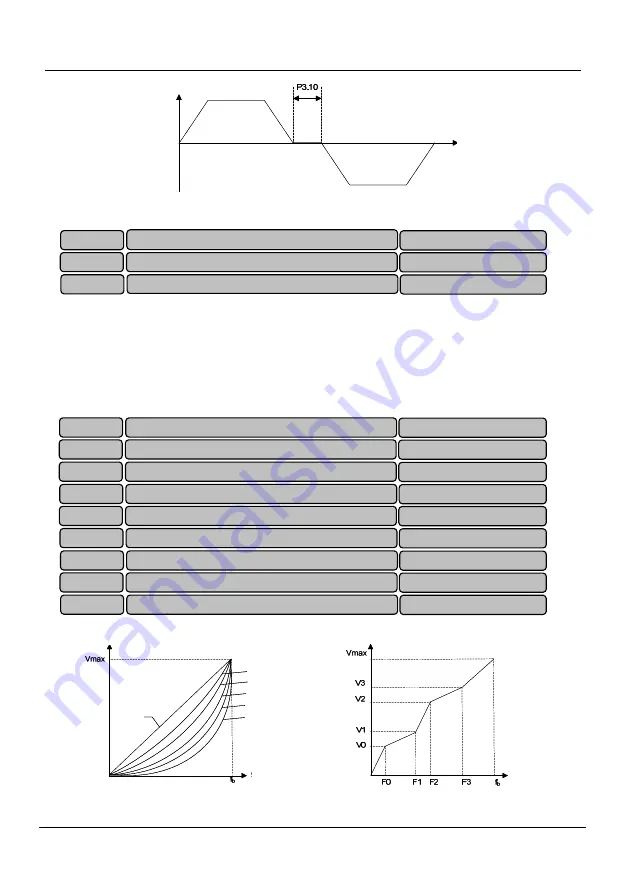
E5
−
H High Performance Universal Inverter User Manual
Chapter 6 Parameter Description
65
Figure 6
−
10 Forward/reverse dead zone time
P3.11 is the frequency set for jog operation.
Jog acceleration time P3.12: The time from zero to maximum frequency.
Jog deceleration time P3.13: The time from maximum frequency to zero.
When the inverter is in standby status, it can adopt jog operation. The jog operation command may come
from the operation panel, multi
−
functional terminal or host computer.
6.5 Multi
−
section Parameter (Group P4)
It is to determine the different V/F curves .
Figure 6
−
11 V/F curve Figure 6
−
12 Multi
−
section V/F curve
P3.11
Jog frequency
0.10~300.00 Hz (5.00Hz)
P3.12
Jog acceleration time
0.1~60.0 s(6.0s)
P3.13
Jog deceleration time
0.1~60.0 s(6.0s)
P4.00
V/F curve reference
0~6(0)
P4.01
V/F frequency value F0
0.00~300.00 Hz(0.00Hz)
P4.02
V/F voltage value V0
0.0~100.0 %(0.0%)
P4.03
V/F frequency value F1
0.00~300.00 Hz(0.00Hz)
P4.04
V/F voltage value V1
0.0~100.0 %(0.0%)
P4.05
V/F frequency value F2
0.00~300.00 Hz(0.00Hz)
P4.06
V/F voltage value V2
0.0~100.0 %(0.0%)
P4.07
V/F frequency value F3
0.00~300.00 Hz(0.00Hz)
P4.08
V/F voltage value V3
0.0~100.0 %(0.0%)
Output frequency
Time
Output frequency
Time
Output voltage
Output voltage
1.2-power
1.4-power
1.6-power
1.8-power
2-power
Output frequency
Output frequency
Straight line
Output voltage
Output voltage
1.2-power
1.4-power
1.6-power
1.8-power
2-power
Output frequency
Output frequency
Straight line