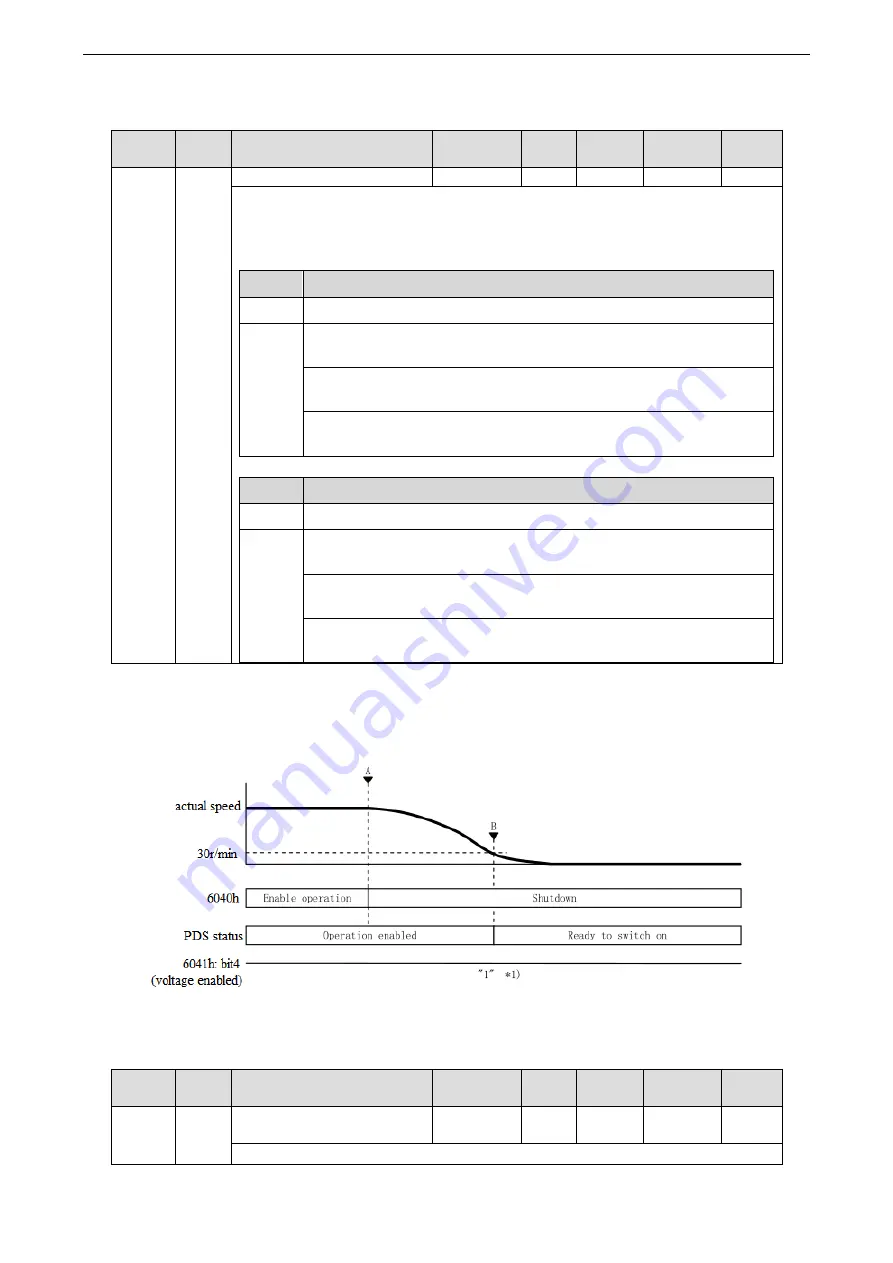
71
2.
Shutdown option code (605Bh)
The motor stop mode when receiving PDS command
「
Shutdown
」
,
「
Disable voltage
」
.
Index
Sub-
Index
Name/Description
Range
Date
Type
Access
PDO
Op-
mode
605Bh
00h
Shutdown option code
0-1
I16
rw
NO
All
Set the time sequence of
「
Shutdown
」
,
「
Disable voltage
」
. It is different according to
the definition of control mode.
The setting is prohibited except the following values.
(1)
PDS command
「
Shutdown
」
is receiving
Value
Definition
0
Stop at once, PDS state migrates to Ready to switch on.
1
The control mode is PP, PV: motor stop through 0x6084 (Profile
deceleration), PDS state migrates to Ready to switch on.
The control mode is HM: motor stop through 0x609Ah (Homing
acceleration), PDS state migrates to Ready to switch on.
The control mode is TQ: motor stop through 0x6087 (Torque Slope),
PDS state migrates to Ready to switch on.
(2)
PDS command
「
Disable voltage
」
is receiving.
Value
Definition
0
Stop at once, PDS state migrates to Switch on disabled.
1
The control mode is PP, PV: motor stop through 0x6084 (Profile
deceleration), PDS state migrates to Switch on disabled.
The control mode is HM: motor stop through 0x609Ah (Homing
acceleration), PDS state migrates to Switch on disabled.
The control mode is TQ: motor stop through 0x6087 (Torque Slope),
PDS state migrates to Switch on disabled.
Examples of deceleration stop action according to the shutdown command:
If the PDS command "shutdown" is received, it will start to decelerate and stop.
PDS status during deceleration remains Operation enabled.
The PDS status after stop is Ready to switch on.
*1) 6041h: bit4(Statusword: voltage enabled) is still 1, not changed.
3.
Disable operation option code (605Ch)
Set the motor deceleration stop mode when receiving PDS command
「
Disable operation
」
.
Index
Sub-
Index
Name/Description
Range
Date
Type
Access
PDO
Op-
mode
605Ch
00h
Disable
operation
option
code
0-1
I16
rw
NO
All
Set the time sequence of
「
Disable operation
」
. It is different according to the
Содержание DF3E Series
Страница 1: ... 1 DF3E series servo driver User manual Wuxi Xinje Electric Co Ltd Data No SF3 01 20210607 1 0 ...
Страница 23: ...15 Fixed installation Bending radius 5 D 5 D Note D represents the finished product cable diameter ...
Страница 121: ...113 2 select jog setting or manual setting to configure the inertia estimation trip 3 Set the auto tuning interface ...
Страница 126: ...118 4 click ok to estimate the inertia 5 set the auto tuning parameters ...
Страница 128: ...120 7 Wait for the end of the auto tuning ...
Страница 132: ...124 8 The upper device starts to send pulses wait the completion of auto tuning 9 Auto tuning is finished click ok ...
Страница 184: ...176 Appendix 8 Torque speed characteristic curve ...