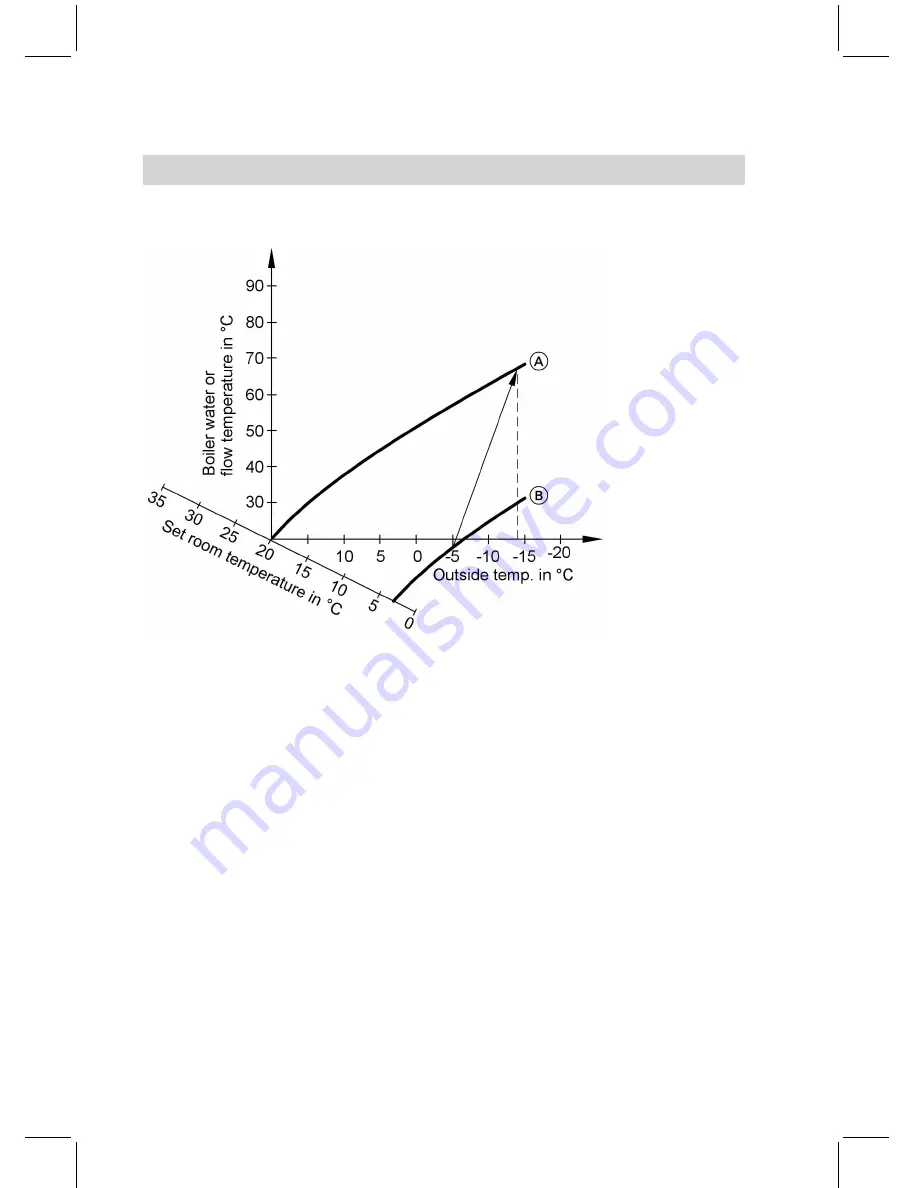
Example using the settings in the delivered condition
A
Heating curve for operation with
standard room temperature
B
Heating curve for operation with
reduced room temperature
Reducing the heat-up time
During the transition from operation
with reduced room temperature to
operation with standard room tem-
perature, the boiler water or flow tem-
perature will be raised in accordance
with the selected heating curve. The
boiler water or flow temperature can
be automatically increased.
The value and duration of the addi-
tional increase of the set boiler water
or flow temperature can be adjusted
in coding addresses "FA" and "Fb".
Control functions
(cont.)
92
Function description
5692
779
GB
Содержание VITOLADENS333-F
Страница 96: ...A1 Main PCB A2 Power supply unit Connection and wiring diagram external connections 96 Designs 5692 779 GB...
Страница 101: ...Parts lists cont 101 Parts lists 5692 779 GB...
Страница 102: ...Parts lists cont 102 Parts lists 5692 779 GB...
Страница 103: ...Parts lists cont 103 Parts lists 5692 779 GB...
Страница 104: ...Parts lists cont 104 Parts lists 5692 779 GB...
Страница 105: ...Parts lists cont 105 Parts lists 5692 779 GB...