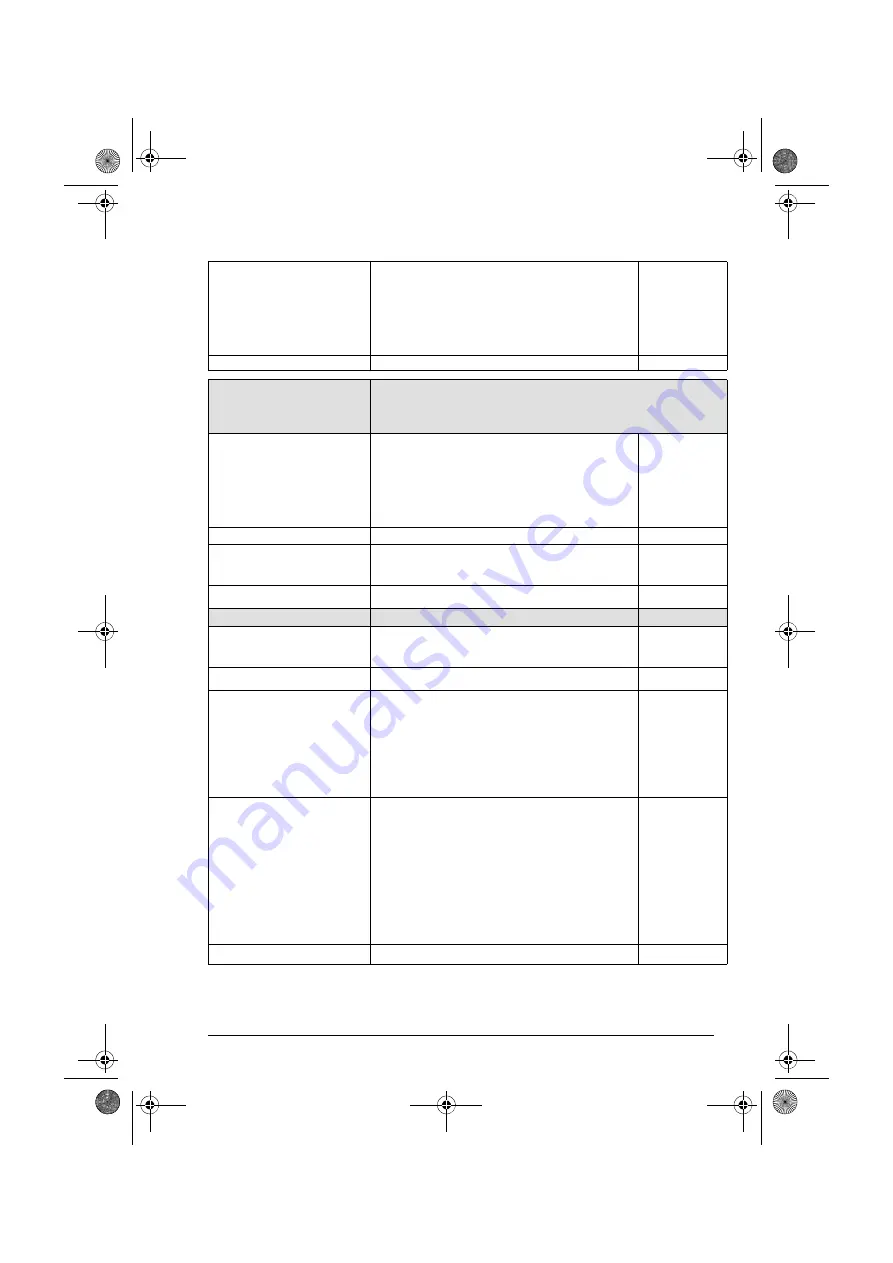
Parameters 59
2206
2nd
DECELERATION
RAMP TIME (FAST
STOP)
This parameter allows an alternative deceleration
ramp down time to be programmed into the DRIVE,
which can be selected by digital inputs (dependent on
the setting of Parameter
9902
DIGITAL INPUTS
FUNCTION SELECT or selected automatically in the
case of a mains power loss if parameter
2102
STOP
MODE = 2.
0.00
0.00…600 s
When set to 0.00, the drive will coast to stop.
25 CRITICAL SPEEDS
Speed bands with which the drive is not allowed to operate.
The Skip Frequency function is used to avoid the DRIVE operating at a
certain output frequency, for example at a frequency which causes
mechanical resonance in a particular machine.
2500
SKIP FREQUENCY
HYSTERESIS
BAND
The drive output frequency will ramp through the
defined band at the rates set in parameter
2202
and
2203
respectively and will not hold any output
frequency within the defined band. If the frequency
reference applied to the drive is within the band, the
drive output frequency will remain at the upper or
lower limit of the band.
0.0 Hz/Rpm
0.0…
2008
2501
SKIP FREQUENCY
Defines the center point of the skip frequency band,
and is used conjunction with parameter
2500
SKIP
FREQUENCY HYSTERESIS BAND
0.0Hz
0.0…
2008
26 MOTOR CONTROL
Motor control variables
2601
ENERGY
OPTIMIZER
Only active when enhanced V/F motor control mode is
selected (parameter
9903
MOTOR CONTROL MODE
= 2)
1 : Enabled
0 : DISABLED
1 : ENABLED
The Energy Optimizer attempts to reduce the overall
energy consumed by the drive and motor when
operating at constant speeds and light loads. The
output voltage applied to the motor is reduced. The
Energy Optimizer is intended for applications where
the drive may operate for some periods of time with
constant speed and light motor load, whether constant
or variable torque.
2603
V/F MODE
VOLTAGE BOOST
Voltage boost is used to increase the applied motor
voltage at low output frequencies, in order to improve
low speed and starting torque. Excessive voltage
boost levels may result in increased motor current and
temperature, and force ventilation of the motor may be
required.
A suitable setting can usually be found by operating
the motor under low load or no load conditions at
approximately 5Hz, and adjusting parameter
2603
until the motor current is no more than 80% of the
rated full load current.
3.0 %
0.0…25.0 %
ACS260-04.book Page 59 Thursday, December 24, 2020 4:33 PM
Summary of Contents for ACS260-04 Series
Page 2: ...ACS260 04 book Page 2 Thursday December 24 2020 4 33 PM ...
Page 4: ...ACS260 04 book Page 4 Thursday December 24 2020 4 33 PM ...
Page 8: ...8 Table of contents ACS260 04 book Page 8 Thursday December 24 2020 4 33 PM ...
Page 14: ...14 Safety ACS260 04 book Page 14 Thursday December 24 2020 4 33 PM ...
Page 22: ...22 Mechanical installation ACS260 04 book Page 22 Thursday December 24 2020 4 33 PM ...
Page 32: ...32 Electrical installation ACS260 04 book Page 32 Thursday December 24 2020 4 33 PM ...
Page 92: ...92 Technical Data ACS260 04 book Page 92 Thursday December 24 2020 4 33 PM ...
Page 96: ...96 Options and Kits ACS260 04 book Page 96 Thursday December 24 2020 4 33 PM ...