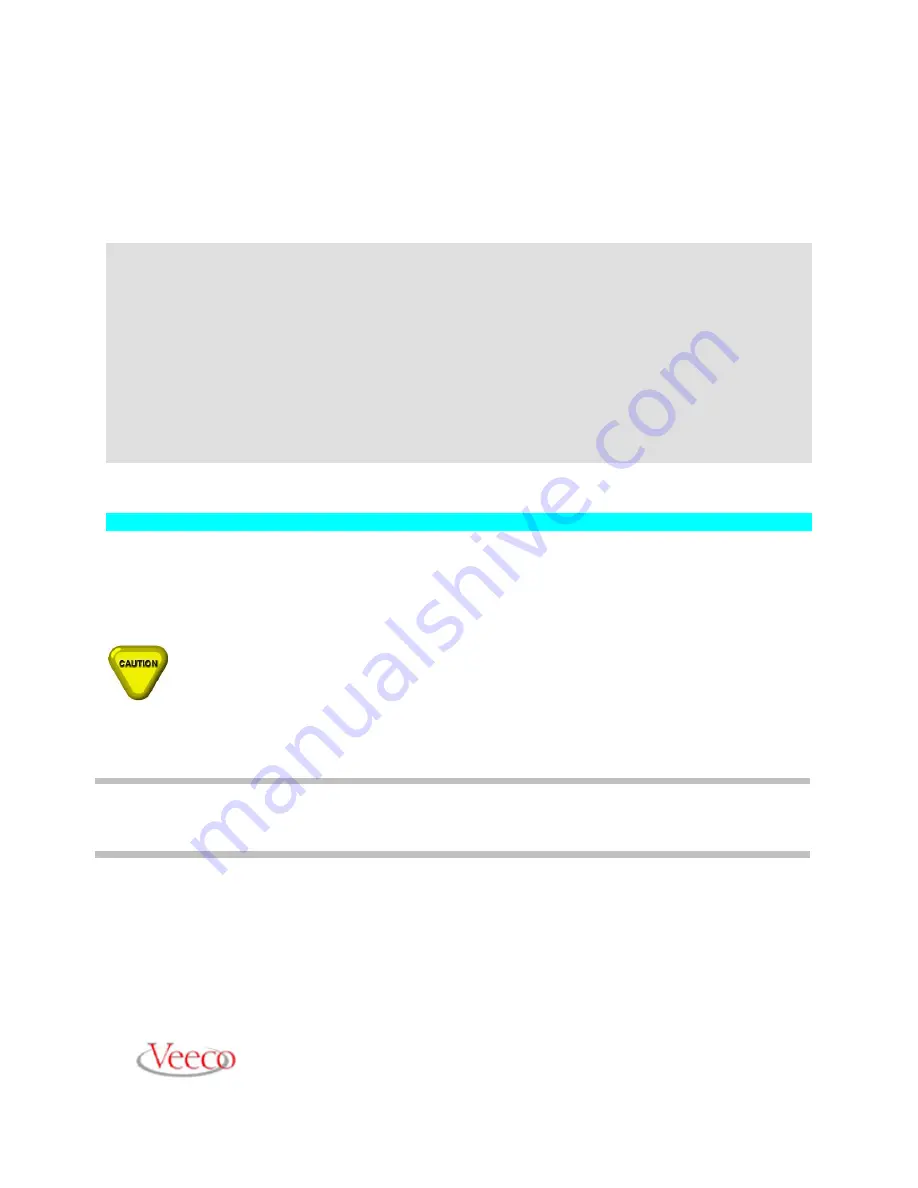
K465i Operations and Maintenance
P/N 1212831 Rev C
Page 4-50
Copyright
©
2012
Veeco Instruments, Inc. Confidential
All Rights Reserved
SETTING UP STATIONS FOR THE TRANSFER ROBOT
Each station of the robot is saved as a set of coordinates for the T, R, and Z-axes. These
coordinates need to be programmed (set) in order for the robot to move to that station
automatically. The stations for the transfer robot can be set using the
Lot Manager
control
software (or Nexus) or using the Genmark GB Tools software program.
Notes:
The lower-case station names (e.g.,
g
,
v
) and upper case station names (e.g.,
G
,
V
)
indicate specific vertical position-stations for the robot fork. A lower-case command puts the
fork directly above the rest position, with the weight of the carrier on the fork. An upper-
case command positions the carrier in a position to be lifted, with space between the fork
and carrier.
While it is easier to make adjustments to the stations with the system open, the system
stations should be taught with the system closed and under vacuum. The system can be
taught
at atmosphere
, with all stations being verified and needing adjustment when
at
vacuum
.
This procedure is used to teach a single station. Please repeat for the remaining shelves.
Procedure 4-19: Setting Up Stations for the Transfer Robot
1. Turn the servomotors on by entering SVN.
2. Home the robot with HOM command. This must be done without a wafer carrier on the fork.
3. Level robot by entering CLZ.
4. Open the necessary gate valve (for teaching the G or V stations only).
Caution:
When moving the robot arm manually use care to ensure that no part of
the robot fork comes in contact with the Transfer Hub chamber or passthrough. This could
damage the fork and/or cause the robot to become misaligned.
Note:
Movement of the robot in the R and Z-axes of 1 inch is equal to 10,000 units, and
for the T-axis 1 degree of movement is equal to 1,000 units. Use small increments when
positioning the robot to ensure the robot does not come in contact with anything.
5. Use the MVR command for the T, R and Z-axes to move the robot fork through the passthrough into
the glovebox. Small steps of 500 to 1000 are recommended. Carefully position the fork under the
wafer carrier.
6. Continue using the MVR commands to position the fork with an equal distance between its edges and
the sides of the carrier. If one side or the tip of the fork are too high or low, the tilt can be adjusted by
moving a specific Z motor elevator. The location of the Z1, Z2, and Z3 elevators in (Figure 4-14)
should enable an anticipated move.