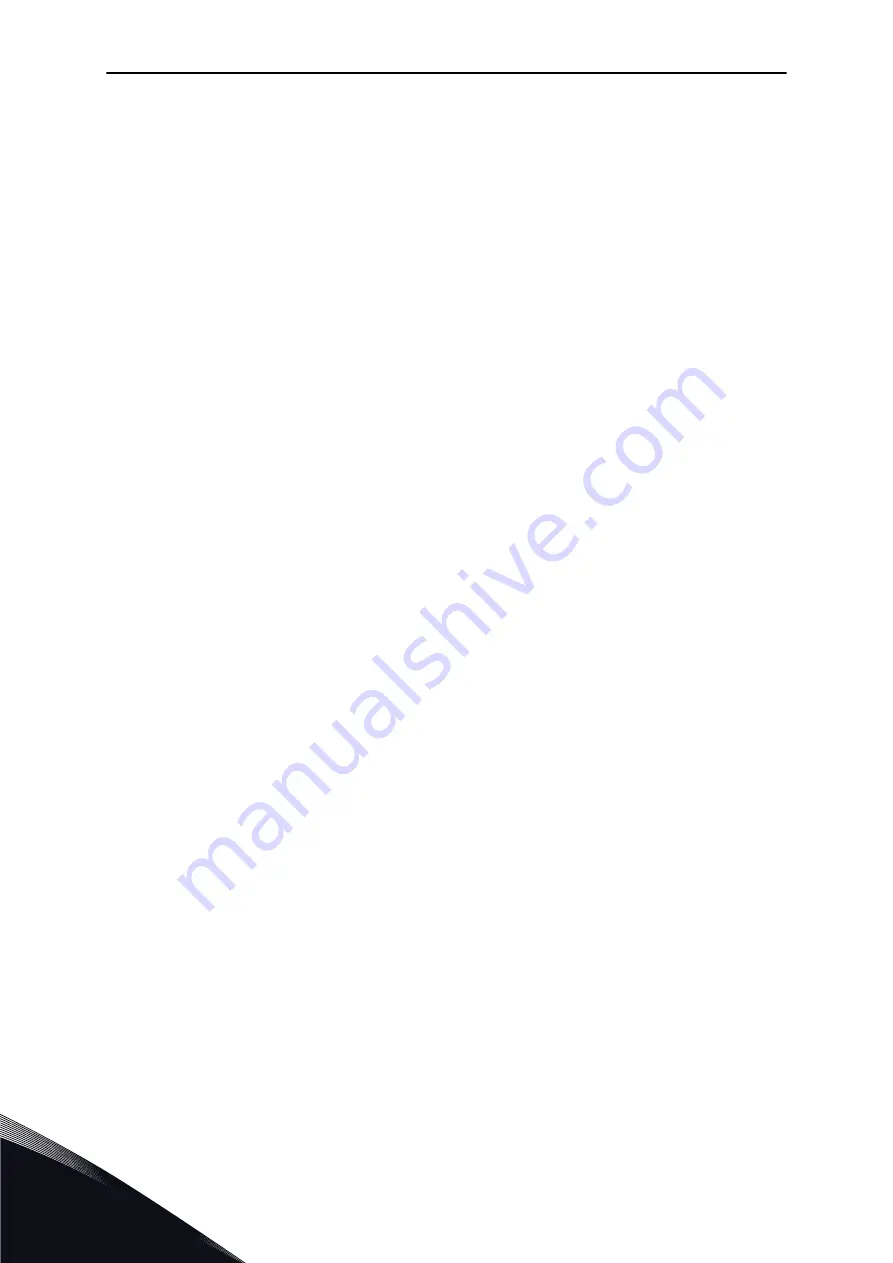
The bits can receive these values.
•
Search the shaft frequency only from the same direction as the frequency reference
•
Disable the AC scanning
•
Use the frequency reference for an initial guess
•
Disable the DC pulses
•
Flux build with current control
The bit B0 controls the search direction. When you set the bit to 0, the shaft frequency is
searched in 2 directions, the positive and the negative. When you set the bit to 1, the shaft
frequency is searched only in the frequency reference direction. This prevents the shaft
movements for the other direction.
The bit B1 controls the AC scanning that premagnetises the motor. In the AC scanning, the
system sweeps the frequency from the maximum towards zero frequency. The AC scanning
stops when an adaptation to the shaft frequency occurs. To disable the AC scanning, set the
bit B1 to 1. If the value of Motor Type is permanent magnet motor, the AC scanning is
disabled automatically.
With the bit B5 you can disable the DC pulses. The primary function of the DC pulses is to
premagnetise the motor and examine the rotation of the motor. If the DC pulses and the AC
scanning are enabled, the slip frequency tells which procedure is applied. If the slip
frequency is less than 2 Hz, or the motor type is PM motor, the DC pulses are disabled
automatically.
The bit B7 controls the rotation direction of the injected high frequency signal, which is used
in the flying start of synchronous reluctance machines. Signal injection is used to detect the
frequency of the rotor. If the rotor is in a blind angle when the signal is injected, the rotor
frequency is undetectable. Reversing the rotation direction of the injection signal solves this
problem.
P3.1.4.8 FLYING START SCAN CURRENT (ID 1610)
Use this parameter to set the flying start scan current as a percentage of the motor nominal
current.
P3.1.4.9 AUTOMATIC TORQUE BOOST (ID 109)
Use this parameter with a process that has a high starting torque because of friction.
The voltage to the motor changes in relation to the necessary torque. This makes the motor
give more torque at the start and when the motor operates at low frequencies.
The torque boost has an effect with a linear U/f curve. You can get the best result when you
have done the identification run and activated the programmable U/f curve.
P3.1.4.10 TORQUE BOOST MOTOR GAIN (ID 667)
Use this parameter to set the scaling factor for the motoring side IR-compensation when the
torque boost is used.
P3.1.4.11 TORQUE BOOST GENERATOR GAIN (ID 665)
Use this parameter to set the scaling factor for the generating side IR-compensation when
the torque boost is used.
VACON · 208
PARAMETER DESCRIPTIONS
10
LOCAL CONTACTS: HTTP://DRIVES.DANFOSS.COM/DANFOSS-DRIVES/LOCAL-CONTACTS/