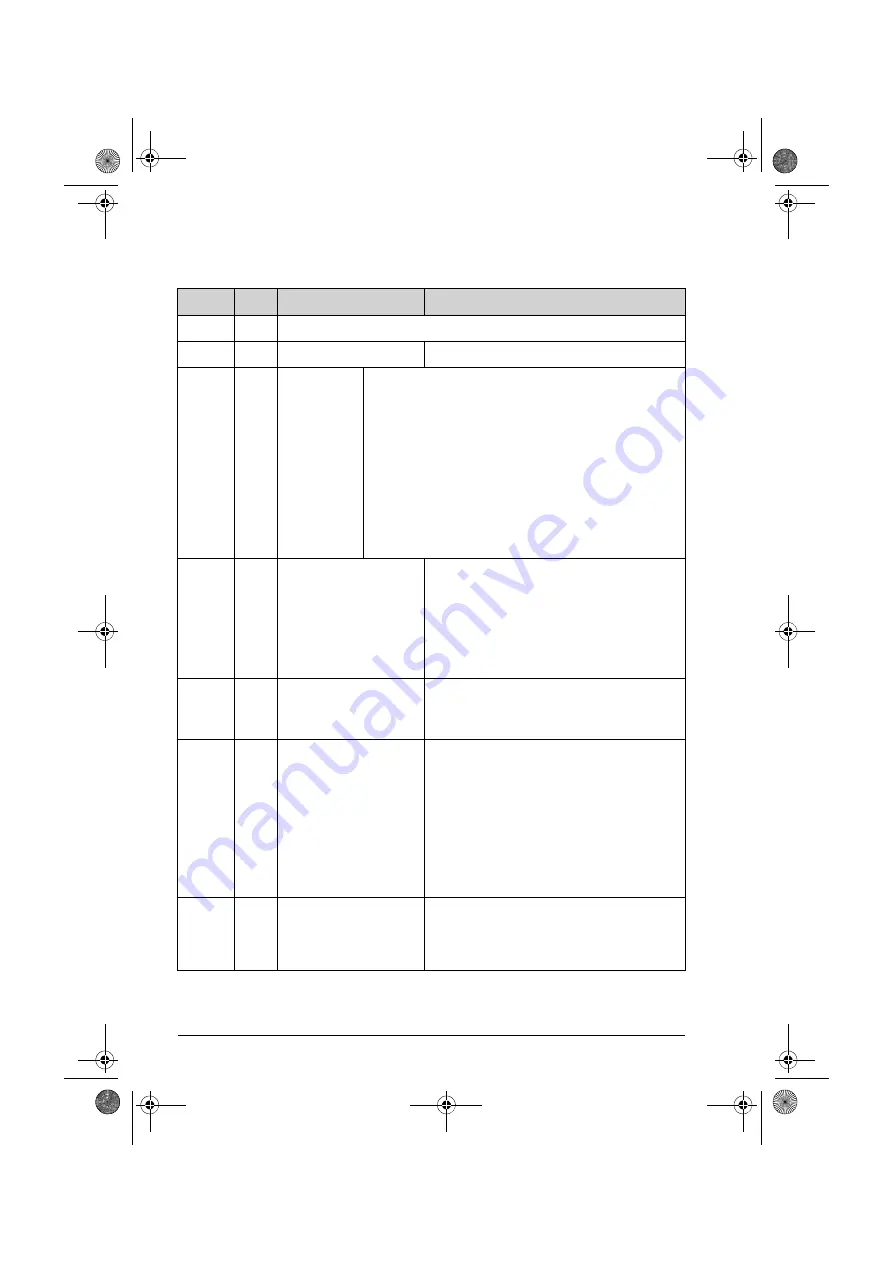
72 Fault tracing
Fault Code Messages
Fault
Code
No.
Description
Corrective Action
Stop
0x00
Drive is READY and in a stopped condition. The motor is not energized. No enable
signal is present to start the drive
P-def
0X0A
Factory Default parameters
have been loaded
Press the STOP key, drive is ready to configure for
particular application
F0001
0x03
Instantaneous
Over current
on the drive
output.
Excess load or
shock load on
the motor.
Fault occurs immediately on drive enable or run command
Check the output wiring connections to the motor and the motor
for short circuits phase to phase and phase to earth.
Fault occurs during motor starting
Check the motor is free to rotate and there are no mechanical
blockages. If the motor has a brake fitted, check the brake is
releasing correctly. Check for correct star-delta motor wiring.
Ensure the motor nameplate current is correctly entered in
parameter
9906
.
Increase acceleration time in parameter
2202
.
Reduce motor boost voltage setting in parameter
2603
Fault occurs when motor operating at constant speed
Investigate overload.
Fault occurs during motor acceleration or deceleration
The accel/decel times are too short requiring too much power. If
parameter
2202
or
2203
cannot be increased, a bigger drive may
be required
F0009
0x04
Motor thermal overload
protection trip. The drive
has tripped after delivering
>100% of value in
9906
for
a period of time to prevent
damage to the motor.
Ensure the correct motor nameplate current value is
entered in parameter
9906
. Check for correct Star or
Delta wiring configuration. Check to see when the
decimal points are flashing (which indicates the
output current > parameter
9906
value) and either
increase acceleration ramp (parameter
2202
) or
decrease motor load. Check the total motor cable
length is within the drive specification. Check the
load mechanically to ensure it is free, and that no
jams, blockages or other mechanical faults exist
OI-b
0x01
Brake channel over current
(excessive current in the
brake resistor)
Check the cabling to the brake resistor and the brake
resistor for short circuits or damage. Ensure the
resistance of the brake resistor is equal to or greater
than the minimum value for the relevant drive shown
in the table in section
OL-br
0x02
Brake resistor thermal
overload. The drive has
tripped to prevent damage
to the brake resistor
Only occurs if parameter
2020
= 1. The internal
software protection for the brake resistor has
activated to prevent damage to the brake resistor.
Increase the deceleration time (parameter
2203
) or
2
nd
deceleration time (parameter
2206
). Reduce the
load inertia
For Other Brake Resistors
Ensure the resistance of the brake resistor is equal to
or greater than the minimum value for the relevant
drive shown in the table in section
. Use an external thermal protection device for the
brake resistor. In this case, parameter
2020
may be
set to 2
F0004
ECT
Hardware Over Current
Check the wiring to motor and the motor for phase to
phase and phase to earth short circuits. Disconnect
the motor and motor cable and retest. If the drive
trips with no motor connected, it must be replaced
and the system fully checked and retested before a
replacement unit is installed.
ACS260-04.book Page 72 Thursday, December 24, 2020 4:33 PM
Summary of Contents for ACS260-04 Series
Page 2: ...ACS260 04 book Page 2 Thursday December 24 2020 4 33 PM ...
Page 4: ...ACS260 04 book Page 4 Thursday December 24 2020 4 33 PM ...
Page 8: ...8 Table of contents ACS260 04 book Page 8 Thursday December 24 2020 4 33 PM ...
Page 14: ...14 Safety ACS260 04 book Page 14 Thursday December 24 2020 4 33 PM ...
Page 22: ...22 Mechanical installation ACS260 04 book Page 22 Thursday December 24 2020 4 33 PM ...
Page 32: ...32 Electrical installation ACS260 04 book Page 32 Thursday December 24 2020 4 33 PM ...
Page 92: ...92 Technical Data ACS260 04 book Page 92 Thursday December 24 2020 4 33 PM ...
Page 96: ...96 Options and Kits ACS260 04 book Page 96 Thursday December 24 2020 4 33 PM ...