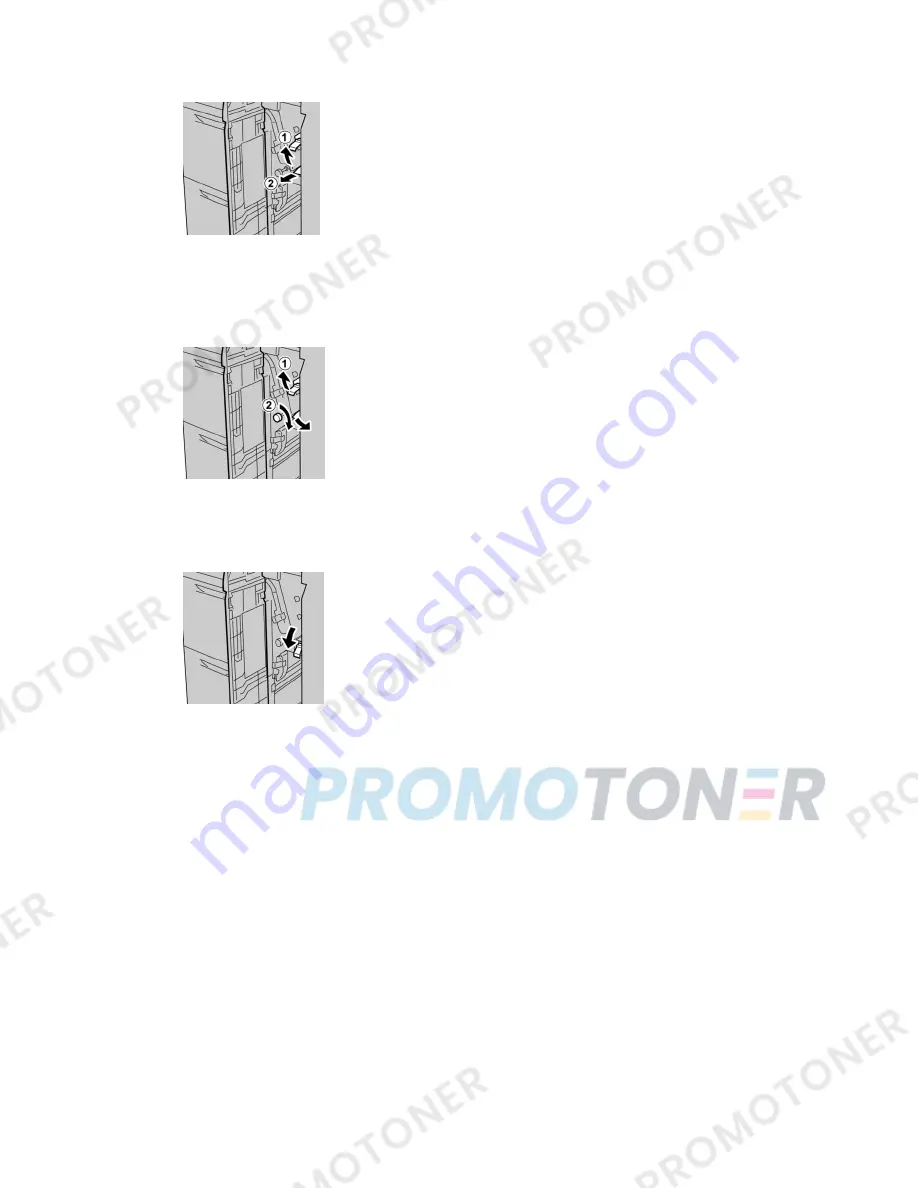
2. Move the lever 1d upward and remove the jammed paper.
Note
If paper is torn, check inside the machine and remove it.
3. If the paper cannot be removed, turn the knob 1c clockwise, and then remove the
jammed paper.
Note
If paper is torn, check inside the machine and remove it.
4. Return the lever 1d to the original position.
5. Close the front cover of the feeder module.
Note
If the front cover of the feeder module is not completely closed, a message will appear
and the machine will not operate.
Fault Information
The following occurs when there is an fault, such as paper jams, open doors or covers,
or a press malfunction:
• The press stops running and an fault message displays on the press touch screen.
• The message includes a graphical illustration showing the location of the fault along
with a brief explanation of corrective actions for clearing the fault.
7-43
Xerox
®
Versant
®
3100 Press
User Guide
Troubleshooting
Содержание Versant 3100 Press
Страница 1: ...Xerox Versant 3100 Press User Guide Book Version 1 0 February 2017 702P04567...
Страница 8: ...Xerox Versant 3100 Press vi User Guide Table of Contents...
Страница 30: ...Xerox Versant 3100 Press 3 6 User Guide Print Job Submission...
Страница 38: ...Xerox Versant 3100 Press 4 8 User Guide Job Machine Status...
Страница 118: ...Xerox Versant 3100 Press 6 42 User Guide Maintenance...
Страница 166: ...Xerox Versant 3100 Press 7 48 User Guide Troubleshooting...
Страница 169: ......
Страница 170: ......