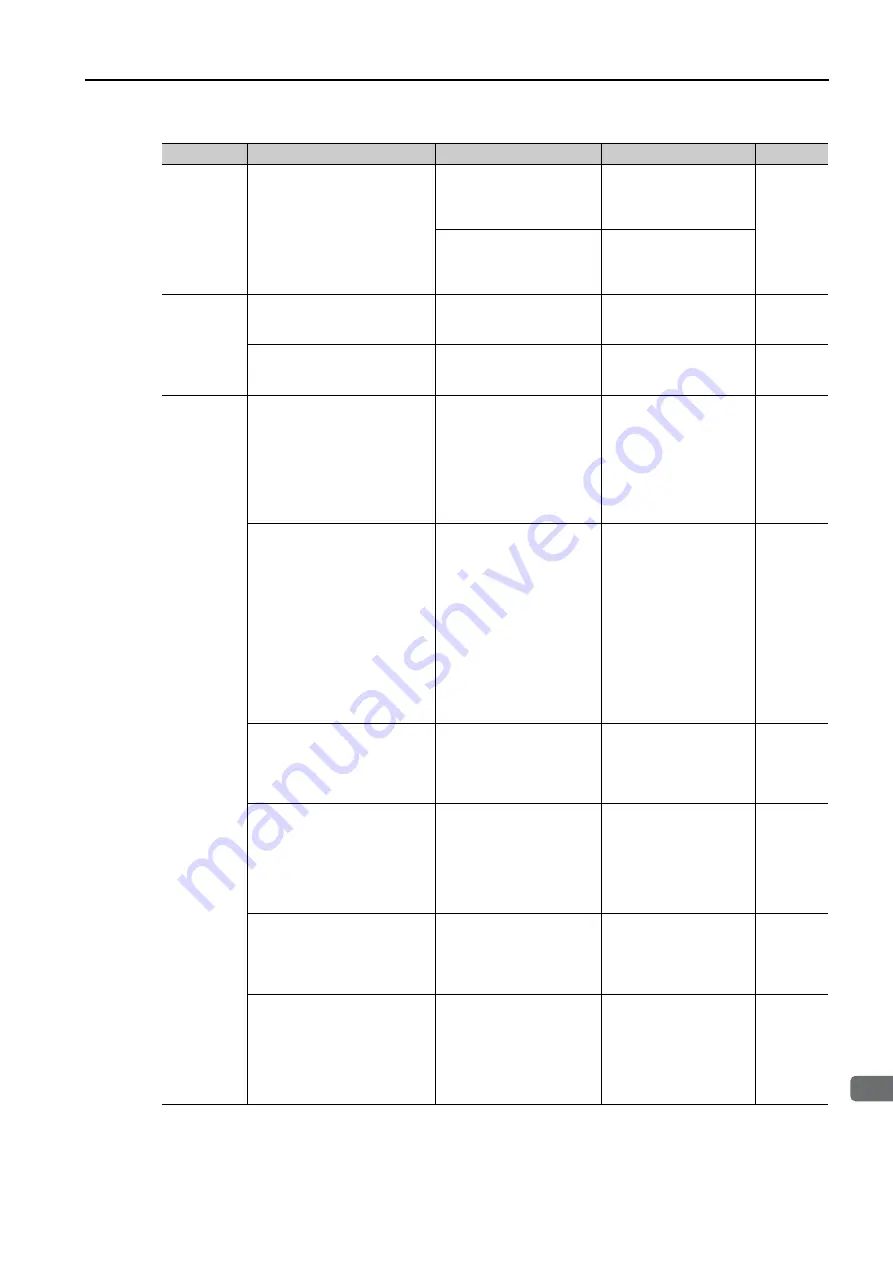
12.5 Troubleshooting Based on the Operation and Conditions of the Servomotor
12-67
12
Maintenance
Overtravel
Occurred
The selection of the Servo-
motor stopping method is
not correct.
Check the servo OFF
stopping method set in
Pn001 = n.
X or
Pn001 = n.
X
.
Select a Servomotor
stopping method other
than coasting to a stop.
Check the torque control
stopping method set in
Pn001 = n.
X or
Pn001 = n.
X
.
Select a Servomotor
stopping method other
than coasting to a stop.
Improper
Stop Posi-
tion for
Overtravel
(OT) Signal
The limit switch position and
dog length are not appropri-
ate.
–
Install the limit switch at
the appropriate posi-
tion.
–
The overtravel limit switch
position is too close for the
coasting distance.
–
Install the overtravel
limit switch at the
appropriate position.
–
Position
Deviation
(without
Alarm)
Noise interference occurred
because of incorrect Encoder
Cable specifications.
Check the Encoder Cable
to see if it satisfies speci-
fications. Use shielded
twisted-pair cables or
screened twisted-pair
cables with conductors of
at least 0.12 mm
2
(stranded wire).
Use cables that satisfy
the specifications.
–
Noise interference occurred
because the Encoder Cable
is too long.
Turn OFF the power sup-
ply to the servo system.
Check the length of the
Encoder Cable.
•
Rotary Servomotors:
The Encoder Cable
length must be 50 m
max.
•
Linear Servomotors:
Make sure that the
Serial Converter Unit
cable is no longer
than 20 m and that
the Linear Encoder
Cable and the Sensor
Cable are no longer
than 15 m each.
–
Noise interference occurred
because the Encoder Cable
is damaged.
Turn OFF the power sup-
ply to the servo system.
Check the Encoder Cable
to see if it is pinched or
the sheath is damaged.
Replace the Encoder
Cable and correct the
cable installation envi-
ronment.
–
The Encoder Cable was sub-
jected to excessive noise
interference.
Turn OFF the power sup-
ply to the servo system.
Check to see if the
Encoder Cable is bundled
with a high-current line or
installed near a high-cur-
rent line.
Correct the cable lay-
out so that no surge is
applied by high-current
lines.
–
There is variation in the FG
potential because of the
influence of machines on the
Servomotor side, such as a
welder.
Turn OFF the power sup-
ply to the servo system.
Check to see if the
machines are correctly
grounded.
Properly ground the
machines to separate
them from the FG of
the encoder.
–
There is a SERVOPACK
pulse counting error due to
noise.
Turn OFF the power sup-
ply to the servo system.
Check to see if there is
noise interference on the
I/O signal line from the
encoder or Serial Con-
verter Unit.
Implement counter-
measures against noise
for the encoder wiring
or Serial Converter Unit
wiring.
–
Continued on next page.
Continued from previous page.
Problem
Possible Cause
Confirmation
Correction
Reference