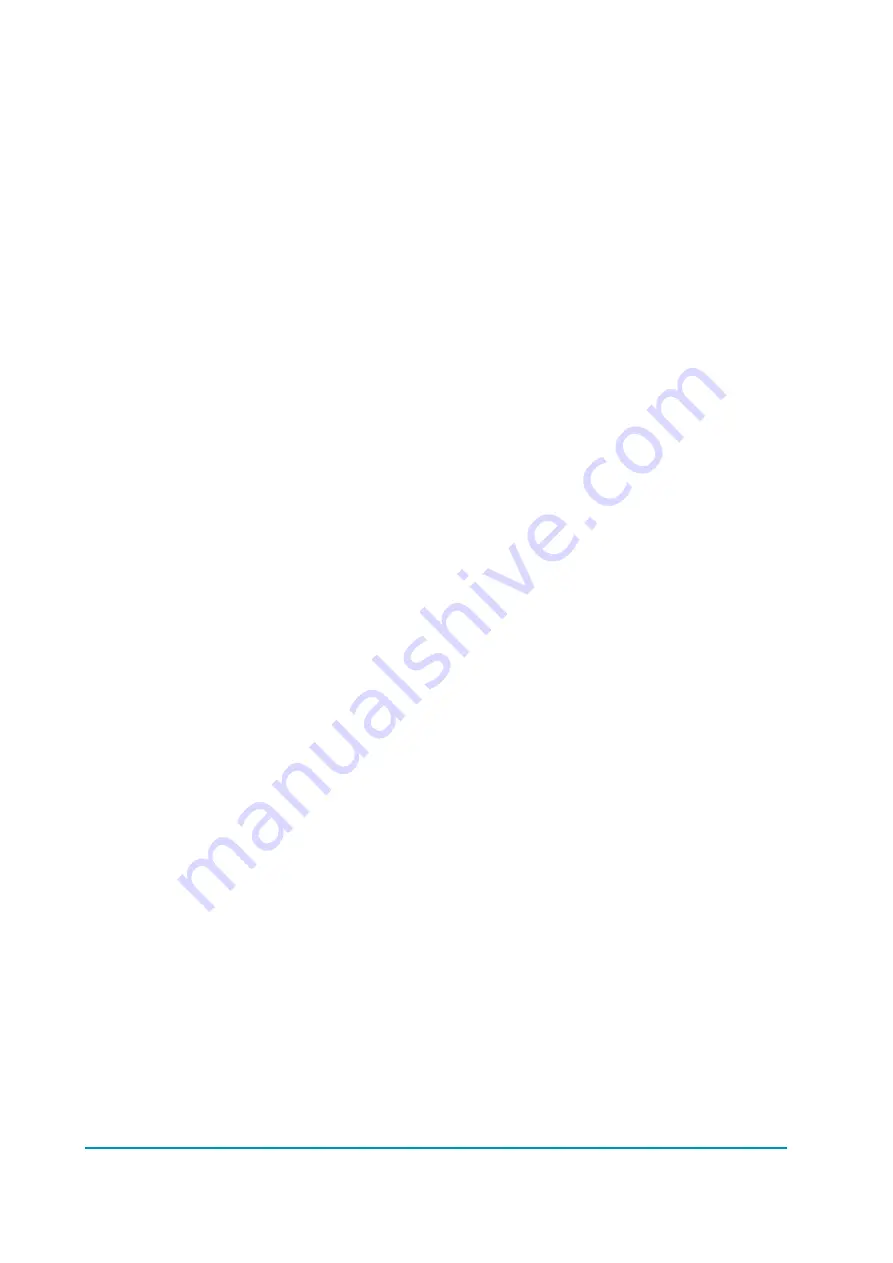
Page - 86/95
AEMZP0BA - EPS-AC0 - User Manual
- Cause:
This alarm occurs if the slave uC detects the safety contact, of the
main uC, open when expected being closed.
- Remedy:
It is necessary to replace the controller.
11) KS CLOSED
CAN Bus Code = 254
- Cause:
This alarm occurs if the main uC detects the safety contact, of the
slave uC, closed prior to be commanded.
- Remedy:
This alarm occurs if the connection CNA#4 (NK1) is around a
voltage of 12 Vdc when switching on the key. In fact, when the
safety contacts are open, NK1 is expected being connected to a
minus battery voltage (not 12 V). Search for a harness problem or
replace the controller.
12) KS OPEN
CAN Bus Code = 252
- Cause:
This alarm occurs if the main uC detects the safety contact, of the
slave uC, open when expected being closed.
- Remedy:
It is necessary to replace the controller.
13) CLOCK PAL NOT OK
CAN Bus Code = 218
- Cause:
The main uC sends an analog signal towards the slave uC to reset
the slave uC on demand. When the slave uC detects this analog
signal external to a window from 2.2 to 2.8 and not in the range to
generate the reset on demand, the slave uC raises this alarm.
- Remedy:
It is necessary to replace the controller.
14.1.2 Two Blinks Alarms
1) HIGH
CURRENT
CAN Bus Code = 70
- Cause:
This alarm occurs if the circuit to limit via hardware the current in
the motor is either always active at key-on or repeatedly active
when the motor is turning.
- Remedy:
Check the motor is suited to work with the eps-ac0 (not oversized).
Otherwise it is necessary to replace the controller.
2) POWER FAILURE #1
CAN Bus Code = 73
- Cause:
This alarm occurs when the current in the phase W of the motor is
zero and the motor is commanded for moving.
- Remedy:
Check the power fuse is OK. Check the battery positive arrives to
the controller. Check the continuity of the wire in the phase W of
the motor. Otherwise it is necessary to replace the controller.
3) POWER FAILURE #2
CAN Bus Code = 72
- Cause:
This alarm occurs when the current in the phase U of the motor is
zero and the motor is commanded for moving.
- Remedy:
Check the power fuse is OK. Check the battery positive arrives to
the controller. Check the continuity of the wire in the phase U of
the motor. Otherwise it is necessary to replace the controller.
Содержание EPS-AC0
Страница 23: ...AEMZP0BA EPS AC0 User Manual Page 23 95 6 2 EPS AC0 Stepper Motor diagram Figure 6 2...
Страница 24: ...Page 24 95 AEMZP0BA EPS AC0 User Manual 6 3 EPS AC0 Twin pot diagram Figure 6 3...
Страница 54: ...Page 54 95 AEMZP0BA EPS AC0 User Manual 12 3 1 Stepper motor with Encoder and Feedback pot Figure 12 2...
Страница 55: ...AEMZP0BA EPS AC0 User Manual Page 55 95 12 3 2 RTC with Encoder and Feedback pot Figure 12 3...
Страница 56: ...Page 56 95 AEMZP0BA EPS AC0 User Manual 12 3 3 Stepper motor with Encoder and Toggle switch es Figure 12 4...