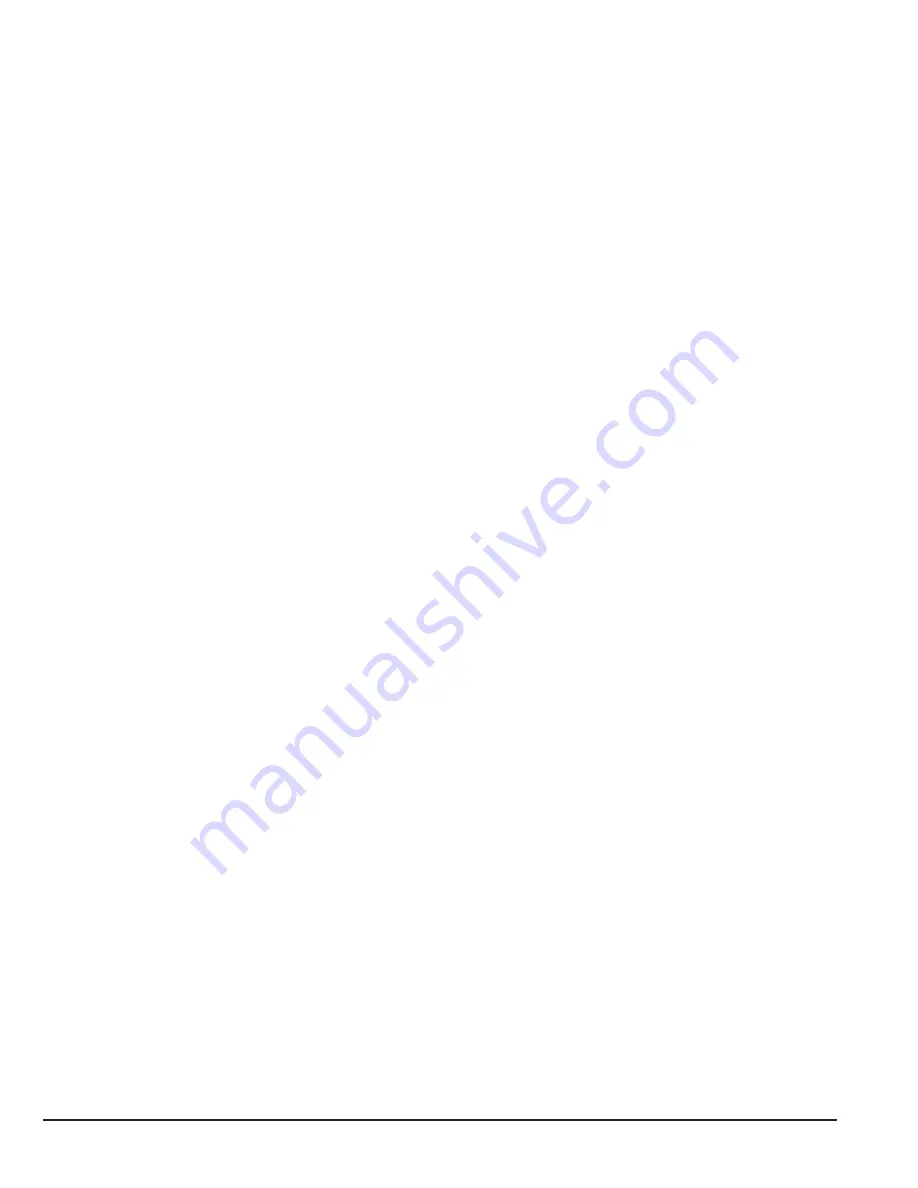
5-4 Control Pad Wiring and Keypad Interface
MN448
5.3.4 To setup the communication address
On first power up, the REMOTE PANEL will communicate with network drive address 1 and initially display “
SCAN
..”
indicating the REMOTE PANEL is searching for a drive with network address 1.
“
Load
..” is displayed indicating the keypad is reading configuration information from the drive. After 1~2 seconds, data has
been loaded and the REMOTE PANEL will display real time drive status.
If the display shows “
Adr-01
”, the keypad didn’t find a drive with address 1 in the network. Use the UP and DOWN buttons
to select the correct address from 1 to 63. Once the address has been changed to a correct value, press STOP to initiate
search again.
5.3.5 Connection to a network of multiple drives
Selection of the drive address can be changed at any time. Press STOP and DOWN buttons together and message
“
Adr
-XX
” is displayed. Use UP or DOWN buttons to select the desired drive address. Select the new address and press
STOP and DOWN button together to establish communications with the new drive address.
5.3.6 To setup the REMOTE PANEL device number
A maximum of (2) REMOTE PANELs can be used on the same drive network. To use (2) keypads on one drive, change the
Device Number on the second panel from the default value of 1 for correct operation. To change Device Number, press
NAVIGATE, STOP and DOWN buttons together. “
Port
-X
” (x = 1 or 2) will be displayed. Use UP or DOWN and change
the Device Number to 1 or 2 as required. Press NAVIGATE, STOP and DOWN button together again to return to normal
operation.
NOTE: An REMOTE PANEL with Device Number 1 must always be present for the network to function correctly.
Change the Device Address to 2 only if multiple keypads are connected.
5.4 Control Signals
5.4.1 Analog Output
The analog output function may be configured using parameter 1501, which is described in Chapter 10 Parameter
Definitions. The output has two operating modes, dependent on the parameter selection.
Analog Mode
The output is a 0 – 10 Volt DC signal, 20mA max load current
Digital Mode
The output is 24 Volt DC, 20mA max load current
5.4.2 Relay Output
The relay output function may be configured using parameter 1401, see Chapter 10 Parameter Definitions.
5.4.3 Analog Inputs
Two analog inputs are available, which may also be used as Digital Inputs if required. The signal formats are selected by
parameters as follows:
Analog Input 1 Format Selection Parameter 1300
Analog Input 2 Format Selection Parameter 1304
These parameters are described more fully in Chapter 10 Parameter Definitions.
The function of the analog input, for example for speed reference or PID feedback is defined by parameters 1103 Primary
Command Source and 9902 Digital Input Function Select. The function of these parameters and available options are
described in section the Macro Function Guide.
5.4.4 Digital Inputs
Up to four digital inputs are available. The function of each input is defined by parameters 1103 and 9902, which are
explained in Chapter 9 Control Modes.
Summary of Contents for EC Titanium ECS100A1H1DF4
Page 1: ... MN448_May 2020 May 2020 EC Titanium Manual User s guide ...
Page 10: ...1 4 Introduction MN448 ...
Page 20: ...3 4 Mechanical Information and Mounting MN448 ...
Page 26: ...4 6 Electrical Installation and Planning MN448 ...
Page 32: ...5 6 Control Pad Wiring and Keypad Interface MN448 ...
Page 36: ...6 4 Keypad Programming and Basic Operation MN448 ...
Page 44: ...8 4 Parameter Navigation and Groups MN448 ...
Page 51: ...9 7 Control Modes MN448 ...
Page 77: ...11 8 Standalone Motor and ABB Drive Setup MN448 ...
Page 99: ...A 12 Modbus RTU Example Connection MN448 ...
Page 102: ......