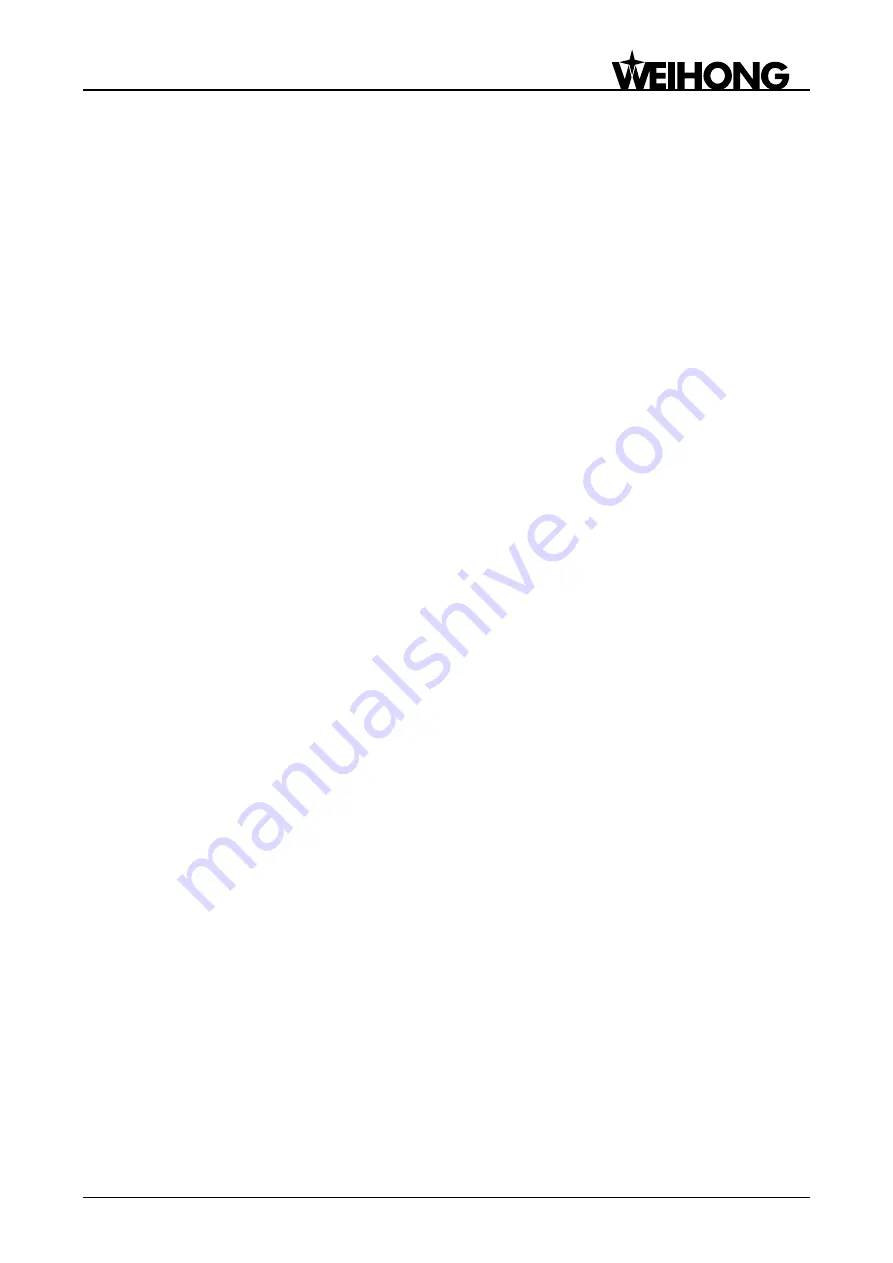
上海维宏电子科技股份有限公司
Weihong Electronic Technology Co., Ltd.
Specialized, Concentrated, Focused - 105 -
5.3
Common Troubleshooting
5.3.1
What should users do if the spindle does not rotate?
1) Check if there is an error in software. Press [Spindle Start] button and see if the dot before the
―Spindle‖ in [Port] screen under [Diagnosis] becomes green. If it does, the software works normally.
2) Start spindle start output, and check if the spindle start indicator lamp on the terminal board is on. If
not, check whether the connection cable of terminal board becomes loose. Close the host machine
and power off machine tool, and then re-plug the connection cable of terminal board. If it still does
not light, check if there is an error in cable of terminal board, terminal board or system. If it lights,
measure if the SPIN port is connected with a multimeter. If it is connected, the spindle start output
port works normally; if it is not conducted, there is an error in the relay of spindle start.
3) Test whether the analog voltage output is normal between SVC and GND with a multimeter. If not,
check if the connection cable of terminal board becomes loose. Still not, check if there is an error in
the cable of terminal board, terminal board and system.
4) Check whether the parameter setting of inverter is right, the spindle and inverter has been damaged,
or the wiring of the spindle and inverter is correct.
5.3.2
What should users do if an axis does not move?
1)
Check if there is output (in green) for ―× servo enable‖ signal of output port in [Port] screen under
[System]. If there is output, the software works normally. Check if the port polarity (it should be NO
―N‖) is set correctly.
2) Check if the parameter setting of servo driver is correct (like setting control mode as position control,
selecting pulse input port for Panasonic driver, etc.).
3) Check if the servo cable of this axis is well contacted at the joint with system host machine and
servo driver.
4) Check if something is wrong with servo driver, motor cable, servo cable or control system (e.g.
exchange servo cable and servo driver with those of other axes working normally).
5.3.3
What should users do if servo motor Z brake can’t be
opened?
Start the system and power on machine tool (eliminating system alarm signal), and see if the brake
output indicator lamp on the terminal board turns light.
1) If light, test whether there is 24V voltage between brake output ports (BRAKE-COM) with a
multimeter. If there is 24V voltage, check whether the wiring of motor brake cable is correct. The
motor brake cable should be connected to brake output port on terminal board directly.
2) If not, directly conduct the brake input ports (K+, K-) on terminal board with a conducting wire. If light
at this time, check whether the servo driver is enabled, the parameter setting related to brake output
of servo driver is right, and break output line of driver is correctly wired to terminal board (black line
is wired to K-, and only K+ is connected to with only one line); if still not light, please change the
terminal board.
5.3.4
What should users do if machine tool returns to the
machine origin abnormally?
Limit alarm or servo driver alarm occurs during backing to the machine origin.
1) Check if the software can receive the REF. point signal of this axis. The method is: trigger the home
switch, and then see if the color of the dot before the ―× machine origin‖ changes from red to green