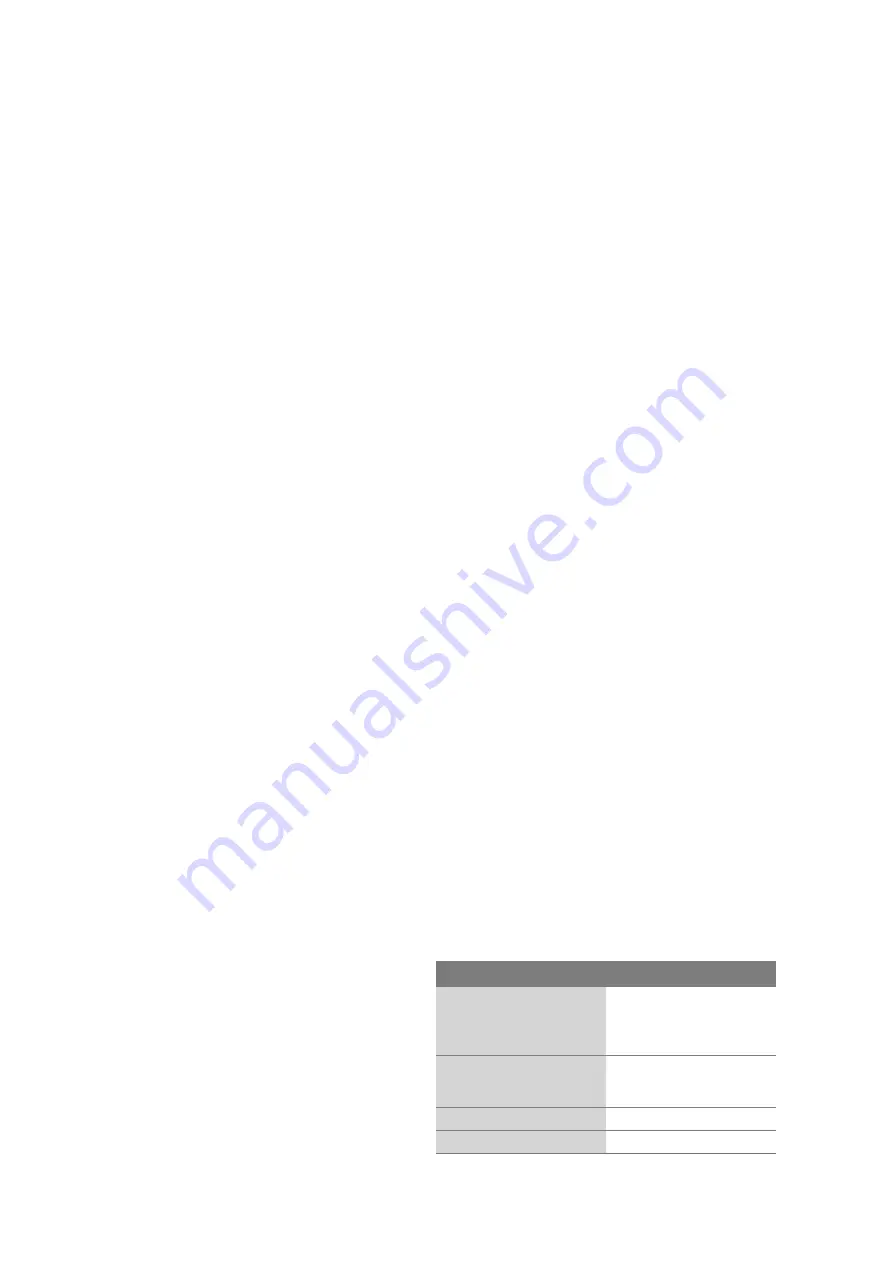
English
PRODUCT DESCRIPTION
38
WILO SE 11-2016 V06 DIN A4
3.2.4. Safety and monitoring equipment
The sewage lifting unit is equipped with the fol-
lowing safety and monitoring devices:
• Safety device
•
Overflow
The lifting unit is directly connected to the
collection reservoir by an overflow in the supply
box/distributor. In the event of flooding, the
water is channelled directly through this into
the collection reservoir after filtration.
• Monitoring devices
• Thermal motor monitoring
The thermal motor monitoring protects the
motor windings against overheating. Bimetallic
strips are used for this as standard. Deactivation
must take place when the maximum winding
temperature is reached.
• Leakage detection motor compartment
The motor compartment monitor signals water
ingress into the motor compartment. Deactiva-
tion must take place.
3.2.5. Materials
•
Collection reservoir: PE
•
Solids separation reservoir: PE
•
Supply box/distributor: PUR
•
Pipework: PE
•
Pumps: Cast iron
•
Gate valve: Cast iron
•
Pressure connection:
•
Variant A: PE with T-merge
•
Variant B: Stainless steel with Y-merge
3.2.6. Switchgear
The switchgear must be provided by the custom-
er! The necessary functions for the control of a
lifting unit with solids separation system must be
provided.
Additional information can be found in the chap-
ter “Minimum requirements for the switchgear”
on page 44 or contact Wilo customer service
with any questions you may have.
3.2.7. Versions
The lifting unit is available in the following ver-
sions:
• Version “A” as standard version with pressure
connection as pipe connection
without
flange
• Version “B” as comfort version with automatic
backwashing, pressure connection with flange
connection, transparent cover on the supply box/
distributor and sealing chamber control of the
sewage pump.
3.3. Operating principle
The sewage flows through the inlet pipe into the
supply box/distributor and from there into one of
the two solids separation reservoirs. The solids
separation reservoirs are aligned upstream of the
discharge ports of the sewage pumps and “filter
out” “non-permitted” large solid materials.
This way, only “pre-cleaned sewage” passes
through the idle sewage pump into the shared
collection reservoir. When the “Pump ON” water
level in the collection reservoir is reached, the
pumping procedure of the respective sewage
pump is initiated by the level control device.
The sewage pumps run alternately, parallel
operation is not permitted!
The volume flow of the working sewage pump
opens the separation system of the solids separa-
tion reservoir and, due to the flow rate, pumps all
of the solid materials held back in the solids sepa-
ration reservoir into the outgoing pressure pipe.
The affected solids separation reservoir is closed
with a shut-off ball on the intake side during this
procedure.
3.4. Ex protection
The sewage lifting unit has a closed collection
reservoir with dry-mounted pumps. There is
therefore no potentially explosive area present.
An explosive atmosphere may obtain within the
reservoir due to the accumulation of sewage in
the collection reservoir.
Ex Zone 2 is in effect within a radius of 1 m
around the ventilation pipe!
In order to prevent explosive atmospheres during
maintenance work as well, equipment must be
installed in the operating space to enable the air
there to be replaced eight times per hour.
3.4.1.
Overflow of the lifting unit
The lifting unit is overflow-proof, and can contin
-
ue to be operated even in a disaster situation.
The electrical connections must be installed
accordingly to ensure that they are over-
flow-proof!
3.5. Operating modes
3.5.1.
Operating mode S1 (continuous duty)
The pump can operate continuously at the rated
load without exceeding the permissible temper-
ature.
3.5.2.
Operating mode S3 (intermittent periodic duty)
This operating mode involves the maximum ratio
between operating time and downtime:
S3 50 %
operating time 5 min / downtime 5 min
3.6. Technical data
Approved field of application
Max. inlet:
CORE 20.2: 20 m³/h
CORE 45.2: 45 m³/h
CORE 50.2: 50 m³/h
CORE 60.2: 60 m³/h
Max. permitted pressure
in the system discharge
pipeline:
6 bar
Max. delivery head [H]:
See rating plate
Maximum volume flow [Q]:
See rating plate
Содержание EMUport CORE
Страница 3: ...Fig 2 Fig 3 1 1 1 2 2 2 2 2 1...
Страница 4: ...Fig 6 A CORE A Motor P 13 Fig 5 Fig 4 2 1 1 5 1 2 4 3 M 3 gn ye W V 21 20 U PE 6 DK...
Страница 7: ...Fig 12 Fig 11 Fig 10 3 3 2 1 4 3 1 2 4 2 1 3 5 Fig 9 3 1 2...
Страница 8: ...Fig 13 Motor P 13 P 17 Fig 13 Motor FK 17 1 Fig 13 Motor FK 17 1 D M D...