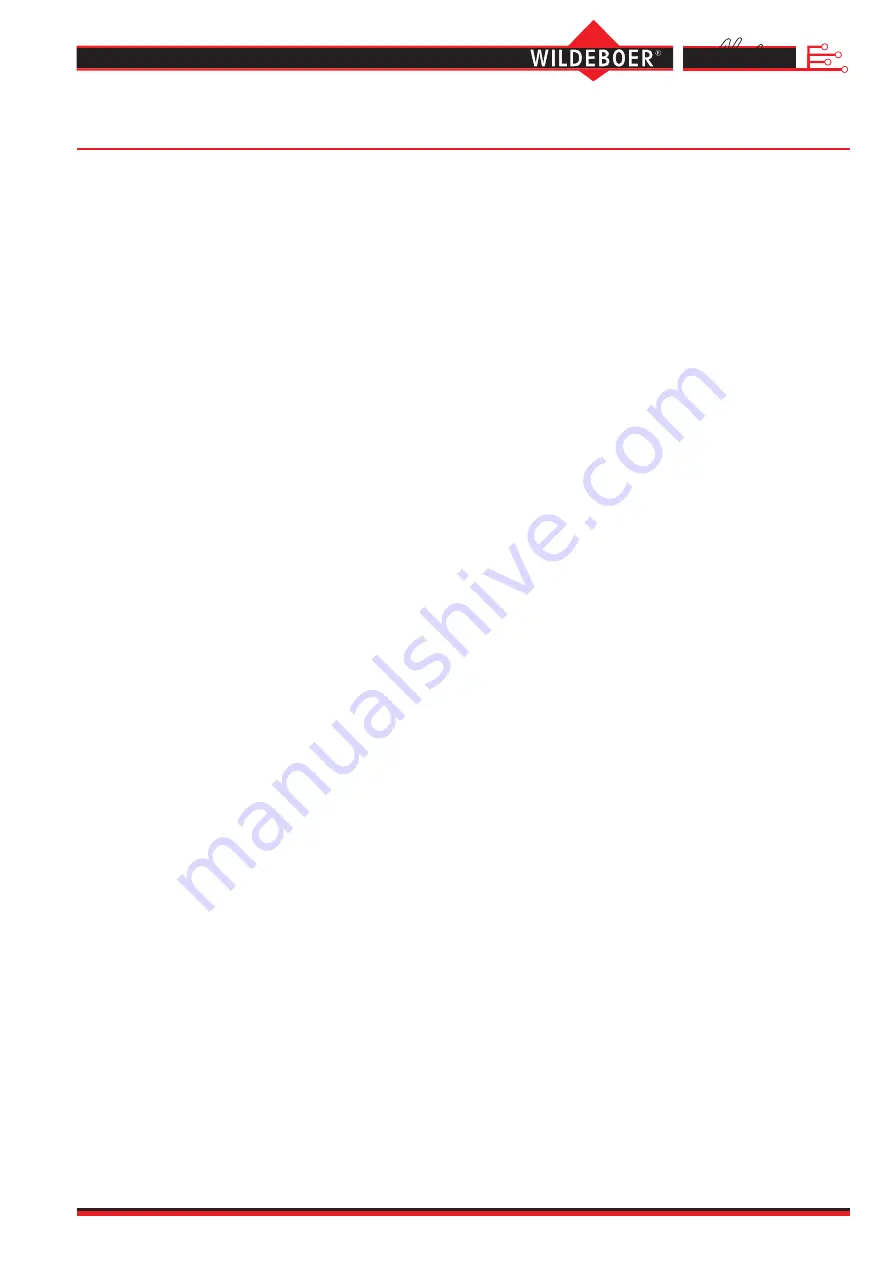
Net
User Manual 7.1 (2019-04) 7
Subject to change
Wildeboer-Net
Commissioning
A unique address for each field module is required within Wildeboer-Net for data communication. The type of field
module (motor module, I/O module etc.) also has to be defined within the system. The detection and addressing of all
connected field modules is performed automatically by the Wildeboer-Net software and takes just a few minutes. All
addresses are managed automatically in the event of expansions and reductions. Thanks to the galvanically isolated
construction of all subnets, partial commissioning is also possible whilst further partial segments or subnets have not
yet been fully installed. Faults when installing the bus lines or modules can be localised easily.
An essential step when commissioning a system is the proper documentation and inspection of the orderly connec-
tion of field devices to the field modules. In Wildeboer-Net a "1-to-1 test" can be carried out using pinging with the
Wildeboer-Net software for fire dampers for this purpose.
In pinging mode the Wildeboer-Net software detects any fault messages from the field devices which arise, and saves
them to a list (ping list) in the order of occurrence. The faults must be generated deliberately in order to carry out the
test. If fire dampers are connected, the fusible link can be pulled off or the test button on the motor can be actuated
to trigger the desired fault message. The fire dampers must be in the OPEN position for this purpose.
To carry out pinging, it is necessary to inspect the system. During the inspection, the installation location and the
equipment identification marking on the field device according to the general identification system (GIS) are noted.
This data can subsequently be transferred to the established ping list in the Wildeboer-Net software, and from there
it can be added to the comments list automatically.
⇒
see page 8
Note:
•
At the time of pinging no parametrised release groups must have been transferred, as all the fire dampers in the
group will otherwise be closed.
•
The structure of the Wildeboer-Net system is monitored cyclically. Deviations are detected. That means that field
modules which have already been addressed cannot simply be expanded or re-installed in the bus in another posi-
tion. However, modules can be replaced simply using the Wildeboer-Net software thanks to an assistant.
On completion of commissioning, the system is ready for use and parametrisation of the functions can be started.
Functions
•
Comment function
⇒
see page 8
•
Fan enabling
⇒
see page 9
•
Functional checks
⇒
see page 10
•
Manual fan shut-off for functional checks
⇒
see page 11
•
Release group control
⇒
see page 12
•
Sequence control
⇒
see page 13
•
Calendar control
⇒
see page 14
•
Graphic analysis
⇒
see page 15