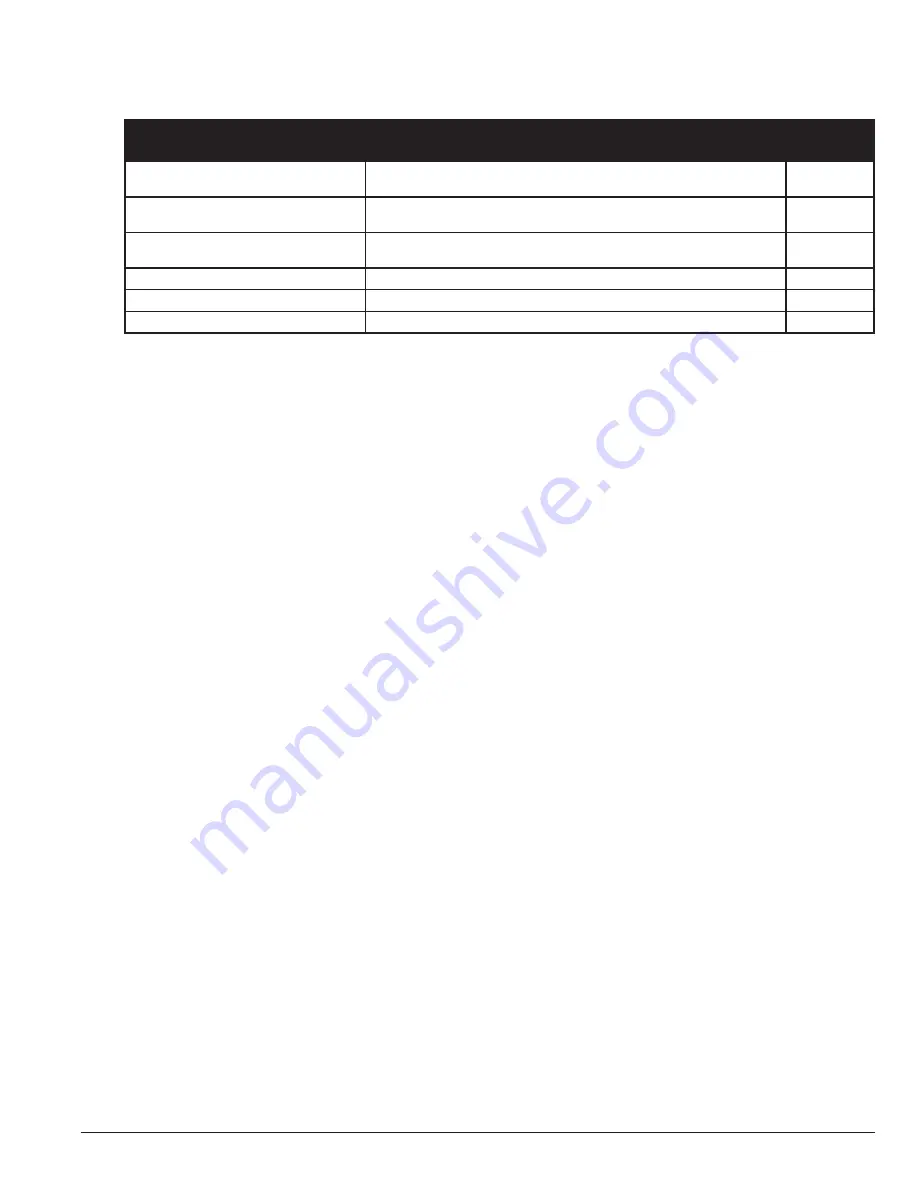
Parameter Definitions 10-17
MN448
Parameters in the Long parameter mode
Index
Name/Selection
Description
Default
11201
MOTOR STATOR
RESISTANCE (Rs)
Motor Stator Resistance – refer to motor nameplate for value.
-
11203
MOTOR STATOR
INDUCTANCE (Lsd)
Ld (mH) Motor Inductance (Lsd) value – refer to motor nameplate
for value.
-
11206
MOTOR STATOR q-axis
INDUCTANCE (Lsq)
Lq (mH) Motor q-axis Inductance (Lsq) value – refer to motor
nameplate for value.
-
96102
BLUETOOTH ENABLE
Turns the on-board Bluetooth On/Off
0
0: Enabled
On-Board Bluetooth On
1: Disabled
On-Board Bluetooth Off
Summary of Contents for EC Titanium ECS100A1H1DF4
Page 1: ... MN448_May 2020 May 2020 EC Titanium Manual User s guide ...
Page 10: ...1 4 Introduction MN448 ...
Page 20: ...3 4 Mechanical Information and Mounting MN448 ...
Page 26: ...4 6 Electrical Installation and Planning MN448 ...
Page 32: ...5 6 Control Pad Wiring and Keypad Interface MN448 ...
Page 36: ...6 4 Keypad Programming and Basic Operation MN448 ...
Page 44: ...8 4 Parameter Navigation and Groups MN448 ...
Page 51: ...9 7 Control Modes MN448 ...
Page 77: ...11 8 Standalone Motor and ABB Drive Setup MN448 ...
Page 99: ...A 12 Modbus RTU Example Connection MN448 ...
Page 102: ......