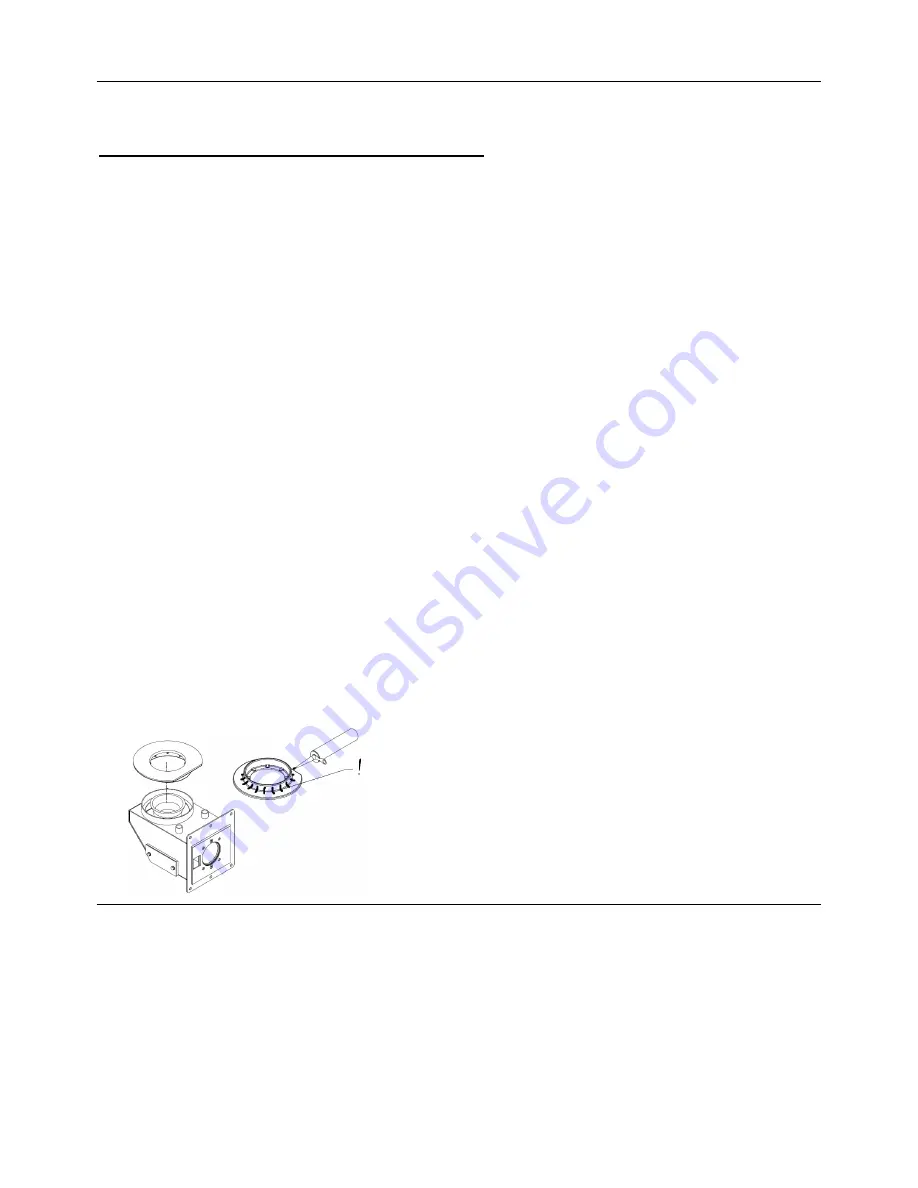
40
6.4
Verification activities before the boiler commissioning
Putting into operation can be performed only by a contractual service company authorized to carry out this
activity.
Before the boiler commissioning it is necessary to check:
a) filling the heating system with water
Water for filling the boiler and heating system must be clear and colourless, without suspended solids, oil and
aggressive chemicals. Water hardness must correspond to CSN 07 7401 and it is essential, in case the water
hardness does not comply, treat water in accordance with the Chap. 4.1. Even the multiple heating of water with
the higher hardness does not exclude salts depositing on the walls of the exchanger. Settlement of 1 mm calcite
reduces the heat transfer at a given point from the metal to water by 10%.
Heating systems with the open expansion tank allow direct contact of the heating water with atmosphere. During
the heating season the water expanding in the tank absorbs oxygen, which increases the corrosive effects while
there is a considerable evaporation of water. To refill, only water treated according to CSN 07 7401 may be
used. The heating system must be thoroughly flushed in order to wash out all impurities.
During the heating season it is necessary to keep a constant volume of water in the heating system. When
refilling the heating system with water it must be ensured that no air is sucked into the system. Water from the
boiler and the heating system must never be discharged or taken for usage except for the emergency cases like
repairs etc. Water discharge and filling with new water increases the danger of corrosion and scale
development.
If it is necessary to refill water in the heating system, refill water only into the cold boiler in order to
prevent damage of the steel base and the exchanger.
b) heating system tightness
c) connection to the chimney - must be approved by a chimney firm
A necessary condition to operate the boiler is the chimney lining due to possible formation of
condensation in flue gases due to their low temperature, especially at the min. boiler output. Lining
material must be resistant to chemical effects of condensate.
d) burner tightness
Plug the device into the mains (insert plug into the socket). By starting the fan via the display, the check of
the burner sealing is carried out. All air must flow into the combustion space of the retort and the cast iron grate.
The check must be focused on the bearing surfaces:
-
of the fan to the flange
-
around the burner cleaning hole
-
of the cast iron grate with the burner. In case a leakage appears, the grate must be removed, the old boiler
mastic must be removed from the bearing surfaces and an adequate quantity of new mastic must be
applied to them; then the grate is remounted to the burner. (Note: The cutting of the grate must be always
directed to the input of fuel feeder.)
Repeat the check.
Fig.
№
. 28
e) connection to the main
The boiler is connected through a flexible cord by means of a plug into a standard wall socket 230 V/
50 Hz/10 A. Protection against electric shock must be ensured according to CSN 33 2000-4-41 ed. 2.
f) water supply to the valve TS 130 or BVTS or STS 20
g) check the opening of chimney flap
The assembly completion and heating test execution must be recorded in the "Warranty card".
!
Apply boiler mastic to the marked point and put
the grate on the retort with the mixer. It is
necessary to ensure tightness between the
burner and the grate.