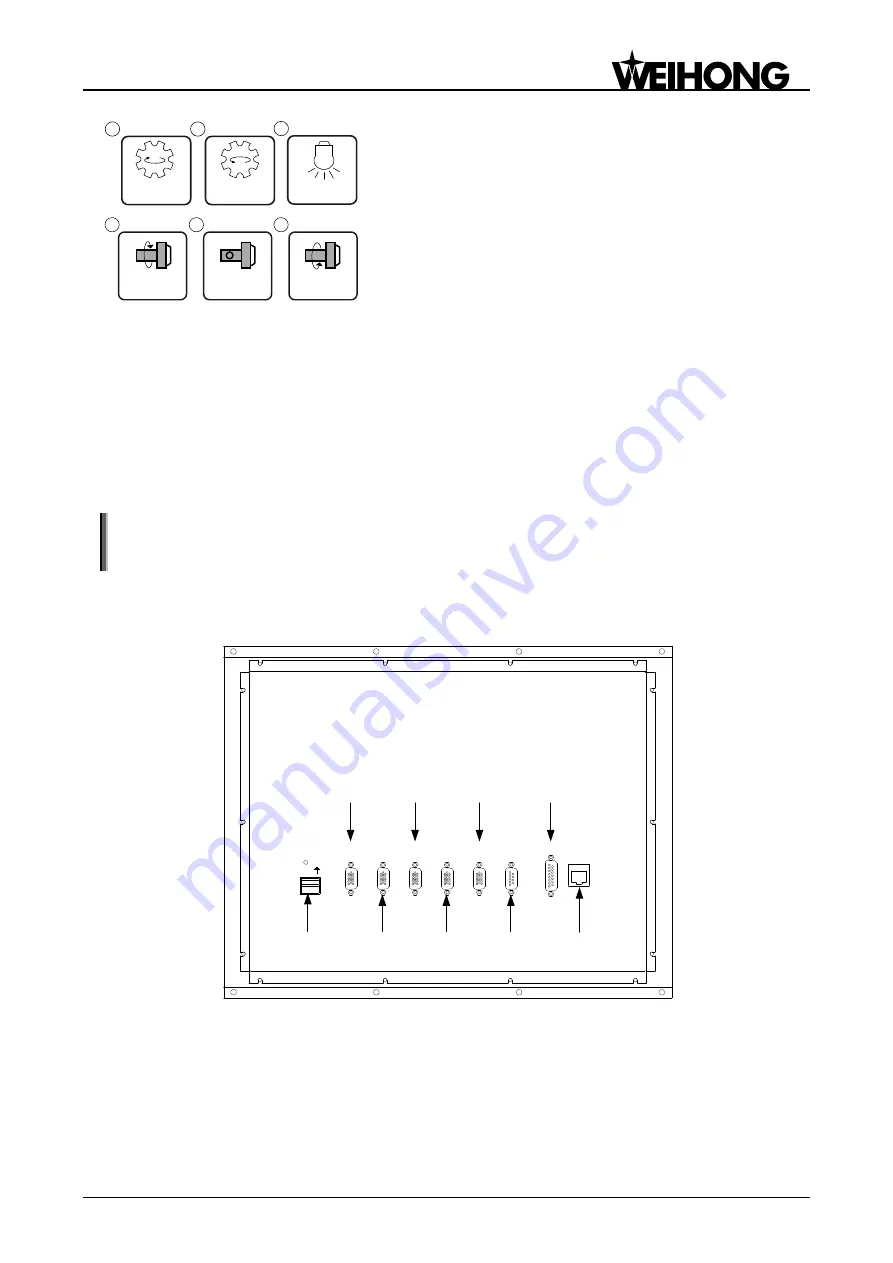
上海维宏电子科技股份有限公司
Weihong Electronic Technology Co., Ltd.
Specialized, Concentrated, Focused - 9 -
ATC CW
ATC CCW
Light
Tool
magazine
manipulation
buttons,
controlling tool magazine CW/CCW.
Light, used to control the lamp on/off.
CW
CCW
Stop
Controlling the spindle start/stop.
E-stop button: in case of danger, pressing this button will power off and stop the machine to ensure
the safety of the operators and machines. Press down this button to make machine stop
immediately and turn the button in clockwise direction to cancel E-stop.
Extended buttons: used for extended functions, including [K1], [K2], [K3], available for the extension
of custom functions.
Feedrate override knob / spindle rate knob: used to adjust the feedrate override and spindle
rotational speed. For details, refer to chapter 3.4 and 3.9.1.
USB interface: take off the nut cap and connect USB equipment.
Manipulation buttons: including F1~F7.
Note:
When the indicator light at the top left is on, it means the corresponding function is activated.
Rear View of NK280
The rear view of NK280 with its interface definition is shown as below.
24V power
interface
DC INPUT
24V2A
+
2
4
V
C
O
M
X
Y
Z
4Axis
5Axis
端子板接口
(I/O Board
Interface)
手轮
(MPG)
网口
(LAN0)
To X
driver
To Z
driver
To 5-axis
driver
To Y
driver
To 4-axis
driver
To I/O
board
To MPG
Network
interface
Fig. 1-4 Rear view of NK280
24V power interface: connected to 24V DC power.
To X driver: connected to the driver of X axis.
To Y driver: connected to the driver of Y axis.
To Z driver: connected to the driver of Z axis.